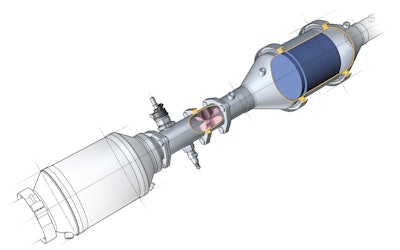
Aftertreatment devices and systems have often been afterthoughts—a figurative bandage—to the increasingly demanding emissions regulations placed onto engine system designers and equipment manufacturers. Integrated solutions like selective catalytic reduction (SCR) and exhaust gas recirculation (EGR) provide emissions reduction internal to the engine system, while diesel particular filters (DPFs) are external filtration devices to capture particulate matter (PM). These solutions are used in a multitude of combinations dependent on the vehicle application and duty cycle.
With Tier 4 Final emissions regulations set to be implemented as of January 1, 2014—which requires off-road engines with output over 75 hp in the U.S. and 130 kW in the European Union to reduce NOx (oxides of nitrogen) and PM emissions by 99% compared to pre-legislation levels—the aftertreatment technologies have been chosen, implemented and announced by engine manufacturers. While there is a standard list of options commonly referenced by OEMs, each manufacturer has a unique variation of how it will accomplish emissions reduction while still improving upon overall vehicle performance and productivity.
Experience in the design and development of aftertreatment solutions enables Tenneco Inc. (company information, 10056163), Lake Forest, IL, to have a unique focus on proactive emissions reduction technologies designed for the anticipated demand in the global commercial vehicle industry.
Tim Jackson, Tenneco’s Chief Technology Officer and Executive Vice President has been with the company since 1999. “The DPF started on light vehicles around 2001, and Tenneco was one of the first to be able to offer high volume DPF production,” says Jackson. “We have been able to take that technology and scale it up to light commercial vehicles, then into non-road commercial vehicles, and ultimately into the large engine space.”
While aftertreatment systems are in a sense able to be scaled-up for larger applications (or vice versa scaled down for smaller applications) the scale is not a direct translation. Take for example the factor of durability, defined as the “useful life” of the system. In a light vehicle space, a system is being designed for a useful life of 8-10 years and 150,000 miles. When it’s moved into the commercial vehicle space, it’s being designed for durability requirements from 400,000 to 1 million miles depending on the customer; in the non-road space, now a system is being designed for a useful life of 8,000 hours up to 20,000 hours.
“In all of those cases, it’s not a simple linear progression on what needs to be done to get higher levels of durability and reliability,” says Jackson. Other variables that are not scalable are engine back pressure, and vibration and G-loads based on the weight and mounting of the emissions control units.
The company has developed and researched dozens of technologies beyond the DPF, priding itself on its forward thinking product development style to create the next-generation emission control solution. See Tenneco’s forward-looking solutions map on pg. XX.
Scalable SCR
The company has been supplying SCR systems since 2004 in Europe. “Around 2007, we made a strategic decision to supply a turn-key SCR system rather than just supply the SCR catalysts and mixing,” Jackson says. At that point, Tenneco acquired the capability for urea injection, dosing electronics and software.
Tenneco’s turn-key SCR system, the XNOx SCR system, is a modular, scalable technology that is being used in engines as small as 4.4 liters and as large as 18 liters or more. The system is comprised of an adaptable, model-based controller, a return flow style injector, a fluid delivery system including a pump and filter and pressure sensor, and ancillary components like fluid tanks and more sensors. The controller drives the system and can predict engine-out NOx and account for ammonia storage and degradation of the catalyst over time. Based on engine and external operating conditions, injection rates are dynamically controlled to accurate amounts of urea to achieve the desired emission levels while minimizing backpressure and costs.
The basic architecture of the system is the same as it is scaled across engine sizes, accommodating for a change in the required dosing rates. Tenneco’s patented injector can be adapted for use with urea (diesel exhaust fluid, DEF) as well as fuel, which is often required within aftertreatment systems to manage DPF soot loads or other NOx catalysts. The design produces significantly smaller droplets than other injectors available in the market, meaning less effort is needed to evaporate and distribute across teh catalyst cross-section. Its wide spray angle improves the urea distribution throughout the exhuast gas, avoiding concentrated impingement that creates localized cooling, promoting the likelihood of undesired deposits forming within the system.
The diameter and cross section of the decomposition tubes have to adjust, as well, but Tenneco works hand-in-hand with engine manufacturers to ensure proper calibration for each application. There is a significant amount of simultaneous engineering that is needed between the engine and emissions systems. “You can’t calibrate the aftertreatment in the absence of engine calibration,” saysJackson. “The optimum point of engine-out emissions with the specific fuel consumption and power output needs to be determined,” he continues. “Turn-key doesn’t mean the system is developed in a vacuum.”
