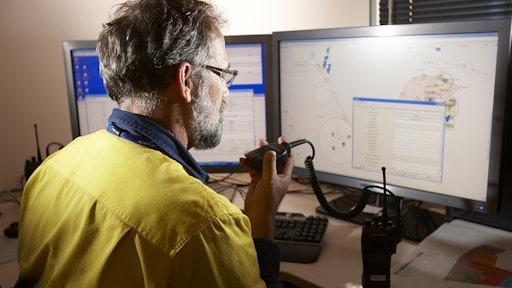
In the depressed mining industry, efficiency is critical. Over the course of the past three years, many mine sites have struggled to stay open while others have closed completely. The strained market has led many mines to look into fleet management systems (FMS) and high precision (HP) technologies to improve their utilization and effectiveness in order to become more competitive and, in some cases, just survive. The return on investment by using FMS and HP systems is very high, some systems pay for themselves in a matter of months due to the savings achieved from improved operations, reduced waste and better vehicle utilization.
As data collection and connected networks rapidly become commonplace in the world around us, it is only natural to gravitate away from generic platform products and shift toward customized solutions for the application at hand. To leverage functionality but also system performance optimization, the tools used to collect, manage and analyze data must be tailored to each application’s unique set of challenges and expectations.
The mining industry has a number of aspects that differentiate its data needs from other off-road industries such as construction and agriculture. According to Michael Roff, High Precision Product Manager for Hexagon Mining, one of the most significant differentiations is the inter-dependency between equipment that exists to efficiently complete different mining operations. The most common example of this is a haulage fleet of trucks and shovels that depend on real-time information from each other to ensure the trucks are loaded to, but not over, capacity. The haulage destination for each truck can be determined based on the material grade that the shovel loaded into the truck.
Typically, other industries don’t have as many examples of close vehicle relationship dependencies, but that is changing. Agriculture, for example, implements collaborative vehicle operations between harvesters working with autonomous grain trucks.
Another facet of the mining industry that sets it apart from construction is the sheer size of the mining site, which can be orders of magnitude larger than a construction site. The vast space a mine can cover creates a larger dependency on the reliable capture, storage and transfer of data between different groups within the mine. Such data includes site planning and designs, operational statistics such as material movement and volume dig rates, machine health data for vehicle maintenance, and real time safety systems.
“Due to the large capital costs and operational costs of a mine, there is a significant return for each percentage of improvement that can be achieved. Data is generally at the center of any such improvement, enabling the initial analysis of operation, evaluation of improvement and ongoing monitoring of performance,” says Roff. A mine can cost anywhere between $100 million to $1 billion to establish and can last upwards of 50 operational years. “It’s this size and scale that demands effective operations driven by innovative data solutions to deliver long term returns on the initial capital outlay and against ongoing operational costs,” he says.
Data Solutions
The effective operation of a mine is accomplished through the effective use of its resources, both vehicle and mineral. Well-rounded data solutions feature data gathering, management and analytics capabilities. Hexagon Mining features data solutions for planning, safety and operations on the mine site.
Download a free brochure to learn more about Hexagon Mining’s suite of data solutions.
The aforementioned fleet management (FMS) and high precision (HP) systems contribute to a mine’s overall operation. FM systems allow the complete fleet of mining equipment to be coordinated from a central location, delivering real time positional and production information, allowing for real-time decisions to be made for the optimized coordination of the mine fleet for maximum production and minimal downtime.
More advanced FM systems feature optimization programs that collate data from every system on the mine site and can dispatch trucks and shovels automatically to improve site productivity, and conversely can park ineffective trucks to minimize operational waste.
HP systems extend the capabilities of FM systems “by generating real-time position data for equipment such as drill, shovels and dozers, and presenting this against production designs [such as] drill patterns, grade blocks or planned surfaces,” Roff explains. “The ability to digitally project a vehicle’s position against a virtual design in real-time enables operators to make decisions on the fly to maximize their efficiency and minimize re-work.
“As access to more sophisticated spatial systems becomes standard in mines, the need for more integrated and intelligent data management systems will be essential. Without such systems, the benefit that can be derived from these new found capabilities will be lost due to the ever shifting nature of the physical mine itself.
Roff suggests that if the FM and HP systems are not yet considered a necessity for mine site operation optimization, the time is not far off before it’s mandatory. “With the likes of Rio Tinto and BHP already exploring autonomous fleet operations, the stage is set where the future is in computerized scheduling and deployment of mining fleets in order to survive the lows and reap higher profits during the highs.”
Hexagon Mining is currently working on the next generation of mining solutions which includes sophisticated data processing and management to provide real-time terrain mapping. This innovation will spawn a new level of awareness on the mine enabling mine managers to make more informed decisions and to more closely align and adapt the short term mining plan based on production actuals. “I predict that real-time terrain will become a central focus for many groups within the mine who will leverage it for planning meetings, progress reports, surface design, material management, stockpile management, hazard detection and many more innovations that haven’t been thought of yet,” concludes Roff.