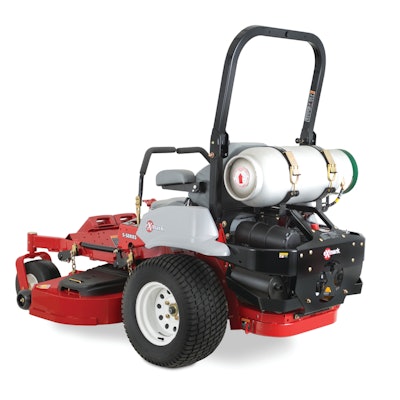
The goal of any manufacturer is to produce a piece of equipment that passes along productivity and profitability to its customers. “A major trend in our industry is finding ways to advance the amount of productivity per gallon of fuel,” says John Swanson, Product Manager, Exmark Mfg. Co., Inc. (company information, 11078696), Beatrice, NE. “For a landscape contractor, that is a really high priority considering how directly fuel costs impact their profitability.” The solutions that find their way onto the next generation of mowing equipment accomplish reduced fuel consumption and increased productivity together, not one or the other.
EFI and propane improve performance
As a frequent new technology development and launch partner with engine manufacturers, Exmark is able to get in on the front end of implementation and gain exclusivity and market share gains prior to a technology’s public launch. The company recently worked with Kohler Engines (company information, 10055682), Kohler, WI, to develop a closed-loop electronic fuel injection (EFI) propane engine system, the PCV740 Kohler EFI. “Our industry was a little resistant to convert to fuel injectors,” says Swanson, “but now that the technology is proven and more reliable, we’ve seen an industry transition to acceptance. I can see carbureted engine systems eventually being phased out completely,” he predicts.
“We worked with Kohler and the Propane Education and Research Council (PERC, association information, 10286979) to develop the PCV740 found exclusively on Exmark’s Lazer Z Propane zero-turn riding mower for the 2013 model year. In 2014, the engine will become more widely available to other manufacturers,” explains Swanson.
Kohler EFI engines integrate an oxygen sensor that analyzes the air/fuel mixture in the unit’s exhaust. If the oxygen level strays from the ideal mixture, the sensor triggers adjustments to the amount of fuel injected into the system. Kohler’s EFI technology then “closes the loop” between the air/fuel intake and the exhaust output to provide a constant stream of critical feedback, which helps deliver optimal fuel efficiency and a variety of other benefits, including easy starting, improved power and increased life span.
Back in October of 2012, Kohler announced its first propane-powered EFI engines, the Command PRO EFI Propane engines, offered in 23 and 27 hp models (product information, 10820616). *See Kohler’s full engine line, including its EFI-equipped models, on OEM Off-Highway’s online Engine Spec Guide. Visit www.OEMOffHighway.com/SpecGuide to view these engines and hundreds more.*
“With the closed-loop propane system, Exmark is seeing the Lazer Z Propane mower burn 40 to 50% less fuel, and the performance exceeds what we had on the old system,” Swanson says. “That’s helping to lower the amount of greenhouse gas (GHG) emissions dramatically as well.” Customers in the lawn care industry are now coming to understand that with a higher up-front investment in a mower with advanced EFI technology, they can get a long-term payback with the fuel efficiency gains.
Using propane fuel is not without trade-offs for the manufacturer. There is a cost and weight penalty due to the amount of fuel needing to be hauled on-board the mower (or other vehicle) as well as the increased storage needs for the gaseous fuel. The propane container alone can weigh as much as a full gasoline fuel tank. To combat the added weight issues, Exmark has worked to lower the overall package weight by going to a one-tank propane system as opposed to the two-tank solutions typically found in the industry. Instead of two 33.5-pound tanks mounted off the side, Exmark uses one 43.5-pound tank that is centrally mounted over the engine, reducing the overall weight and enhancing mower handling due to the balanced tank location.
“If there is ever a way we can reduce weight without impacting durability, it’s a win-win. But we won’t sacrifice the durability that our landscape contractors are relying on 10 hours a day, six days a week,” Swanson says.
On-board intelligence amplifies fuel savings
Beyond the electronics and sensors included in the fuel injection system, Exmark implemented last year its RED on-board intelligence platform which is capable of improving fuel savings even further. Instead of a spring-based mechanical governor system, the RED platform features an electronic governor on the engine that was originally developed for generator and welder machines. The electronic governor offered by Exmark, E-Gov, helps to maintain a constant yet slightly reduced engine rpm which reduces fuel consumption while maintaining blade tip speed for improved and consistent cut quality.
