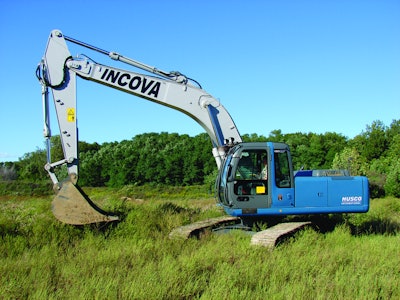
The National Fluid Power Association (NFPA) aims to advance the fluid power industry and the companies within it through its industry events, learning resources, research projects and other services.
In 2009, the NFPA gathered a team of representatives from member companies and the CCEFP to put together the Technology Roadmap for the Fluid Power Industry. The goal was to outline a research and development agenda that would allow the fluid power industry to help meet the future needs of fluid power customers, expand fluid power into new customer markets, and attract young engineers to the industry.
The six main research and development (R&D) challenges faced by the fluid power industry (which can be found at www.nfpa.com), as determined by the Roadmap team are:
- Increasing the energy efficiency of fluid power components and systems
- Improving the reliability of fluid power components and systems; for example, increasing uptime, eliminating leaks, reducing maintenance requirements, and making fluid power safe and easy to use
- Reducing the size of fluid power components and systems, while maintaining or increasing their overall power output
- Building “smart” fluid power components and systems; for example components that can perform self diagnostics/prognostics and troubleshooting integrate easily with “plug and play” functionality, etc.
- Reducing the environmental impact of fluid power components and systems such as noise and fluid leaks
- Improving and applying the energy storage, recovery and redeployment capabilities of fluid power components and systems
According to the NFPA, only part of the action plan is to be led by the NFPA itself. The full achievement of the association’s goals will be, in large part thanks to the involvement of individual member companies incorporating the Roadmap objectives into their own product innovations and strategies.
Jeff Herrin, Director of Advanced Programs at Sauer-Danfoss, Ames, IA, states. “The Roadmap is a very high level set of prioritized directives in the industry because it’s from the consolidated voice of industry partners,” he says. “The topical areas were identified as critical for the industry as a whole, so many of them are already on manufacturers’ radar.” What the list does assist manufacturers with is prioritization of their own projects.
According to Herrin, Sauer-Danfoss had all of the Roadmap challenges on its radar, but found it challenging to prioritize the drivers, “The Roadmap helped us prioritize in terms of where our investment flow should be for R&D,” says Herrin. “We’ve had a lot of investment and focus on energy efficiency. As a provider of both components and system solutions, we’re addressing it from both sides, looking at the core fundamental technology pieces like pumps ,motors and valves, but also looking at configuring system solutions out of those components and bringing software and electronics to them to create more efficient solutions. We are striving to offer pre-configured hardware/software solutions that can help our customers as they become more and more challenged with the energy efficiency of their vehicles.
HUSCO International., Waukesha, WI, too had members on the Roadmap development team, and saw parallels to its own internal project goals and the NFPA’s Roadmap. Joe Pfaff, HUSCO’s Vice President of Corporate Development Engineering, says the first thing to do when addressing the R&D challenges is to determine how today’s solutions are not satisfying customer’s needs. Next is to link what key characteristics or features are needed to address those needs, and then to gain the fundamental knowledge on how to create the innovation and new products to solve the market’s technical challenges.
“When you think about the increasing engine emissions regulations, the increased cost of fuel, the increased use of off-highway equipment in developing countries, and the high cost of fuel in those developing countries, that is creating a huge market demand—need—to improve efficiency.”
Sauer-Danfoss, too, is challenged by the Tier regulations. “With the new Tier 4 engine emissions challenges where a whole new engine type is entering the marketplace, the need to integrate existing components with new engines and new controls is one of the big technical challenges our customers have to deal with,” says Herrin.
In regards to the Roadmap, increasing energy efficiency, building smart components, and at the end of the day reducing environmental impact are all initiatives for tackling engine technology and emissions reduction systems. Sauer-Danfoss isn’t measuring the emissions of the new engines, but rather working with the engine interface with its control system. The new engine models interface with control systems in the same basic way, but the engine behaves differently.
“I can talk to the engine the same way, but if I ask the engine to go from 1,000 rpm to 2,500 rpm, what used to take three seconds now takes only one second,” says Herrin. That is a big deal for the hydraulic system provider, which is currently going through its components and systems to appropriately adjust them to react with the new engines.”
As a valve manufacturer, HUSCO needed to be experts in how to increase valve efficiency. The company has tested over 18 machines to quantify the energy transfer from the fuel coming into the machine, being transformed to the engine, through the pump, thorough the valve, to the actuators. “We needed to understand the overall efficiency of the machine system to understand how to design a better valve system. With this understanding we’re now designing valve systems within the context of the application’s machine efficiency resulting in both more efficient and cost effective solutions.,” explains Pfaff.
To better understand the inefficiencies of the valves of the hydraulic system, HUSCO gathered information from the entire hydraulic system. “It’s not making a more complex product in a lot of cases,” Pfaff says. “It’s making a more refined product. That’s where you find the cost savings, a reduction in components while simultaneously improving efficiency.
“The knowledge we’ve gathered has enabled us to make better refinement on existing products, and it has given us the insight to develop new products that aren’t dependent on new technology. They’re still spool valves and still using existing design and manufacturing know-how, but they are arranged in a unique way that dramatically improves their efficiency while simultaneously lowering the cost.”
Control valves today range in efficiency from 25% to around 60%. That is a 35% opportunity to improve efficiency just by simply refining already existing technologies. “From testing, analysis and development we’ve done, the most efficient valve on the market has the opportunity for another 15 to 20% improvement in efficiency” says Pfaff.
