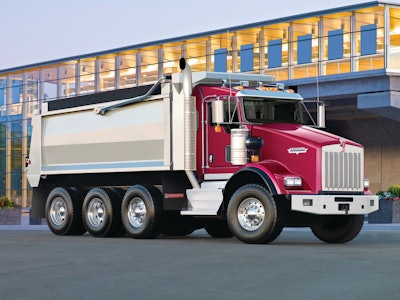
In 2013, on-board diagnostics (OBD) regulation revisions were phased in for heavy-duty on-highway vehicles weighing over 14,000 pounds. All 2013 and above model year engines are required to have an OBD system that monitors engine and emissions control component functionality which guarantees the parts are working properly and not releasing more than the allowable amount of exhaust emissions.
Sensors on the engine and aftertreatment communicate with the engine control unit (ECU) via software algorithms which track if components are functioning correctly. If a problem is detected, the ECU sends a signal to the operator display to illuminate a Malfunction Indicator Light (MIL), telling the operator to get to a repair shop as soon as conveniently possible because there is a problem that could be causing the vehicle to no longer be emissions compliant. The communication protocol prescribed for communications between an ECU and tester is specified as ISO 15765-4 or SAE J1939.
The California Air Resources Board (ARB) implemented OBD regulations as a means of combating air quality issues because it found the traditional emissions regulations were not enough. Components developed for emissions control were malfunctioning or wearing out quickly, causing vehicles to release more emissions as they got older. “One big problem was that ‘in-use’ vehicles were not staying clean (emissions-wise) as they got older and were driven more,” says Mike McCarthy, Chief Technology Officer, Mobile Source Control Division at ARB. “OBD was seen as a way to provide additional incentive to vehicle manufacturers for durability of emission controls.” The regulations also make it easier for technicians to fix detected problems because they provide a standardized method for diagnosing and repairing malfunctioning components.
ARB first implemented OBD regulations for heavy-duty vehicles in 2004. After updating the regulation a few years later to encompass model year engines from 2010 on, the U.S. Environmental Protection Agency (EPA) worked together with ARB to develop a similar nationwide OBD regulation.
While OEMs have been monitoring emissions and aftertreatment activity throughout the progressing Tier emissions regulations, heavy-duty OBD (HD OBD) requires a tightening in monitoring and detection of emissions and failure of emissions control systems, necessitating the use of new sensor technology.
A system built on models
The regulations state that there are 13 major systems and parameters that an OBD system must monitor (see sidebar, pg. xx) to ensure continued emissions compliance. This requires a network of sensors to be used throughout the vehicle on components and systems which could have an adverse affect on emissions compliance. In most cases, the sensors used by the OBD system are ones already included on the vehicle for control of the engine and its emissions controls. In addition to the sensors, software algorithms are used to analyze operating data and identify abnormal behavior that could lead to emissions issues. Keith Doorenbos, Engineering Manager for Vehicle Systems at Kenworth Truck Company, Kirkland, WA, says the software algorithms are the core of the OBD system.
Models and simulations of how a component or system normally operates are built into the software and compared to the actual operating values measured by the sensors to determine if components are functioning properly. “For some components, [models] can be as simple as electrical type checks verifying there are no shorts,” says McCarthy, “while on other components it can be as complex as verifying [the component] is performing at a level that ensures tailpipe emissions are below certain levels.”
Built into the software models are OBD emissions thresholds which tell the OBD system how much of a particular emissions constituent—carbon monoxide, non-methane hydrocarbons, oxides of nitrogen (NOx), etc.—can be released before it’s necessary to activate the MIL. According to Franz Lieder, Director of Calibration in the Diesel and Gasoline Systems division at Robert Bosch LLC (Bosch), Farmington Hills, MI, the OBD regulations state a system must react when emissions reach two times the legislated standard for basic exhaust gas emissions. “You get a bit of a tolerance in the OBD design that you don’t have to have the system flagging when it reaches one and a half times the legislated standard as used for light-duty vehicles,” says Lieder.
