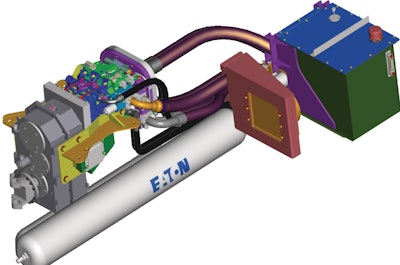
As a consumer, you can make changes to your daily lifestyle in order to counteract the effects of the rising fuel prices. Those options, however, don't suit the obligations of commercial vehicle users. Refuse has to be picked up, parcels need to be delivered, and the whole scope of other services still need to be provided, regardless of fuel prices.
The only practical response to rising fuel prices for nearly all of the vehicles used in these applications is to improve their efficiency, and the best technology available to do that today is hybrid technology.
A hybrid powertrain system reduces fuel consumption by blending the power generated by the internal combustion engine with power from other stored sources of energy on board. And of course, when you reduce fuel consumption, you also reduce the polluting emissions that are an inevitable by-product of burning hydrocarbon fuel.
Electric and hydraulic
There are two different kinds of hybrids, electric and hydraulic. Electric hybrids more easily support other on-board electronics and have a high energy density — best suited to applications that have a lot of cruising time because they can support longer engine-off operation.
Electric power is generated by the diesel engine and through regenerative braking, which recovers power which would normally be wasted as heat and brake wear. That power is then stored, typically in a battery pack, and delivered back to the truck through an electric motor that delivers energy back to the drivetrain, or to auxiliary power systems on the vehicle to power equipment or tools.
While electric hybrids have a high energy density, hydraulic hybrids have a higher power density which provides a better power boost for acceleration "off the line." The hydraulic hybrid systems work best with intensive stop-and-go applications such as residential refuse pick-up, because of the use of stored energy through regenerative braking.
According to NextEnergy, Detroit, MI, a non-profit corporation, a hydraulic hybrid system can recover and use up to 70% of the kinetic energy that is captured during braking. Hydraulic hybrid vehicles (HHVs) reuse stored energy that would normally be lost during braking in conventional vehicles, creating a cost effective system, while also eliminating idling and reducing engine operation for fuel efficiency.
Regenerative braking is a process by which the hydraulic kinetic energy from braking — which pumps low pressure hydraulic fluid into a high pressure accumulator — is stored for future use. As the fluid enters the high pressure accumulator, it compresses nitrogen within the accumulator, which then pressurizes the hydraulic system. The stored energy is used for accelerating the vehicle in conjunction with, or in place of, the engine.
Glenn R. Wendel and Travis W. Jackson, engineers in the Vehicle Systems Research Dept. at Southwest Research Institute (SwRI) write, "an important characteristic of nitrogen gas is that as oil is pumped into the high-pressure accumulator during braking, the gas pressure increases exponentially. Energy is stored as more and more fluid is pumped into the accumulator at higher and higher pressures." The stored compressed gas in the accumulator forces hydraulic fluid through a hydraulic motor to power the wheels.
Other benefits of hydraulic hybrid systems include the use of less-costly components, no battery requirement, and the use of composite material for reduced weight and more efficiency.
Work is being done to increase the maximum operating pressure, currently around 5,000 psi to around 7,000 psi. As accumulators increase in pressure capabilities, a hydraulic hybrid system will be able to sustain engine-off driving for longer periods of time.
"It is definitely not a question of one technology being better than the other. Hydraulic and electric hybrids simply have different ‘sweet spot applications," says Brad Bohlman, business development manager, Advanced Technology, Eaton's Fluid Power Group. "The choice of which to use in a particular application is highly dependent on the nature of the application itself, specifically the duty cycle of the vehicle in question.
"A key difference between today's hydraulic and electric hybrids is the duration of the power they can supply," says Bohlmann. "Hydraulic systems have high power density while electric systems have high energy density. For example, the Hydraulic Launch Assist (HLA) system delivers 300 hp from a motor that measures roughly 12 in. by 18 in., but it only does it for a short time, measured in seconds. An electric system will deliver less power at any given instant, but do it for an extended period of time, measured in minutes.
"So, if you look at vehicle duty cycles, a hydraulic hybrid power system makes a lot of sense for a large, heavy vehicle like a refuse truck that is constantly starting and stopping. There, you can capture the braking energy and re-cycle it over and over to improve operating efficiency.
"An electric hybrid tends to be ideal for something like a utility bucket truck that's driven to a jobsite and then sits in one place for extended periods with the engine idling to run the bucket and other systems. In that type of application," Bohlmann says, "you can charge the batteries on the way to and from the jobsite, and also capture braking energy, of course. Once on-site you can shut off the engine and run the bucket and other systems on battery power until the batteries need recharging. This could be up to several hours. At that point, the engine automatically restarts and fully recharges the batteries in a few minutes."
