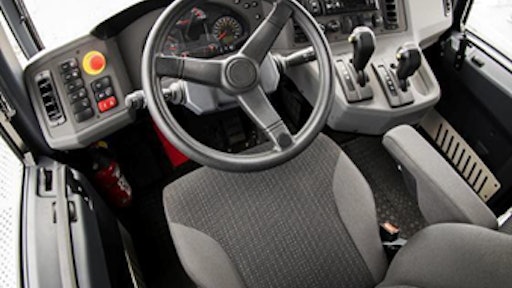
Over the last decade or more, digital switches have become the first choice for electrical systems in passenger vehicles. More recently, the off-highway vehicle sector of the transportation market has accelerated its migration to digital switch technology.
As the automotive industry has transitioned from hardware to software-defined vehicles, the amount of electronics and software per vehicle has soared. This same trend is taking hold in the construction and agricultural vehicles sector. The electromechanical switch remains integral to the design of off-highway vehicles. However, the added functionality of digital switching and the reduction in wiring weight and complexity make it a choice worth considering in any vehicle design.
Is it finally time to switch? Unfortunately, going digital is a lot more complicated than using an electromechanical switch. Each digital switch must be programmed to interact with the controller on the vehicle. LIN and CAN buses have different considerations. Configuration requires close collaboration between OEM design engineers and the supplier’s hardware and software teams. On top of that, there are more considerations for selecting the switches themselves, including the environment, functions, configurations, and communications.
This article walks through the considerations and gives tips on the process of migrating to digital switches.
Part Number Reduction
The cost of an electromechanical switch is decidedly lower than that of multiplex switching. Nevertheless, digital switching products can positively impact business operations. A heavy-duty vehicle manufacturer currently has about 300 different electromechanical component variants within its cab. The manufacturer’s goal is to replace this setup with one of three digital switching systems as selected by its customers, with actuators configured at the end. If all goes as planned, the manufacturer will see a sharp reduction in the number of components it purchases and stocks.
Ease of Manufacturing
Multiplexing results in significantly fewer components to assemble, wire, and connect. According to one transit bus manufacturer, prior to moving to multiplexed communication, its electrical system accounted for as much as one-half of engineering time and 15% of vehicle assembly cost. By the way, fewer components to assemble and connect means fewer chances for error and fewer potential points of failure.
Weight Reduction
In a CAN bus system, there is no need for an array of hard-wired components and circuit boards as the functionality they enabled is now software-driven. The dash weight of a heavy-duty truck can often be reduced by half when eliminating large, heavy wiring harnesses. This improves fuel efficiency and strengthens a manufacturer’s selling proposition.
Reliability
In a digital switching system, there are fewer physical contacts transferring electricity. In some cases, digital switching is more responsive upon load activation because solenoids operate more slowly than a signal sent via software.
Built-in Diagnostics
As a software-driven product, digital switching modules come equipped with built-in diagnostics. This enables the quick and easy identification and repair of myriad issues that can help lower the total cost of vehicle ownership.
Customization
The features of the passenger car dashboard will steadily find their way into the cabs of commercial vehicles. As with many 21st-century business trends, this trend is driven by economics and capabilities afforded by innovative technology.
With multiplexing, manufacturers now have the ability to customize the actions of a switch. This results in new features that can enhance vehicle comfort, productivity, and safety. For example, headlights that automatically switch on upon wiper activation, switches that activate only if the driver is in the seat, automatic dimming of interior lighting that minimizes windshield glare, and door lock activation above 5 mph (8 kph).
Digital switching offers varying degrees of customization depending on the customer’s needs and budget. For example, the OEM can specify a standard digital switch at one price point and upsell a customized switch. Littelfuse
Architecture
A digital switching system has two sides: the physical switches in the cab and the non-physical interfaces that communicate with controllers via CAN bus or LIN bus and provide complex logic and intelligence. For different applications, these devices may be using different languages.
Digital switches typically are available as modules containing 4 to 12 buttons. They might feature a rotary encoder or a joystick. The switches are designed to work with certain communication protocols, so that may affect the options at the time of selection.
In selecting switches, a consideration is how many switches are in the cabin and what variety of functions. Will the functions be static, or will they change? Also, what is the vehicle quantity? Some switches are better suited for lower or higher volumes.
A controller module acts as the gateway between LIN and CAN based communications. The switch sends a signal to the controller, and the controller communicates with other controllers inside the vehicle. These controllers cover the powertrain, safety, comfort, infotainment, and telematics.
Selecting a digital switch includes selecting the communication protocol and baud rates plus the source address. The vendor will supply an interface specification that guides how the switch is sending and receiving messages; this is how the switch can be recognized by and integrated with the controller.
Typically, the vendor creates an interactable software environment for the user to configure and program the logic to their needs. Digital switching requires a lot of collaboration between the software engineers for the controller and the software engineers for the HMI, as well as the engineering team for the final design.
Flexible Design
Digital switching enables manufacturers to easily integrate new options into their vehicles. This is a particular benefit for many smaller to mid-size companies whose key competitive strength is maximum design flexibility. Take, for example, switch placement. With some digital switches, the intelligence is in the switch itself, so switch placement can be anywhere the customer wants. If, for instance, the customer wants the door lock switch on the door instead of the center console, no problem. The switch can be removed, relocated, and reprogrammed. Indeed, by making design customizable, scalable, and expandable, multiplexing gives the manufacturer and its customers the ultimate in design flexibility.
Human/Machine Interface
One reason why digital switches appeal to vehicle designers is because they are stylish. A modern appearance can help differentiate a vehicle and enhance its perceived value. The key to design success is to ensure that the new style in no way compromises the operator’s interaction with the vehicle.
A few years ago, product designers for some metro bus manufacturers sought a more pleasing aesthetic by specifying membrane keypads. However, these keypads presented a fundamentally different experience than what bus operators were used to. The new switches provided no positive haptic feedback. What’s more, because the drivers had to take their eyes off the road to confirm they were pressing the right spot on the keypad, the switches made for unsafe driving. Understandably, there were so many complaints from drivers that the engineers had to redesign the interface.
Think through how the vehicle operator will interact with digital switches compared to what they are used to. Will retraining be required? Have all safety-related issues been fully considered? Simply put, while style is important, substance is more important.
Operating Environment
The cabins of off-highway vehicles are often exposed to rough handling, bad weather, shock and vibration, and dusty environments. It is imperative that the digital switches are robust and meet the required IP rating for the application. Some switches are designed with enclosed backs that add protection if the seal around the switch fails.
In Summary
Is it time to leave electromechanical switches in the dust? While electromechanical switches still play a major role in commercial vehicle electrical design, digital switches offer advantages that can make them the more suitable choice for many applications. Multiplexing is the future of commercial vehicle electrical design that’s fast becoming the present. For now, at least, it’s fair to say that a point has been reached when off-highway vehicle transportation engineers should carefully weigh the pros and cons of both switch types when designing in a switching system.
Callum Eastwood is senior associate product manager at Littelfuse.