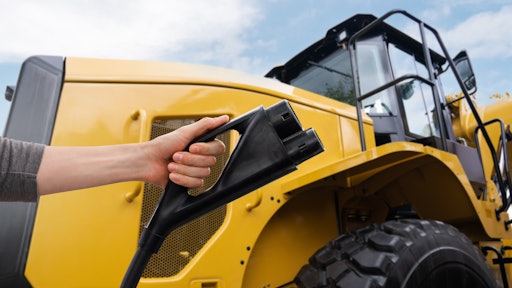
Go to any trade show or open any news publication and you’re likely to hear how companies of all sizes and types are working to optimize product designs in response to stricter zero-emissions policies.
What exactly does optimized mean in the world of mobile system design? Everyone seems to have a slightly different definition but, ultimately, it’s about achieving the ideal balance between performance, cost and efficiency.
Achieving that balance is no easy task, especially in light of the ongoing high cost of batteries and lengthy charging times. That means the entire system’s design needs to be rethought in order to achieve the ideal marriage of hydraulics and electrification. For those who have been in the industry for some time, it means having to relearn some things, and not just on the control side.
In this article, we’ll discuss various efficiency models, different system approaches, and we’ll provide tips, at a high level, on how to optimize system design for hydraulics.
Shifting Away From Diesel Engines
While different parts of the mobile market are responding differently, most of the changes we’re seeing today in systems design are driven by zero-emissions policies and mandates. OEMs and operators alike are looking for the best options that help them shift away from diesel engines to electrically driven systems. At the foundation of this newly envisioned system are the inverter, which converts battery energy to power the system, and the motor. The motor drives the propulsion of the vehicle and/or hydraulics and/or accessories since these newer systems no longer have pulleys or belts to drive things.
Understanding The Key Challenges
Everyone is striving for efficiency, and there are lots of approaches for getting there. Yet not all of these approaches are truly efficient. And some approaches that are efficient have proven to result in negative consequences, such as excessive noise, or safety or reliability problems. Designing an efficient system that is quiet, safe and reliable comes from proper system design and an ability to effectively analyze and use data.
Figure 1: Electrification: Balancing cost vs. performanceParker HannifinElectric systems are like data machines, producing all kinds of data that can be transmitted and able to inform ways to optimize the operation of the vehicle or equipment, perform diagnostics, pinpoint the greatest areas of efficiency, and create a digital strategy for productivity.
Since the hydraulic components are often the least efficient part of the three (inverter, motor, pump/valve), designing an efficient system should start with a focus on the hydraulic system architecture. The challenge, however, is that so much is still unknown. Think about the traditional baseline diesel engine design. It is a traditional system long in the making and optimized over many years. Based on data gathered over all this time, we know exactly what diesel systems cost, TCO, maintenance requirements, etc. What we know about electric machines is that they are more expensive, primarily as the result of the high cost of the battery. That’s why efficiency matters so much.
Efficiency is key in electric machines. With a traditional system, you could simply add a bigger cooler for heat rejection. But this is an expensive option with electric systems and heat is a result of inefficiency which means you’re wasting useful energy from the battery. So start by looking at what contributes to the overall system’s power density, including the motor, the pump characteristics and how it operates at high pressure, the inverter and its capabilities, noise, condition monitoring and thermal management.
Good system design and innovation are critical to reach specific cost targets because the power density of diesel versus a battery is 20:1. A lot of volume is required to get a kilowatt of stored energy, whereas it doesn’t take a lot of diesel to run an engine for a specific time.
Batteries also have charging limits and take time to recharge, so you have to figure out a solution that works around these obstacles. That means changing the way we think about hydraulic systems. Despite advances in technologies, batteries today are still expensive and many can’t get through a full shift without needing to be recharged. Battery management is critical because every 1% of efficiency gain in a system is $200 savings in battery costs — a huge factor in calculating TCO.
With a traditional hydraulic system that includes a diesel engine with a PTO and gear pump, the hydraulic valves consume excessive amounts of energy to control the hydraulic power. That’s a lot of wasted power to do a relatively small amount of work, which translates into lots of lost efficiency. Just getting hydraulic power out of the engine/PTO can take a lot of power due to mechanical losses. This didn’t matter before, because diesel fuel is cheaper than battery power and takes much less space to store so most fleets weren’t as concerned about how much fuel was necessary to get the job done.
Identifying Possible Solutions, Starting With the Power Architecture
In the early days of electrification, a lot of companies approached the problem the same way. They simply dropped out the diesel engine and replaced it with an electrical motor and then replaced the fuel tank with a battery pack. The solution seemed simple enough and initially appeared to work because everything else downstream remained the same, which meant there were no new maintenance requirements. But there was a big problem. Even though each component could be very efficient, once in a system, they didn’t efficiently work together.
From these early attempts we learned that we needed to take a more holistic view that considered the total system design.
