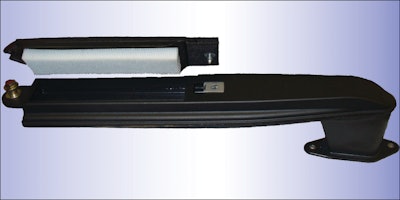
When debris, dust and various other particulates enter a machine cab, both operators and electronic equipment are put at risk. Operators exposed to particulates are susceptible to a range of health risks. Meanwhile, electronic equipment can short circuit and malfunction, minimizing its usefulness and lifespan.
As OEMs and their customers have become more aware of the damaging effects of improper cab air filtration—due in part to growing research—they have put more of an emphasis on ensuring their equipment includes effective cab filtration and pressurization systems.
New standards such as EN 15695 in Europe and ANSI/ASABE S613 in North America have also played a part in emphasizing proper cab air filtration. EN 15695 specifies four categories representing various protection levels ranging from no protection against hazardous substances (Category 1) to protection against dust, aerosol and vapor. Category 2 requires a filtration system to reduce the quantity of dust that enters a cab while Category 3 states both dust and aerosols must be reduced. Category 4 adds requirements for gas adsorption to the reduction of dust and aerosols. “To reach the different requirements, cabin air filters of Category 3 and 4 require a combination of different filter media in one element,” says Kevin Babb, Business Development Manager at MANN+HUMMEL USA (company information, 10055755), Portage, MI.
The new European standard also requires certification of the filters from an independent test laboratory to guarantee standard compliance and operator safety. “Standard development will help to ensure high quality and technology levels that will enhance operator protection,” says Babb. “The primary markets today driving cabin filtration are Europe, North America and Japan.” The American Society of Agricultural and Biological Engineers (ASABE, association information, 10239641) standard requires certification of the filter manufacturing process and proper labeling of the filters, enabling consumers to be informed about the efficiency performance of the filter.
According to Jeff Moredock, Vice President of Sales and Marketing at Sy-Klone International (company information, 10056670), Jacksonville, FL, the most damaging particulate is that which is not visible to the human eye. “The issue is the dust you can’t see,” he says. “Our focus is on removing respirable particulate in the 0.3 to 10 micron range.” As a point of reference, the diameter of a human hair is 150 microns. See sidebar below.
Traditionally, cab air filtration systems have consisted of a fan bringing outside air into the cab and a low efficiency filter located between the fan and the cab to prevent particulate from entering. However, Moredock says these filters are not effective at removing particulate less than 10 microns.
Spinning the dirt out
To prevent even the most microscopic of particulate from entering a cab, Sy-Klone has developed the RESPA-CF Vortex HyperFLOW Cab Air Quality system which creates a tornado (centrifugal forces) inside of a tube to remove particulate. A fan motor brings air into the tube in a circular manner and accelerates the air speed to collect the particulate. “The faster you spin that tornado, the more capable [it] is of pulling particulate out of the air to a smaller and smaller size,” says Moredock. “We can pull particulate out of the air down to about 5 microns, at a very high level; [it’s about] 93% of the 5 micron material that’s being pulled out of the air.”
As particulate is collected by the tornado, it is ejected out the backside of the tube away from the vehicle cab. While the spinning air is able to capture the majority of the particulate that tries to enter a cab, there is still material that is too small to be affected by the circulating air. “Five micron and smaller particulate—down into that lower end of the resperable range, 0.3 to 5 microns—that particulate is so small, gravity has no impact on it,” explains Moredock. “It floats around in the air indefinitely.”
Because the center of a tornado has no air movement, Sy-Klone determined that was the best place to put a filter for capturing the microscopic particulate. The particulate rests on the filter until water enters the system, causing it to collect and clump together much like sand does when it gets wet. The particulate becomes a very fine sheet of debris which is now capable of being ejected out of the system via the tornado.
The compact system, capable of operating in some of the harshest and most intense environments in the world, typically extends filter replacement to 1,000 hours whereas previous systems may have required filters to be changed daily.
Providing positive cab pressurization is also critical to keeping particulate out of the operator’s working environment. By continuously putting fresh air into the cab, more air can be pushed in than is leaking out to create positive pressure that prevents particulate from entering the cab.
Moredock says a traditional pressurizer/blower system—which uses a fan similar to a fan/motor in an air conditioning system—is used to provide the continuous airstream for cab pressurization. The pressurizer/blower draws air through a filter and into the cab or HVAC system. This type of system can clog the filter quickly and prevent air from entering the cab, which can lead to a loss in positive pressure.
Enginaire’s Cabaire cab pressurization unit addresses this issue by using a precleaner to remove particulate from the air which will be used to pressurize the cab. “It has a self-contained air pump where we draw air through an air precleaner then through a filter and then through a pump. And we put positive pressure inside the [cab],” says Bill Decker, President of Enginaire Clean Air Systems (company information, 10055364), Janesville, WI.
By spinning the air as it enters the precleaner, centrifugal force is able to separate the heavy particulate from the airstream and eject it from the system back outside the vehicle. Now only the smaller particulate remains for the Cabaire filter to capture, allowing only clean air to enter and pressurize the cab. “It keeps the filter working for a longer period of time and keeps the whole system cleaner for a longer period of time,” Decker explains.
