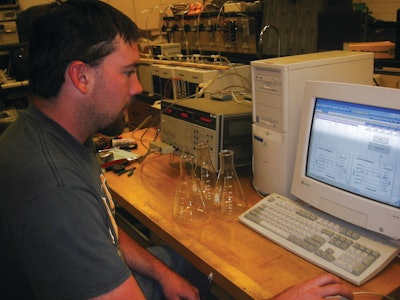
Degradation and contamination of the working fluids is a major cause of failures in hydraulic systems. Increases in contaminant levels and changes in fluid properties can be both an indicator of deteriorating component conditions and a cause of component failure. Low cost sensors that give early warnings of fluid problems could add significant value to hydraulic systems by providing an opportunity take corrective action prior to failure.
Robustness in sensing fluid contaminants in real-world operating environments is difficult because of the variability in the fluid state and the variety of possible contaminants. While there are ample examples of sensors measuring the conductance or dielectric constant of oils, those sensors either do not acquire multiple measurements across the dielectric spectrum or do not use multivariate models to predict parameters of interest. As such, current technologies lack robustness or the ability to discriminate by contaminant type because the limited data collected. With single frequency dielectric measurements, the measured response is a combination of the primary parameter of interest and any other interference parameters. In single frequency measurements, the fundamental assumption is that the response of the primary parameter is orders of magnitude greater than the response of any possible interference parameter, which is then assumed to be insignificant. In many cases, this assumption does not hold true, and the interferences can significantly affect measurement accuracy.
The multi-frequency approach is based on the premise that the primary and inference factors respond differently at different frequencies, allowing the separation of the response from the primary parameter of interest from the interferences. In fact, these sensing systems can often be configured to simultaneously measure multiple parameters. The proposed approach collects much more information about a target fluid, multiple dielectric measurements across a wide spectral range, and thus provides much greater sensing capability.
This innovative approach capitalizes on the capability of electronics that are only coming available now based on developments in technology required for the wireless technology markets. Those technologies can be exploited in this case for the purpose of detecting high contaminant levels in fluids. An example of this rapid development is the substantial increase in A/D conversion speed from the time of an earlier project in 2004 when the maximum conversion speed for 10-bit A/D chips was in the 100 million samples per second (MSPS) range. Presently, 12 bits A/D chips are available with conversion speeds in 400 MSPS, and 8-bit A/D chips in the 2.2 giga-samples per second (GSPS) range.
In addition, the project's approach employs the use of computational intelligence techniques (such as genetic algorithms, support vector machines) for multivariate analysis of the high dimensional dielectric measurements. These advanced techniques have been shown to produce robust calibration and classification models which will be extremely valuable for the sensor's design.
In previous work funded by NFPA, it was shown that water contamination, metal contamination and silicon dust contamination levels can all be sensed using dielectric spectroscopy with promising results. The prediction of water contaminant levels was possible as were the prediction of metal and silicon dust contamination. Dielectric measurements are sensitive to fluid temperature, but when temperature was included as a known parameter, the models showed good potential to predict contaminant levels.
These experiments were performed using a laboratory impedance analyzer to demonstrate proof-of-concept. The next step is to design the sensor circuitry and cavity so that this technology can be practically applied. Thus, the goal of this project is to develop a practical low-cost contaminant sensor for hydraulic fluids based on these previous results. This sensor will measure fluid dielectric properties at multiple frequencies based on previous work to detect water, iron and dust contaminants using a simultaneous multi-frequency dielectric measurement technology similar to that developed by the research team in previous work. The sensor architecture will enable the automatic modulation between different sets of frequencies for detecting different contaminants.
The approach for this sensor design is inherently low cost because no particularly high cost materials are required and no special manufacturing techniques are required. The sensor will require the design of a dielectric sensing cell through which the fluid being measured flows. The proposed sensing technology is leveraging electronic hardware (high speed digital-to-analog and analog-to-digital conversion, embedded signal processors) used in cell phone/wireless device markets, which has a cost advantage due to the large volumes associated with these other markets. The speed and resolution of these electronic devices have increased dramatically in the last few years and are enabling to this sensor development.
In addition, the team is proposing to use multivariate and computational intelligence methods for the development of calibration and classification models that relate high-dimensional dielectric property measurements to contaminant levels. These methods add sensing capability with little additional cost.