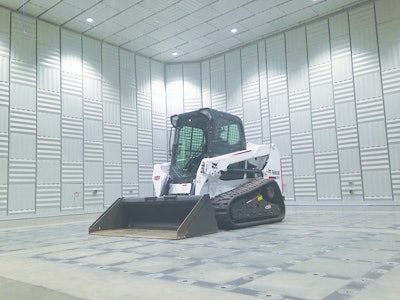
Bismarck, ND is home to Bobcat Company’s Acceleration Center which is a flagship research, design and engineering facility. Opened just over a year ago, the 190,000 sq. ft. complex is a magnet for young engineering talent and cutting edge technology. And that’s exactly why Bobcat contracted Eckel Noise Control Technologies to design and install a state-of-the-art test chamber there.
“Bobcat is world-renowned for its construction, landscaping and agriculture equipment. Their Acceleration Center is an exemplary facility for innovation and testing,” says Eckel Vice President Jeff Morse. “Being chosen to contribute to such a place is a true honor and we’re proud that our chamber is helping to support Bobcat’s superb design and engineering.”
The Eckel SuperSoft Test Chamber provides a customized solution for evaluating noise and vibration emitted by Bobcat machines and components. It features high-performance perforated metal sound-absorbing panels which are installed using a track and batten system. The V-ridged panel facings help to maximize noise reduction. Designed to match or exceed the sound absorption characteristics of an existing chamber at Bobcat’s Gwinner, ND facility, the Eckel chamber blocks the transmission of noise from testing in other parts of the Acceleration Center to provide a totally insulated and quiet environment.
The chamber is big enough to hold some of Bobcat’s larger equipment, such as skid steer loaders, compact track loaders and compact excavators. The room’s ventilation and exhaust systems allow for operating the machines under full load, while the floor grid supports the bolting down of fixtures for component tests on engines, hydraulic systems and cooling systems. Installed hydronic lines provide external cooling.
Internally, the chamber measures 50 ft. long by 51 ft. wide and 25 ft. high. It features a 12-foot by 14-foot vehicle door; a 90-inch by 41-inch personnel door; and a 48-inch by 42-inch viewing window of laminated safety plate glass. The walls, ceiling and doors are covered with Eckel’s SuperSoft perforated metal panels, each measuring 30 in. by 30 in. The chamber has a 200-Hertz cutoff frequency (meaning it is 99% sound energy-absorptive at frequencies of 200 Hertz or higher). It meets the ISO 3745 standard for transmissibility and has a base ambient sound level of 22 dBA, exceeding Bobcat’s target of 30 dBA.
Construction and installation began on September 24, 2014 and finished on December 1, 2014. Bobcat started setup for its first test in the chamber that very afternoon. The test involved a spherical beamforming project in collaboration with Sound Answers and Brüel & Kjær. Spherical beamforming creates a 360-degree sound field map in confined environments like vehicle cabins and measures sound pressure, sound intensity, particle velocity and sound quality.
“We were very pleased with Eckel’s attention to detail and their firm commitment to our installation schedule,” says Pat Stahl, Product Development Engineer at Bobcat. “This new chamber has allowed us to significantly expand our testing capabilities.”