Each constituent has its own OBD emissions threshold specified within the regulations. Particulate matter (PM), for example, has a threshold of 0.02 grams per brake horsepower hour. When designing a PM sensor, a company like Bosch would build the sensor’s corresponding model to be at or close to that OBD threshold of 0.02 grams. If the measured amount of PM is more than the modeled amount, an alert from the ECU signals that there is a problem and emissions compliance could be in jeopardy. Cayetano Garcia, Project Manager for the OBD Diesel Systems division at Bosch, notes that as the OBD emissions threshold gets closer to the basic emissions limit, designing an OBD system becomes more challenging. The emissions levels engineers have to work with are becoming smaller and margins for design are nearing zero.
OBD models must also take into account the varying operating conditions of a vehicle. “One major challenge is calibrating the logic so that it can quickly and consistently identify the deviations that signal emission issues while not triggering alerts for unusual or extreme deviations that are part of the normal variation range of engine and vehicle operation,” says Doorenbos.
Because conditions can change at any moment, and thus affect how the OBD system determines proper functionality, all potential scenarios must be accounted for and built into the system. When a vehicle is traveling at higher loads and speeds, more than the average amount of heat is generated in the diesel oxidation catalyst (DOC) which could cause the DOC’s temperature sensor to alert the OBD system that there is a problem. Having a model built into the temperature sensor which accounts for these high load and speed conditions, however, tells the sensor the target temperature threshold for OBD and emissions compliance needs to be set higher and that until the temperature surpasses this new threshold, there is no problem. “At higher loads and higher speeds you’ll have a different target than at lower loads and lower speeds,” says Bosch’s Lieder. “That’s where the model becomes critical.”
Ensuring proper functionality
With so many components, systems and models to keep track of, developing OBD systems and components can be challenging. “There’s a significant chunk of functionality inside [an ECU]; usually in excess of 50% of the code is taken up by diagnostics,” says Bernie Porter, Senior Technical Calibration Specialist at MAHLE Powertrain (MAHLE), Novi, MI. “If you look at the level of complexity in a modern vehicle powertrain, there’s more computing power than there is in the space shuttle.”
An OEM’s close collaboration with engine, aftertreatment and other component suppliers enables a wealth of information to be collected and used to more easily develop fully optimized, reliable OBD systems. According to Kevin Baney, Chief Engineer at Kenworth, he and his colleagues have become one team with their engine suppliers, working together in the early stages of development defining a plan by determining what the requirements are and how they will be integrated. “It’s a lot of early, up-front definition and close communication throughout the process,” says Baney.
Garcia says that for an engine manufacturer, OBD can be especially challenging due to the variety of applications where the engine can be utilized. “Because the engine is built into very different types of vehicles you cannot make something special that only works on one truck and not on the other,” says Garcia. “You have to find solutions that are robust and can be built into different types of vehicles.” In addition, companies such as Bosch have to design accurate and reliable sensors, as well as highly durable ones, to last hundreds of thousands of miles, often without service intervals.
Working together with an engineering services provider such as MAHLE can help with the development process, as well. MAHLE will calibrate and analyze OBD systems developed by OEMs and engine manufacturers to ensure the manufacturers are delivering on their promise of meeting the regulations. Porter says a large part of what MAHLE does when collaborating with manufacturers is detecting sensitivities within the system which would prevent it from working properly. “The calibration part of it involves engineers effectively setting the control parameters based upon the conditions the engine is operating in,” says Porter. This however, can be challenging because no two drivers operate a vehicle in the same manner. “What we term the system ‘sensitivities’ are not so easy to determine because that basically involves identifying every possible way an end user could drive the vehicle.”
One of the sensitivities manufacturers have to watch out for is MIL fatigue, which can be caused by setting the fault threshold too low. Porter says the fault threshold—the point at which the OBD system says it’s necessary to turn on the MIL—will often be set 50% lower than the legal level to ensure compliance. The light may also be programmed to illuminate as soon as a fault is detected, even though the regulations allow for a two-trip logic, which is a fault being detected twice, once each on two successive trips before the MIL needs to be turned on. This approach to OBD system development can cause the MIL to be illuminated too frequently, and often when not necessary, causing operators to become annoyed with the light and ignore it.