HUSCO owns a 20-ton excavator for their development of new hydraulic solutions. The excavator is equipped with a hydraulic system that allows a complete degree of freedom on how flow, pressure and power are controlled throughout the whole system. It uses the INCOVA system’s independent metering system along with a rapid prototype controls system utilizing Mathwork’s Simulink. This allows the company to develop iterations of the spool valve system and test it on the machine without having to wait for the physical housings and spools.
“Also, with the data acquisition and data analysis, certain tools were developed to be able to characterize the inefficiencies and understand how to manage them,” says Dwight Stephenson, senior vice president engineering, HUSCO Intl. When a machine is tested, there are hundreds of signals and gigabites worth of data being collected, so summarizing the information and presenting it to an engineer in a useful way can be a challenge in and of itself.
Products and their (R&D) Challenges
Within the last 12 months, HUSCO has been applying their system knowledge to develop a better valve—two to be exact. “The FSX and the SBX were both developed on the foundation of the system efficiency we developed in the last two years. Both of these valve systems have delivered over 20% improvement in overall machine efficiency using fewer components than standard competitive products and are lower in cost,” says Pfaff.
The valves were developed with the first and second main R&D challenges in mind: Improving energy efficiency and improving the reliability of a component or system. “The second challenge may be even more important than the first,” says Pfaff. “How these pieces fit together, and the level of refinement you are able to bring to it is one of the keys to improving overall machine efficiency.”
As a subsystem integrator, Sauer-Danfoss has found itself directly challenged by the Tier regulations, a hurdle that had not been anticipated by engine system integrators when the emissions reduction announcements were made. Most had assumed the engine system would run slower, would take up more space under the hood, would rob other systems of energy for turbo charging and exhaust gas recirculation; but what had not been anticipated was the change in engine dynamic behavior. “With the new Tier 4 engine emissions challenges driving new engine designs and controls, the need to integrate existing components with these new engines and controls is one of the big technical challenges our customers have to deal with,” says Herrin.
“We can interface to the engine the same way mechanically and electronically, but the dynamic response and inertia of engines vary and that impacts the downstream controls directly,” says Herrin. That is a big deal for the hydraulic solution provider, which is going through its components and control systems to ensure proper integration with the new engines.
In regards to the Roadmap, increasing energy efficiency, building smart components, and at the end of the day reducing environmental impact are challenges Sauer-Danfoss is addressing.
The company is working to develop turn-key solutions for its customers to aid in the integration of its products with new engines. This is achieved through the company’s vehicle control platform, PLUS+1, which acts as a development environment to efficiently link hardware components with control software.
“Best point control is a technology area all system integrators are working on,” says Herrin. “By using new software algorithms to allow us to integrate our propel and working hydraulics functionality with the both the engine and vehicle controls, the entire machine can be operated in a more efficient way than we have in the past, without having to sacrifice productivity.”
While you can always make design improvements to the components themselves that will translate into a more efficient vehicle, there are oftentimes bigger opportunities in finding how best to integrate and operate those components simultaneously with one another to create the best point of operation through looking at the entire system, instead of looking at just the component controls.
CCEFP
The Roadmap also helps to guide the research efforts of the Center for Compact and Efficient Fluid Power (CCEFP) and the grant program of the NFPA. The objectives of the Roadmap helped the NFPA to determine that the next area of focus for grant work would be the development of new fluid power sensors. While there are sensors available to measure parameters such as contamination, pressure, differential pressure and flow, the high cost and sparse availability inhibits broad implementation on fluid power systems.
This new research project, according to the National Fluid Power Association’s Education and Technology Foundation’s Chairman Gregory Willard, “is envisioned to lead to sensors that could be broadly used to improve the operation, reliability, efficiency, and maintainability of hydraulic and pneumatic systems—and cost one of two orders of magnitude less than the current technology.”
Headquartered in Minneapolis at the University of Minnesota, the CCEFP is currently undertaking 24 research projects and 4 test beds. One of the four test beds being developed though the research program of the CCEFP is set to be highlighted at the 2011 IFPE show at its booth (#13004)—a high efficiency excavator.
Under development at Purdue University under the direction of Professor Monika Ivantysynova, the excavator is a platform to demonstrate the many research advances throughout the CCEFP. The primary question the test bed sought to answer was, what the technological barriers, solutions and potential for displacement controlled actuation and hydraulic hybrid technologies were in order to be successful in drastically improving fuel consumption in multi-actuator mobile machines.
The test bed began as a study of new system concepts based on throttle-less actuator technology and a demonstration of fuel savings, improved performance and system compactness using the throttle-less actuator for the construction, agricultural and forestry machinery. The excavator program also hoped to study and demonstrate effective control strategies for complex multi-actuator systems, including new human-machine interfaces.
After June 2010, the product focus shifted to develop the excavator with improved fuel economy and a reduced engine size that used displacement controlled hydraulics and hybrid technologies.
The test bed is based largely on the results from the Project 1A2: Optimal Power Management for Mobile Fluid using Displacement-Controlled Actuators, though results from other technologies developed from other projects through the CCEFP (see Compact, Effective, Compact in OEM Off-Highway’s ____ issue for more on the CCEFP’s Project 1A2).
A Bobcat 435 excavator had its load sensing hydraulic system replaced with a displacement controlled hydraulic system. The new system shows an average of 40% fuels savings than the Bobcat 435 excavator standard model. All functions are controlled electronically with the displacement controlled hydraulic system allowing the use of the advanced control strategies. Advanced power management control minimizes machine fuel consumption according to the work cycle being performed, and the improved efficiency offers lower working temperatures for the hydraulic fluid for longer fluid life and less maintenance and thus machine downtime.