Going HEPA
With the increasing concern over cab air quality, the use of HEPA (high-efficiency particulate air) filters in air filtration systems has grown in popularity within the off-highway equipment industry. “Everyone wants to get into HEPA filtration,” says Russell Kelly, President of APC Filtration (company information, 11017384), Cheektowaga, NY.
To be classified as HEPA, the U.S. Dept. of Energy (DOE) says a filter must meet certain standards; in particular, the filter must have the ability to remove a minimum of 99.97% of particles measuring 0.3 microns from the first pass of air through the filter.
For many years glass fiber HEPA media has been the industry standard in HEPA filter construction. Glass fiber filter media is capable of operating at higher temperatures, however compared to synthetic fibers, glass fibers are expensive and heavier in weight, which can be an important factor in some applications. Within recent years fiber producers have developed lightweight synthetic fibers that perform at HEPA-level efficiencies. Kelly notes that in comparison to glass fiber media, synthetic materials provide a lower pressure drop across the entire filter. “As a result, longer service life can be achieved compared to glass fiber filters of the same size. In certain cases we reduce filter size for applications where cab space is limited,” he says.
Kelly says traditional filter media cannot simply be replaced with HEPA filter media. This would increase pressure drop across the filter and decrease airflow through the motor or blower, ultimately reducing airflow circulation throughout the cabin. “Converting from traditional cellulose media to glass fiber HEPA media, requires modifications to the cabin air handling system and/or the filter housing,” he says. He continues that cabin air HVAC systems often use low pressure static fans which do not work well with HEPA filters because glass fiber filter media is more restrictive than traditional cellulose. In order to provide higher efficiency and proper airflow throughout the cabin, either new motors or blowers have to be used or modifications to the filter housing have to be made in order to accommodate a larger filter area. “We’re doing a lot of work with OEMs of off-road HVAC equipment designing cabin air handling systems to accommodate glass fiber and/or synthetic HEPA filters,” says Kelly.
APC works with both HVAC manufacturer, and off-road equipment OEMs to determine the application and its required filtration level and equipment. This is important to determine raw material selection and proper filter media for each application. While working with Bobcat Company (company information, 10815102), West Fargo, ND, and its HVAC supplier, APC determined using a fiber glass PTFE laminate HEPA filter media was the best option for the application due to the dust load the filter would be subject to, the size of the filter that was needed, as well as the cabin geometry. “We couldn’t use synthetic HEPA media because it’s thicker than glass media, almost fluffy, and you cannot get the necessary amount of filter media surface area required. In comparison, glass fiber media did not provide the dust release required for this heavy and dusty work application. The best alternative was a PTFE membrane laminated to a glass fiber substrate media. This provided the best dust release and filtration efficiency of 99.99% at 0.3 micron,” says Kelly.
Choosing the right filtration media
Various environmental factors have an effect on the type of filter media that is used in a system. Kelly says because synthetic media is electrostatically charged it works best in dry environments where relative humidity is around 72 F. “Static charge starts dissipating in high humidity conditions,” he explains, decreasing the lifespan of the filter. Synthetic media will also not survive in wet environments. “We have to be very conscious of where equipment is operating in the world,” Kelly says. “We have samples [of dust] from all over the world—we know the micron size and the makeup of the dust—and we design the filter to handle that type of dust. In some cases, you have to modify or replace any existing HVAC equipment to handle those environments.”
Besides the shift towards HEPA filtration, the industry has made other advances in filtration media design, much of which has been moving away from the paper-like media that has been used over the last 30 years. The use of nanofiber technology, for example, has been growing in many types of filtration systems including those for operator cabs. Sy-Klone’s Moredock says filtration media has historically been made in a similar manner to a bird building a nest—pieces of fiber are placed on top of one another until an indiscriminate mat has been created. Nanofiber technology improves upon that, he says, by creating a more uniform surface.
According to Kelly, nanofiber filtration media consists of applying an extremely fine diameter web of polypropylene fiber onto a substrate media, providing a fine web-like appearance to increase filter efficiency. “It’s not HEPA by any means but it’s a very high filtration and it still allows for decent airflow,” he says. See sidebar, pg. xx to learn more about nanofiber technology.
One disadvantage with nanofiber filtration media is that it cannot be washed, Kelly points out. Once the filter is no longer able to capture particulate, it must be thrown out and replaced. He says APC, on the other hand, offers washable synthetic and PTFE membrane filtration media that can be cleaned and reused multiple times.
“Increasing demands for operator comfort have resulted in the tendency to use combination filters (with activated carbon) rather than pure particle filters,” adds Babb of MANN+HUMMEL. Carbon filters are most often used in applications where there are a lot of chemicals or smells present that would inhibit operator productivity, such as landfills or farm fields where pesticides are being sprayed. The activated carbon (charcoal) provides a larger surface area for capturing the odors and chemicals.
Ensuring operator health will continue to be a key design factor for OEMs and their component suppliers as customers and government regulations alike pursue the importance of clean air. “The big thing right now is there is a lot of attention being brought to this whole issue, principally because the research has given a clear understanding of what the problem is, and also a consensus on how to address the problem,” concludes Moredock.