Series vs. parallel systems
Parallel system design keeps the traditional transmission and driveshaft system, and a pump/motor adds and subtracts power through the mechanical drive system. A parallel system does not keep the ground speed separate from the engine speed, but it still provides better fuel economy and lower emissions when compared to traditional drivetrains.
Series systems eliminate a traditional transmission and driveshaft system, allowing the ground speed and engine speed to be independent of one another. This allows the engine to be turned off when not needed, like when stopped or accelerating, and for the engine to run at its best efficiency. In both a series and parallel system, some vehicles can actually downsize their engine without losing any functionality, resulting in even more fuel savings.
Hybrid-electric trucks
Eaton is a leading provider of diesel-electric hybrid power systems for truck and bus applications on three continents, and is also developing hydraulic hybrid power systems technologies for use in refuse trucks, delivery vehicles, buses and other applications.
The Model 335 Hybrid Electric truck from Peterbilt Motor Co., Denton, TX, a division of PACCAR Inc., can be used in both utility-boom, and pickup and delivery applications when equipped with a PACCAR PX-6 engine and an Eaton hybrid power system.
The Model 335 Hybrid Electric utilizes components that provide up to a 30-40% improvement in fuel efficiency, when configured for a utility application. These fuel savings are realized through both an on-road fuel economy gain and an 80% reduction in engine idling through electric operation of the power take-off (PTO) using the on-board lithium-ion batteries.
Available with a 26,000-lb. GVW rating, it can be configured for non-CDL (commercial driver's license) operation with hydraulic brakes for a greater range of driver options. The integration of the Eaton Hybrid Drive System and the 260-hp PACCAR PX-6 engine delivers up to 860 ft.-lbs. of torque.
PACCAR's other division, Kenworth Truck Co., Kirkland, WA, offers a medium-duty, hybrid-electric truck for utility operations. The Seattle, WA, King County Dept. of Transportation, the first government agency to place the Kenworth hybrid into service, uses its Kenworth Class 7 hybrid to maintain traffic signals.
The hybrid is equipped with a utility bucket atop a 50-ft. boom, which is longer than a standard aerial lift. While a non-hybrid utility truck must idle to operate its lift, the hybrid's lift typically operates on electric power, which reduces emissions.
After just over 5,000 miles of operation, the hybrid has already achieved a 25% reduction in fuel consumption over a comparably equipped conventional model, says King County Fleet Administration Div. Director, Windell Mitchell. The county also uses B20 biodiesel as its fuel for added environmental friendliness.
Kenworth's medium-duty hybrid, which can carry a payload of up to 16,000 lbs., features an integral transmission-mounted motor/generator, frame-mounted 340-volt battery, and dedicated power management system. Above 30 mph, the Kenworth hybrid operates like a standard diesel vehicle with all power coming from the engine during steady driving conditions. Below 30 mph, it uses a combination of diesel and electricity with the system automatically switching between the two modes of operation. Electricity generated through regenerative braking is stored and used for acceleration, assisting the diesel engine.
Plug-in vehicle
Odyne Corp. is currently in a project with DUECO Inc., Waukesha, WI, to develop a proprietary plug-in hybrid electric vehicle propulsion system for aerial lift truck applications, explains Roger M. Slotkin, CEO, Odyne Corp., Hauppauge, NY.
"It takes 0.8 gallons to one gallon per hour of fuel just to idle," he explains. "Put that at a 10-hour day, for five days a week, and that equals 40 to 50 gallons a week."
Slotkin continues, "We're taking our strength of battery management systems to give the ability to continue operating the aerial device without running the engine. There is less environmental pollution and there's no exposing the workers to those environmental contaminants as well."
To eliminate engine idling, Odyne's technology allows DUECO's trucks to be plugged into the power grid at night, providing enough power to work at job sites with the engine off, thus reducing emissions, noise pollution, and fuel use. The Odyne system will allow for virtually unlimited charging in the field should the truck's mission be extended due to emergencies or extenuating circumstances. In those cases, the on-board internal combustion engine would provide the generating power.
"The U.S. fleet of Class-6, -7 and -8 gas and diesel vehicles consumes 45% of the imported fuel and contributes to about 80% of the pollution from fuels.
"New York has high energy costs," he says. "Our grid is producing energy and at night, it is not being consumed. If we could use energy from the grid during off-peak hours, it would be a win-win. It also offers a sharp reduction of CO2 and other airborne contaminants."
Mail Delivery
"The Postal Service has the largest vehicle fleet in the nation, and probably the world today," says Han Dingh, program director, vehicle engineering for USPS. "Every year we consume about 125 million gallons of fuel, and we drive about 1.2 billion miles per year. It has been estimated that every extra penny in fuel cost adds an additional $8 million in annual operational costs.