“While we are able to customize the solution, we are at the same time able to have a high amount of system standardization,”Jacksonsays. Two basic injector designs—high flow and low flow—can cover an engine range from 1.0 liter up to around a megawatt (1,300 hp) of power, “and the dosing maps, the calibration and the on-board diagnostic (OBD) software is always application specific,” he says.
Solid SCR
An alternative to liquid urea/AdBlue SCR systems is Tenneco’s Solid SCR. Jackson clarifies that Tenneco does not believe that its Solid SCR will become a replacement for all urea-based systems, but rather is for customers seeking an alternative solution. “This isn’t necessarily a disruptive technology, but I think it has a compelling value proposition in the right application. For new or cold [temperature] applications, or remote locations without the ease of access to urea’s developed distribution infrastructure, Solid SCR may make sense. If you think about a situation where a vehicle is being used in a cold mountain climate, how do you get liquid SCR to them besides in a heated cab to keep the urea from freezing while in route to the job site? We’re seeing a lot of interest inChinacurrently because of its lack of DEF infrastructure.”
The Solid SCR system can generate ammonia (NH3) for the SCR system at much lower temperatures than with urea. Urea’s challenge is that it has to undergo thermolysis and hydrolysis reactions to result in ammonia. “With our Solid SCR system, you dose directly with gaseous ammonia that’s released from a solid form using heat.” What that means pragmatically is that after an overnight cold soak—and certainly in the non-road segment there are several examples of equipment that sits outside overnight—the urea freezes. So, after an engine starts it can take anywhere from 10 to 20 minutes before the urea is liquefied and the exhaust temperatures are high enough to dose. With the Solid SCR system, the ammonia can be generated in as little as 90 seconds after an engine start, even after an overnight cold soak. “For test cycles, such as the World Harmonized Transient Cycle (WHTC1) that has a lot of cold temperature performance with significant weighting on the cold temperature portions, the Solid SCR system can outperform a liquid SCR system [with up to a] 40% improvement in NOx reduction,” Jackson says.
Another benefit to Tenneco’s Solid SCR is the reduction in storage needs. Ammonia carried in liquid urea form is approximately 67 to 68% water, whereas the storage density of the ammonia in the solid form eliminates that. “We can store about twice as much more ammonia in its solid form, which makes the packaging much simpler. In a non-road environment, some of these package spaces are pretty tight. There is not a lot of room on the vehicle when you consider ground clearance, visibility and space under the hood to package an SCR tank. We can get an equal amount of ammonia in about half the space with the Solid SCR,” saysJackson.
Due to the reduced tank size and better performance at cold temperatures, and the fact that the Solid SCR eliminates the corrosion issues of water-based urea, the system costs less than other SCR systems. “We all understand the importance of cost reduction in the business for the purchaser. They don’t appreciate the increase in sticker price that comes with emissions compliance. Our customers are looking for solutions to improve the value to the end customer. We as an industry have to have an intense focus on cost reduction, and that cannot come at the expense of sacrificing emissions performance or durability,” Jackson says.
Hydrocarbon (HC) Lean NOx Catalyst
Another alternative to urea-based SCR systems was created by Tenneco along with its partners, GE and Umicore. The Hydrocarbon Lean NOx Catalyst (HC-LNC) uses either diesel fuel or ethanol as the dosing reductant. “We invented that technology based on a very futuristic view of the world, that eventually there would be demand for a non-urea NOx abatement technology. Now, we’ve found excitement around that technology in South America. That’s an example where we’ve been innovative and have led the industry by owning the science around new technologies.”
Brazil has one of the most developed ethanol economies in the world; ethanol fuel can be purchased at virtually any filling station. Brazilian ethanol is not produced from corn like in the U.S., but rather sugar cane, a local and more affordable source. “We have commercial vehicle customers who have taken the step to evaluate the system within their on-road development fleet which should lead to a production commitment,” Jackson states.
Years ago, the Brazilian government announced a mandate for the transition from hand harvesting to mechanized harvesting of sugar cane. The primary purpose of the transition was to eliminate the need to burn sugarcane fields before workers cut the sugarcane by hand. In order for the sugarcane to be harvested by hand, the dry leaves must be burned off ahead of time. The burning process results in increased amounts of pollution and PM in the air. They also release huge amounts of greenhouse gasses (GHG) which the government is trying to limit.
“Sugar cane harvesters will be a great development,” Jackson says, “because it will increase capacity and eventually reduce the cost of the ethanol-based product. We’re measuring the ethanol consumption on these trucks compared to the DEF consumption that is on the counterparts, and we’re seeing a variable operating cost at about half with the ethanol of what the DEF expense is. A liter of ethanol actually goes further. Our dosing rate is lower with ethanol than it is with DEF, and the ethanol is less expensive per liter, and when you multiply those two together, you get a variable operating cost for the reductant of about half of what the legacy cost is.”