“Because the E-Gov system is more responsive than a spring and wind-based governor system, the engine doesn’t have the rpm droop you can get if you’re cutting a patch of heavy, wet grass,” says Swanson. “Engine droop is significant on the mechanical governor system we’ve used in the past in the industry. With the electronic governor, it doesn’t mean you have zero droop, but it’s close to zero. As opposed to a binary system that looks for feedback after a condition has changed, the electronic version senses condition changes and can supply feedback immediately allowing the engine to adjust accordingly.”
The RED technology is essentially an engine management system that interacts with the electronic governor technology and allows Exmark to define the performance modes of the engine. A contractor can work in Max, Efficient or Low modes depending on the conditions. “I would say approximately 80% of the time the contractor should be running in Efficient mode which allows the engine to run at its peak performance while maximizing fuel efficiency. If they encounter overgrown or heavy cutting conditions, for example, the operator can switch to Max mode,” says Swanson.
In the long term, Exmark can see a fully-automated system allowing the machine to run in its most efficient mode dependent on conditions without any operator engagement, but transitioning an operator from full mechanical control to zero control is too significant of a mindset and operational shift for Exmark. As an interim solution, the RED platform system features a physical rocker switch with three mode selection. “We’re phasing it in to ensure our customers end up with the performance we want and they need,” Swanson states.
The RED system also monitors the clutch, and by matching the engine speed to the optimum clutch engagement and disengagement points is able to elongate the component life. The on-board electronics also track engine temperature and oil pressure. Should a critical threshold—as established by Kohler and Exmark during engine system co-development—be surpassed during operation, the system places the machine in “safe transport” mode which both notifies the operator of the problem with visual warning LEDs and audible alerts, as well as allows more attentive servicing before there is a larger problem.
“We are looking to expand the use of the RED on-board intelligent platform in the future with additional models,” confirms Swanson.
Deck configuration evolution
Similar to a larger piece of agricultural harvesting equipment, in the lawn care industry mowers see power gain opportunities with streamlined processing of material. “While the widely accepted configuration of side discharge offers easier bagging and mulching capabilities due to the grass material being handled three times from left chamber to center chamber to right chamber discharge, it also raises safety concerns and performs poorly in certain conditions,” claims Swanson. “Plus, if the material is being handled three times under the deck before being expelled, it’s also drawing on the engine three times as much as the single-time handled rear-discharge deck we developed at Exmark.”
The deck was launched with one of Exmark’s 2013 model year mowers, and after a year in the market “we’ve learned some things that will end up transitioning a lot more customers to rear discharge than we anticipated,” Swanson says. “For 2014 we will be expanding the use of the rear-discharge deck to additional models in the Lazer Z line,” announces Swanson, which demonstrates a huge investment and company confidence in the value of rear-discharge decks for the industry.
Even without the added value of reduced power draw on the engine, rear-discharge decks are gaining momentum in the industry as bagging becomes less common due to the affiliated labor costs and environmental issues associated with the practice. As a side benefit to the end customer, by leaving the cut grass clippings instead of bagging them, when the grass clippings decompose, they return nutrients to the soil making the lawn healthier.
Ergonomic enhancements
Exmark employs an entire team to focus specifically on operator performance through reduced operator fatigue for increased productivity and safety. Its ECS (Enhanced Control System) was developed for stand-up mowers with ergonomics in mind. The grips position an operator’s hands in a naturally comfortable location, as well as a protected location when maneuvering by objects such as fences or trees. “As a general rule, we try to keep technology simple because our customers can’t afford a week of training for each new employee. They need to be productive within the first day, so technology was developed to be intuitive,” says Swanson.
In addition to mower hand controls, Exmark’s ergonomic seat technology, the EVC (elastomeric vibration control) stretch fabric is patented by its seat supplier. The elastic band replaces the springs that were traditionally under the seat for added comfort and cushion.
The mechanical seat suspension in the past had a lot of friction so it wasn’t as quick to respond up and down. “We got rid of the friction by going to a ball bearing system which floats up and down with much more ease. All of that seat technology sits on top of our patented isolators,” Swanson says. The patent is written on how much freedom of movement an operator will have up and down, but also fore and aft. “The seat has a certain amount of give in every direction as opposed to just the up and down motion. Isolating the operator in a 360 degree manner makes a significant difference because impacts aren’t being taken in a straight up and down manner, so why should the suspension?”
In the end, every technology Exmark contemplates developing and implementing must somehow increase the productivity and/or profitability of the people using the product. “If it doesn’t accomplish one of those two core goals somehow—whether it is increased comfort helping the operator stay productive longer, or the ability to produce the same amount of work with less fuel consumed thus lowering operating costs—we aren’t going to focus on it,” concludes Swanson.