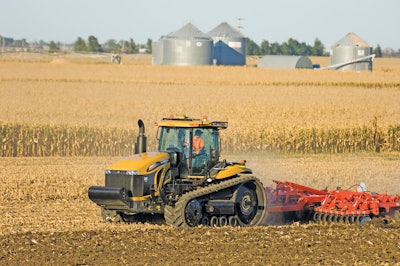
The precision system industry is one of the hottest developing trends in the off-road equipment industry. Its benefits are easy to identify, operator training is minimal thanks to technology transparency and ease-of-operation, and thus the adoption rate of the technologies from bolt-on option to integration at the OEM level can be relatively quick.
The first step in technological adoption is a small 1% of leading-edge OEM adopters, then another 2% to 5% follow. “After about 5%, you cross a chasm into more mainstream adoptions,” says Michael Gomes, Director of Marketing Topcon Precision Agriculture, Livermore, CA.
In order for a technology to go mainstream, it must create a value for the user, be easy to use and be usable over a reasonable time of the year. For example, on-the-fly nitrogen sensors are available through three different manufacturers currently. The technology has been in the commercial marketplace for around 10 years, yet the adoption rate is low. The value of the technology has not yet been widely accepted by equipment users and operators.
The automatic steering system’s abnormally fast adoption (within four years) is unique. “It created tremendous value to the end user,” says Gomes. “You could double the hours of usage of a tractor during, for example, spring planting season. People who had multiple tractors averaging 400 operating hour increased to 800 to 1,200 operating hours. The ability to operate day and night with repeatability essentially turned two tractors into one. Those kinds of trends get immediately recognized by tractor companies.”
AGCO saw a strong benefit with auto-steer for its swather equipment, which typically runs late into the day or extremely early—working around moisture levels. The equipment would be run at a tedious speed (maxing out around 8 miles per hour) for 16 to 20 hours in a day. Adding the auto-steer technology gave the operator the same level of control of the machine, yet helped him to operate the machine more safely and responsibly.
Working with an OEM
“We start off working with the OEM who is paying close attention to the market, what the market is adopting, and what technology is proving to be the most viable in the aftermarket marketplace so it can be integrated into the OEM’s machine as an option,” says Gomes. “OEMs are looking to offer the latest cutting-edge features on their equipment because in order to stay competitive they need to offer the most efficient piece of equipment on the market.”
Discussions with the OEM determine how it sees the technology strategy fitting in with its product line and functionality offerings. In many cases, the OEM will test the technology to a number of standards separate from aftermarket standards.
In many cases, the solutions start as a bolt-on option after it has proved market viability and acceptance with the right feature sets and price point. Over time, the OEM works to integrate the technology functionality into the machine so it can be an internal property, which also lowers the total cost of the technology, its development and integration.
Topcon as a company is trying to take aftermarket to OEM adoption to the next level by working more closely with OEMs to understand its release process, its testing process and how these ideas apply to Topcon’s technologies to figure out if the development process needs to be altered.
Collaborative engineering agreements
Topcon has been working with OEMs like AGCO and Komatsu for years. In late September, the company announced a cooperative agreement with Same Deutz-Fahr (SDF), a leading manufacturer of tractors, combines, engines and other agricultural equipment.
The agreement allows for both engineering departments from Topcon and SDF to develop custom precision systems and products (under the Agrosky brand name) specific to SDF equipment.
Recently the company began a strategic partnership with Amazone, a supplier of a complete range of professional arable farming solutions, to provide hardware components and expertise for automatic steering systems and section control for a complete range of professional farming solutions.
The initial project of the partnership was the development of user-friendly content for an ISOBUS-operator terminal with a unique Amazone functionality, the AMAPAD ISOBUS terminal, which was presented at Agritechnica 2011 in Hannover, Germany.
The system’s AgApp (Agriculture Applications) concept allows third-party software to be loaded into an operator terminal so independent developers can be fully integrated into the console interface. Most operator terminals are closed systems with limited functionality for a dedicated implement. With the AgApp concept, the end user can select the application best suited to individual needs for any piece of farm machinery so the operator can quickly decide which sensor technology to use.
“Hardware is always standard, and for OEMs specifically, hardware has to be produced to a global standard,” says Gomes. “But, when it comes to user requirements for different market places, that is where the regional differences come in.” In North America, there are places that have been farming for between 150 and 300 years, while in Europe farming systems have been in existence for 3,000 years.
Depending on geographic location, positioning technology can also operate differently dependent on the latitude or longitude and the number of satellites in orbit that can offer a strong signal for precision systems. GPS (global positioning systems – the U.S.’s constellation) works well in certain locations, and poor in northern latitudes. Topcon’s technology utilizes several constellations for additional accuracy and reliability in more locations around the world, allowing it to work with European-based equipment giants like Same Deutz-Fahr and Amazone.
Technology on the rise
Gomes sees three particular technology systems that are catching a foothold in the off-road equipment market. The first is telematics systems and a growing understanding of how it can be leveraged as a business strategy in addition to creating a value for the end user. Sensors including optical sensors, ultrasonic sensors and flow rate sensors used in conjunction with GPS-based automatic steering precision systems create an integrated and intelligent machine. Also, coordinated machine systems are also gaining attention in the industry.
“The equipment is big. The equipment is powerful. The next thing that is happening is the equipment is becoming smart,” says Gomes. The precision systems are allowing more than just job efficiency. They are now able to provide layers of performance data and other valuable information from which an owner or OEM can extrapolate operation patterns and best practices. Whether it is up-front job planning to figure out how much time a job will take with particular equipment with a specific route, to supplying records proving on-time schedules, output and regulation compliance, the data from precision and automated systems is becoming invaluable.
Optical sensors emit an infrared laser through the plant leaves. Based on the refraction, the sensor can determine whether the plant needs more or less nutrients, water or fertilizer and execute a decision immediately.
Individual nozzle control systems provide flow rate shut-off control for individual nozzles through pulse-width-modulation solenoid valve technology. The ability to adjust a single nozzle’s flow rate means boom overlap during a pass over a crop row will not cause excess spray on crops that have already received it. This also allows for application compensation during boom speed variance--such as when a sprayer turns causing the inside nozzles travel at a slower velocity than outside nozzles.
Ultrasonic sensors, when placed on a sprayer’s boom, can control boom height for optimum spray pattern during chemical application. NORAC Systems Intl. Inc., Saskatoon, SK, Canada, offers spray height control systems which include ultrasonic sensors mounted on the left, right and center sections of the boom. The boom automatically follows the contours of the land and maintains a preset height above the ground or the top of the crop. Roll control technology enables the system to monitor and compensate for roll in the center section. Proportional valves ensure height corrections are smooth, even and automatic.
Many of these instant decisions are not being made by the operator anymore. Technology transparency means based on programmed operator input the machine is able to sense, evaluate and execute a decision without the operator having to actively do anything. “Increasingly operators have to make many “simple” decisions quickly, and automation improves that situation for the operator,” says Gomes.
Working with OEMs forces technology developers to push themselves harder to make their technology more reliable. “As you begin to work with OEM customers, it makes you better at producing higher volume at lower cost, because when you align yourself with an OEM, their standards are higher for service and support. That’s the only way you’re going to push yourself to the next level,” Gomes concludes.
“It’s more about an OEM-philosophy of doing business than it is about working with one specific OEM.”