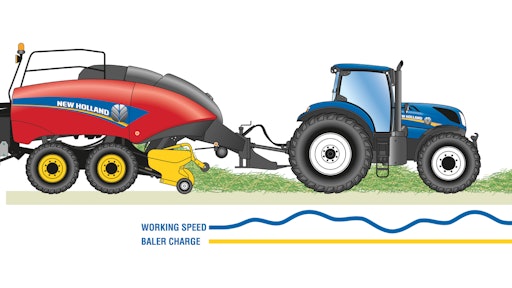
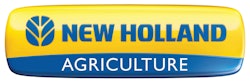
As 2015 marks New Holland’s 120th anniversary, the milestone has allowed New Holland to reflect on its leadership and success in hay and forage equipment. For model year 2016, select New Holland hay and forage equipment has been enhanced to meet the ever-changing marketplace demands for upgraded electronic features that can help achieve higher efficiencies.
“New Holland customers use our hay and forage equipment because they know New Holland knows hay,” says Mark Hooper, Senior Director of Marketing for New Holland North America. “Nobody bales more hay each day than New Holland, and we look forward to using new technology to continue our reputation for raising the bar in hay and forage equipment.”
Technology enhancements for model year 2016 include in-cab density control on Roll-Belt Series Round Balers, ISOBUS III AEF certification, heavy-duty pickup components and the new IntelliCruise Feed Rate Control system on the BigBaler Series Large Square Balers, PLM Connect Telematics system on the Speedrower Self-Propelled Windrower, and new ISOBUS-compliant electronic controls on the MegaCutter Mounted Disc Mower-Conditioners.
Roll-Belt Series Round Balers
New Holland announces in-cab density control and variable core adjustments in model year 2016, Roll-Belt Series Round Balers. This technology allows operators to change the density pressure setting using the monitor inside the tractor cab for easier operator interface and convenience. Additionally, independent density values can be achieved in the bale core and outer bale. Customers that desire to have a lower density core for easy feeding and movement, or to allow the bale to “breathe” in high-moisture conditions can achieve two separate density values for the core and outer bale. If customers choose to store outside hay longer than normal due to plentiful supply then choose a higher outer bale density to increase water shedding ability.
The operator can also determine the size of the core for additional customization. Density pressure and core diameter settings are adjusted in the Bale Command II Plus User Settings Menu or if the baler is equipped with ISOBUS capability, these settings can be adjusted using the IntelliView touchscreen.
In-cab density and variable core adjustment is available as a standard feature on Roll-Belt 450 SuperFeed , CropCutter and all Roll-Belt 460 models. It is also available as an optional feature on all additional Roll-Belt 450 Dry Hay and Silage Special models, Roll-Belt 560 Dry Hay WPU, Bale-Slice and Specialty Crop models with Deluxe Wrap or ISOBUS with or without monitor.
BigBaler Series Large Square Balers
New BigBaler 340 Standard and BigBaler 340 Rotor Cutter models offer IntelliCruise Feed Rate Control System with two modes of operation: Charge Control (Rotor Cutter Only) or Slice Control (Standard or Rotor Cutter). IntelliCruise is operated with the new, ISOBUS Class III compatible T7 AutoCommand tractor as an optional feature that helps operators achieve a constant feed rate or flake thickness while baling. Since most fields have varying crop yields, resulting in inconsistent swaths, it makes it difficult to maintain a constant feed rate. The IntelliCruise system allows the baler to run at optimal performance by controlling the speed of the tractor.
The IntelliCruise system when operated in Charge Control automatically matches the tractor’s forward speed to crop load at the BigBaler. A charge sensor on the stuffer constantly monitors the bale charges, or slices, delivered to the bale chamber. The system measures the demand placed on the baler (from crop yield) and adjusts tractor forward speed for optimal crop feeding. In areas with lighter crop, forward speed automatically increases so operators consistently work at the capacity specified.
When operated in Slice Control, tractor speed is adapted based on slice thickness to strive to obtain a user defined amount of slices.
Using the IntelliCruise system results in dramatically reduced fatigue because fewer operator interventions are needed, up to 9% higher capacity and productivity over an inexperienced or fatigued operator, and lower fuel consumption for lower production costs.
Another new feature on the BigBaler Series is the Crop RFV System. Using the Crop RFV system allows operators to measure the Relative Feed Value of their crop as it is being baled. The system measures the weight of the bale and the moisture content to calculate the leaf-to-stem ratio of the alfalfa crop. The leaf content relates directly to Acid Detergent Value (ADF) and Neutral Detergent Value (NDF). The lower the ADF and NDF, the higher the RFV.
When used with the CropID system, each bale will be tagged to show the RFV, Total Digestible Nutrients (TDN), and Moisture Content (MC%) making it easy for operators to see how the value measured in the field compares to lab analysis of actual core samples. Crop RFV can also be paired with a dye marker kit as an economical option to mark bales with a user set RFV range for easy identification and sorting.
The BigBaler Series Large Square Balers have been enhanced with heavy-duty pickup components which have been improved by incorporating features of the current self-propelled forage harvester windrow pickup head. This means that the BigBaler now has larger diameter tine bars, stronger tine bearings, and new heavy-duty flanges for the bearings. The new tine assembly mirrors the SP forage harvester windrow pickup heads design with a heavier tine retention casting and new speedy tine fixation, no nut required.
Speedrower Self-Propelled Windrower
PLM Connect Telematics is now available as a factory supplied option for model year 2016 Speedrowers with the IntelliView IV display. The new Speedrowers are the first New Holland machines to feature PLM Connect as a factory-supplied option, making it easier for producers to take advantage of the latest PLM technology.
Precision Land Management technologies have evolved and today more tools are available to help managers ensure their operations work more efficiently than ever before. PLM Connect provides today’s farm managers with the remote monitoring of machine performance, physical location, and many other parameters in addition to providing the possibility to remotely share guidance lines between equipped machines. Currently an Essentials Package and Professional Package service levels provide an introductory level service as well as a comprehensive full feature service package. Model year 2016 PLM technology also became even more reliable and user-friendly by taking advantage of secure, cloud-based data transfer over two of the nation’s largest cellular networks.
The Speedrower Self-Propelled Windrower’s CommandGrip Multi-Function Handle will also see an upgrade during the model year to enhancing ergonomics in haying applications. The button sensitivity has been improved to require less force to activate header control functions, the header control and reel buttons have been rotated slightly for better access relative to hand placement, and the stalk of the handle has been shortened to provide easier transition with the adjacent finger rail.
MegaCutter Mounted Disc Mower-Conditioners
ISOBUS technology also comes to the MegaCutter Mounted Disc Mower-Conditioners allowing for a totally new user interface that enhances ergonomics.
A new joystick control box is now available for the MegaCutter 530, which has several options with varying ISOBUS compatibility. The first option is a control box for ISOBUS equipped tractors, which connects through a tractor's ISOBUS plug on equipped tractors and control all functions on the rear unit through a new joystick controller. With this controller functions can also be monitored and controlled by compatible tractors virtual terminal when equipped. The second option eliminates the joystick controller and relays information on the tractors ISOBUS connection. The MegaCuter 530 is controlled through a virtual terminal, or the use of a tractor’s programmable multi-function hanlde buttons when equipped. The last option is provides a joystick style controller to directly control the MegaCutter 530 where a tractor is non -ISOBUS equipped tractors. This includes the new ergonomic joystick control box and a wire harness to connect directly to the rear mower.
Model year 2016 MegaCutter 530 models also have a closed center hydraulic system to make efficient use of tractor hydraulics.