"USPS had an agreement with Azure Dynamics, Vancouver, BC, Canada, to convert one of our step vans to a hybrid-electric vehicle," Dingh explains. "That van is a parallel hybrid. We kept the original 6.5-liter diesel engine, and Azure Dynamics added a 35 Kw induction motor, plus an ultracapacitor used for energy storage instead of a battery."
Hydraulic hybrids
Hydraulic hybrids have been on the rise, gaining in popularity due to their better fuel efficiency. However, the low energy density makes it an unlikely candidate for vehicles driving constant speeds for extended periods of time, such as over-the-road trucks. However, the improvements in storage capacities, as mentioned earlier, are allowing more hydraulic hybrids to surface.
A pressurized hydraulic accumulator can handle a high-energy transfer cycle better than a battery, and it is more cost-effective than an ultra-capacitor system. Additional benefits include greatly reduced brake maintenance and the potential to use the hydraulic reservoir to power attachments or other equipment, rather than driving a separate hydraulic pump.
The U.S. Environmental Protection Agency (EPA) partnered with Eaton to fabricate EPA's integrated hydraulic rear-drive for a United Parcel Service (UPS) package vehicle. The two power sources were Eaton's hydraulic hybrid components and the EPA Clean Diesel Combustion engine.
Eaton's series hybrid hydraulic drivetrain component in the hydraulic system contributed to the UPS truck's 45-50% better fuel economy than a truck with a standard chassis.
The Clean Diesel technology was developed by International Truck and Engine Corp. in cooperation with the EPA Advanced Technology Div. under a Cooperative Research and Development Agreement.
The engine is a combination of diesel fuel injection system performance im-provements, refined air management systems and an improved combustion system, capable of meeting the 2010 NOx standards without NOx after-treatment.
The EPA estimated that if manufactured at a high volume, the added costs of the hybrid components would pay for themselves in three years through lower fuel and brake maintenance costs.
Activity like this has encouraged component suppliers and OEMs to start nudging their hybrid programs from prototype and pre-production stages to actual assembly line production.
Mass production
In August of 2007, Eaton announced the commercial availability of it medium-duty hybrid power systems. The systems are now being sold and delivered to customers on the 2008 chassis of several major North American commercial vehicle manufacturers. These include International Truck and Engine Corp., Kenworth Truck Co., Peterbilt Motors and Freightliner Corp. The announcement followed more than four years of development and two million miles of successful field-testing in North America, Europe and Asia.
According to Kevin Beaty, manager of Eaton's Hybrid Power Systems business unit, the company plans to produce several hundred systems in 2007. Eaton is planning to ramp-up production capacity over the next three years in order to meet customer demand and achieve economies of scale.
More than 220 hybrid-powered vehicles with Eaton's advanced technology systems have been produced to date for testing and evaluation — most of which have been placed into service alongside their conventionally-powered counterparts. Vehicle configurations include package delivery vans, medium-duty delivery trucks, beverage haulers, city buses and utility repair trucks, each of which has generated significant fuel economy gains and emission reductions.
Fleet customers for Eaton hybrid power have so far included FedEx Express, UPS, Coca-Cola Enterprises, The Pepsi Bottling Group, and 14 public utility fleets into which were placed 24 hybrid-powered repair trucks. Truck body builders also involved in the delivery of new vehicles include Altec Industries of Birmingham, AL, Terex Corp. of Westport, CT, and others. Additional testing is taking place in Europe with DAF Trucks, and in Asia with the Beiqi Foton Bus Co., one of China's largest commercial vehicle producers. Eaton hybrid power systems in these and other applications are generating fuel economy improvements of up to 60% and significant reductions in harmful emissions.
"Financial incentives at the local, state and national level will help encourage early adoption," said Beaty. "Meanwhile, increased production volumes will help drive down the per-unit cost of the systems and empower the industry to offer a compelling value proposition that is sustainable."
Beaty added that Eaton is looking forward to significant government-related purchases of hybrid-powered trucks for its fleet operations noting that many of these same government agencies are also offering the purchase incentives. "We hope to see hybrid power encouraged and mandated in ways similar to what is being done today for alternative fuel vehicles," said Beaty.
Eaton, which supplies electric drives and power systems to several hybrid systems, is also aware of the shifting momentum: "What's happened recently is that we, with a number of our suppliers, are ramping up to more of a production offering, so that these fleets can buy in higher volumes at lower prices," says Kevin Beaty, business unit manager for Eaton Truck's Hybrid Power Systems unit.
As environmental concerns continue to gain momentum, the requirements for emissions will stiffen. As fuel prices climb, so too will the demand for better fuel-efficiency. Hybrids possess the ability to not only save money, but the Earth as well. These "green machines" are a driving motivator for the continued pursuit of energy-smart technology.