According to Garcia, one of the basic principles of designing an OBD system is ensuring it can separate a good part from a failed part. “You never want false failures in your systems,” adds Lieder. If the system is continually flagging a good component as a bad one, warranty issues can arise. Conversely, if the system continues to detect a bad component as a good one, the vehicle will no longer be considered emissions compliant and could receive heavy fines from ARB and EPA.
User interaction
Properly educating drivers and technicians on how to use an OBD system has also been a concern for OEMs. Kenworth’s Doorenbos says that while there have been some heavy-duty OBD engines in use since 2010, they were in the minority and most customers have not had much exposure to them. One change brought about by the 2013 regulation is the difference in setting and clearing fault codes. “It is important for drivers and technicians to be clear in communicating when the MIL is illuminated and when the Check Engine Light is illuminated,” says Doorenbos. “They have a similar appearance but different meanings and uses.”
At the beginning of 2012, Daimler Trucks North America (DTNA), Portland, OR, made its OBD system Virtual Technician (VT) available on Detroit brand engines (visit oemoffhighway.com/10848408 to learn more about VT). Brad Williamson, Manager, Engine and Component Marketing for DTNA, says VT monitors engine and emissions systems, and provides the operator with directions on how to take corrective action when the MIL is illuminated. “Virtual Technician will help a driver quickly determine the severity of a MIL and make a determination when it is most appropriate to service the issue,” he says.
Like many OEMs, Kenworth is continually working to make the OBD user interface more operator friendly. The company has developed aftertreatment notifications which pop up simple text messages on the display that clarify for the driver what actions can be taken to resolve diesel particulate filter (DPF) soot loading or low urea levels before those conditions become severe enough to cause problems. “The whole goal is, if the MIL comes on, how do you get it resolved, reset and the customer back on the road as quickly as possible,” says Baney.
Future regulations and product development
McCarthy says ARB routinely updates the OBD regulations every two to three years in an effort to keep up with emissions control and technology advancements. As such, new requirements will be put into place in 2016 and 2019. “OBD is an evolving regulation,” adds Doorenbos. “There are major changes in the sensitivity threshold for identifying emissions issues that are presently scheduled for 2019.” He adds that other smaller changes will also be made as necessary such as the introduction of urea quality sensing and a possible data link speed change.
Updates to misfire detection are also on the horizon, which Lieder says Bosch is preparing for through the development of components such as combustion pressure sensors. Current OBD regulations require misfire detection when a vehicle is at idle. The updated regulation will also require detection at high speed and high load, or possibly over the entire operating range, which means new sensors may be needed to accurately identify misfire issues. According to Lieder, additional OBD updates will also include additional exhaust gas monitoring. “One catalytic converter prepares exhaust gas for a second catalytic converter, and the regulation specifies monitoring of proper exhaust gas preparation,” he explains.
Each time ARB makes updates to the OBD regulations, it works with manufacturers to get a better understanding of how their products work and what technology changes or advancements the manufacturers are capable of making to meet the proposed updates. “We have to get into detailed discussions with manufacturers regarding how their systems work and have very detailed understandings of control systems, emission controls and what happens when things malfunction,” says McCarthy. As ARB moves on with the rulemaking process, it again meets with manufacturers as well as associations and individual suppliers to further evaluate technical feasibility, costs and any other concerns. “Staff routinely meets with manufacturers to review their future systems and plans,” McCarthy adds, “and provide feedback on whether they are on track to meet our requirements.”
For the time being, the HD OBD regulations are restricted to on-highway vehicles. McCarthy says at one time the EPA said it would like to pursue similar regulations for the off-highway industry, but as of yet no regulations have been put forth. “There are several things that generally have to happen before an OBD approach could be considered,” he explains. “Those include the source having ‘enough’ emission controls to warrant monitoring and enough electronics or computer control to make such a system viable to incorporate.” Until then, off-road equipment manufacturers should simply be aware of the OBD regulations, since more often than not heavy-duty on-road equipment technologies eventually find their way onto more rugged applications.