Centralized System
Early designs included a centralized system with a main pump to control all the functions. With this design with a typical 30 kWh battery the load difference and speed difference of the different cylinders created lots of starting loss, with valve loss representing more than half of total system loss. With this approach you only get 10% of the available energy. So, while this type of system design allows you to keep your identical hydraulic system architecture and controls, you wind up with very low system efficiency, as well as cooling problems because of excessive heat that’s generated by the valve loss.
Decentralized System
A decentralized system has proved, over time, to be a better option. With this design, you don’t just drop in a new engine. Rather, you split the electro-hydraulic actuator by work function. The pump/motor pair with inverter serve as a specific power source dedicated to one function control. This eliminates concerns of overproduction of flow or pressure and allows you to do power-on. This results in a significant efficiency gain because the hydraulic pumps are driven by multiple electrical motors in an EHP and EHA setup. You can also achieve partial (but not full) power on demand with the EHA with electronic LS control, which means that valve throttling loss is reduced, but still significant. But at least you are able to reduce battery size and cost.
Fully Distributed System
A superior option for some OEMs is a fully distributed system which provides electro-hydraulic actuation with minimal valve controls. With this approach, a dedicated motor pump pair drives a cylinder which reduces valve loss substantially, leaving the biggest loss through the pump. The result is 70% duty cycle efficiency, which is more than twice what can be achieved using the decentralized approach. Advantages include maximized system efficiency, as well as full power on-demand with no throttling or idling loss. However, its complex system structure requires smaller, faster and power-dense pumps with advanced controls. The more complex structure reduces the power needs of the system so that power is double or triple what you originally had. However, it’s important to ensure coordinated motion and control.
Figure 2: Total system efficiency comparison of various system architecturesParker Hannifin
This distributed architecture costs more initially because of the complex structure, but ROI is realized from the efficiency savings. To realize these savings, however, you must start by matching the pump and the motor. They can’t be randomly chosen and simply thrown together.
Existing hydraulics are designed for optimal efficiency at lower speeds (typically less than 3,000 rpm). However, the typical electric motor is most efficiency at very high speeds (typically more than 7,000 rpm). This results in a mismatch in which the pump’s peak efficiency is at a different range than the motor’s.
One solution is to design a smaller pump that operates at high rotational speeds and is also more efficient at those higher rpms. If the pump can cover the higher range efficiently, the result is higher motor and pump power density. The challenge is existing hydraulic pumps are designed to match a diesel engine and there is no need for hydraulic pumps to go above 3000 rpm in a diesel system. That means adapting the pump to optimize the electric motor range, effectively marrying the motor and pump together. Gearing can help to match the pump with motor, but this approach comes with additional inefficiency and cost. High-speed pumps are already being successfully used in other industries, such as aerospace, where the weight of the unit is a critical consideration. To date, though, their use in mobile applications has been limited.Figure 3: Matching of hydraulic pumps and electric MotorsParker Hannifin
Factoring In the Noise Problem
None of the discussions around efficiency would be complete without pointing out how noise factors into the design equation. Noise was never a consideration before because the traditional diesel engine masked any hydraulic noise. But now with the diesel engine phasing out, the noise of the hydraulic pump is noticeable. The problem is not with the motor, as electric motors emit little noise. Rather, the problem is with the pumps which, currently, are not sound optimized for an electrical motor drive.
How important is noise? It depends on the market and application. If you’re working in areas where noise mitigation is a priority, including residential areas, you need to design your system with the goal of limiting the noise of the pumps.
A good starting point is understanding what affects noise levels. This includes pump technology, pump speed, operation conditions and pump pressure. High-efficiency pumps tend to be noisier. There are quieter pumps available, but those aren’t as efficient. Fortunately, new pump technologies are continuously being developed to effectively balance noise with efficiency.
In the meantime, there are four ways that you can solve a noise problem using existing pumps:
- Pump emitter noise reduction (ripple reduction)
- System emitted noise reduction, which is related to component design and control
- Isolation/dampening, using some material to shield and absorb the noise)
- Encapsulation (wrap around)
Or, there are ways to control the motor to reduce the pump noise. Motor suppliers are evaluating potential motor topologies which are optimized to produce peak torque at lower speeds, which would be optimized to run hydraulic pumps.
Conclusion
As this article has highlighted, with every system design there is a tradeoff. Unfortunately, there are no silver bullets available today. So, you need to work with what’s best for your machine approach. Think of the total system and not just individual components. Also look at the total work life of the piece of equipment.
When it comes to maximizing efficiency, it’s important to match components and optimize the entire system for maximum power density. Don’t assume you can overlook noise, but also recognize that noise is largely a result of the pump, so focus your mitigation efforts there. Condition monitoring, which was not discussed in detail in this article, can also lower TCO by providing actionable data. When you’re making investments of this size, it’s critical to use data to optimize the entire system operation.
_________________________________________________
Rich Nagel is a program manager for electrification at Parker Hannifin. Howard Zhang is chief engineer for motor technology at Parker Hannifin.