Leveraging the leftovers
Exhaust heat is one of the biggest wastes of usable energy on any vehicle. Tenneco is exploring various thermal management solutions to recuperate exhaust heat and convert it into accessible on-board power. There are three basic ways that heat energy can be reintroduced to the vehicle as usable energy: The first, and simplest, is heat-to-heat conversion. In a heat-to-heat energy conversion, a common air-to-water heat exchanger can be built into the existing exhaust system and used for auxiliary vehicle functions such as warming the cabin more quickly in cold conditions. Another option would be to pump the heat into the driveline to warm lubricants and hydraulic fluids during cold starts to reach optimal operating conditions faster. “On a cold start, all of the lubricants and hydraulic fluids are cold and viscous. There is a large amount of parasitic loss in the driveline due to this; so, one of the easiest things we can do to improve vehicle fuel economy is to help get that vehicle up to an optimal operating temperature more quickly after a cold start. That’s the easiest and most cost effective of the heat recovery applications,” Jackson confirms.
The heat conversion that’s probably the most exotic, according to Jackson, is heat-to-electricity. It’s a technology that is well-founded in physics to use semiconductor elements with the Seebeck2 effect. Jackson explains further, “You use a temperature gradient across the semiconductor to generate electricity, and then instead of getting electricity from a belt- or gear-driven alternator mounted on the engine which extracts a fairly significant parasitic loss load on the engine, you can get the electricity ‘for free’ using waste exhaust heat.” He notes that the current problem with that technology is cost. “The industry needs to see at least a 10:1 reduction in the current cost in order for that to be a commercially viable technology, but Tenneco is working on it in collaboration with customers, universities and specialty material companies. I’m confident that before the end of this decade we’ll see it become a cost-effective technology for vehicles, but the durability will have to be proven, as well.”
The third exhaust heat energy recuperation technology that is still a mystery is waste heat to mechanical energy. “Here you use a reverse Rankine cycle3 machine that actually takes the exhaust heat and runs it through a miniature turbine or engine to produce shaft power,” explains Jackson. “Then you can put that power back into the engine in a couple of different ways. You can either use it to turbo-compound the engine where you use a supercharger at lower RPMs and the turbo at higher RPMs, or you can use it to add horsepower back into machine. That one is in the very early experimental phases, and it is unclear if and acceptable cost-benefit ratio can be acheived, but we are working on it as are many others nonetheless.”
What else does the future hold?
As OEMs continue to investigate ways to enhance the existing Tier 4 Final engine package, the conversation frequently echoes a desire to re-simplify the engine system and fully integrate the aftertreatment capabilities into the internal function of the engine without additional components that add weight and space constraints.
While some engine manufacturers want to use engine-based technology to reduce the amount of aftertreatment, Jackson points out two realistic conditions that may stop this from happening are the reduction in GHG and improvements in fuel economy. “We all understand that there is a basic trade-off between NOx and fuel economy. What I believe is going to happen is that the engine-based technologies are going to be largely directed toward reducing GHG and improving fuel economy.” Tenneco already has companies asking for higher efficiency aftertreatment devices. While current SCR systems are operating at 90 to 95% efficiency for removing NOx, there is an interest in 98% efficiency.
FOOTNOTES
1 The WHTC test is a transient engine dynamometer schedule defined by the global technical regulation (GTR) No. 4 developed by the UN ECE GRPE group. The GTR is covering a world-wide harmonized heavy-duty certification (WHDC) procedure for engine exhaust emissions. The regulation is based on the world-wide pattern of real heavy commercial vehicle use.
2 The Seebeck effect, according to the Encyclopedia Britannica (yes, it still exists), is defined as the production of an electromotive force (emf) and consequently an electric current in a loop of material consisting of at least two dissimilar conductors when two junctions are maintained at different temperatures. The conductors are commonly metals, though they need not even be solids. The Seebeck effect is used to measure temperature with great sensitivity and accuracy and to generate electric power for special applications.
3 According to the Encyclopedia Britannica, a Rankine cycle in heat engines is an ideal cyclical sequence of changes of pressure and temperature of a fluid, such as water, used in an engine, such as a steam engine. It is used as a thermodynamic standard for rating the performance of steam power plants. In the Rankine cycle, the working substance of the engine undergoes four successive changes: heating at constant pressure, converting the liquid to vapor; reversible adiabatic expansion, performing work (as by driving a turbine); cooling at constant pressure, condensing the vapor to liquid; and reversible adiabatic compression, pumping the liquid back to the boiler.