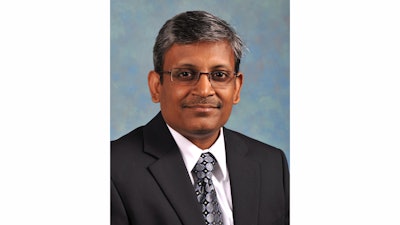
Now that Tier 4 Final is underway, many companies’ engineering resources have been freed up to refocus on developing new products instead of refining existing products to meet regulatory expectations. Have you seen this refocusing? What does this mean for future equipment designs and advanced system development?
Electronics and mechatronics are leading product innovation in both vehicle and implement control. In addition to powertrain electrification, there is also interest in converting traditional hydraulic controls to electric drives. Advanced driver assistance systems (ADAS) leading to full autonomous driving is one of the most active product development areas. This involves a lot of technology infusion into the vehicle, including a variety of sensors, electronic control units (ECUs), and software to enable this technology.
Where is the heavy-duty vehicle industry lagging?
Computing and electronics technology are rapidly changing and opening new possibilities in product innovation. Additionally, there is significant collaboration among OEMs to understand the non-competitive technology components that could benefit from the economies of scale leading to standards such as AUTOSAR. On the other hand, with increasing software content there is a renewed focus on the software development process. This highly dynamic technological environment provides the heavy-duty vehicle industry an opportunity to benefit from technical advancement to create a competitive edge, while reducing cost by leveraging standards. The heavy-duty vehicle industry has an opportunity to benefit from:
- Vehicle-to-Infrastructure (V2I) capabilities with changing on-road infrastructure
- Leverage electronics/mechatronics to create a competitive edge
- Economies of scale by leveraging cross-industry standardization (such as AUTOSAR)
What current ideas and new technologies have the most potential for future gain?
Advanced driver assistance systems leading to a future of automated driving are already having an impact in the passenger vehicle market. These technologies hold a big promise towards reduction of on-road fatalities. I believe these technologies will migrate to the heavy-duty vehicle segment much sooner than we expect.
What new challenges have arisen that effect the way you design or manufacture your product? How you do business? How you go to market?
Mechatronics and embedded software are a very innovation-rich segment of product development. Increasing electronic content in the vehicle is leading to fast growing system complexity. To manage this system complexity and large amounts of data, we are continuously innovating on our side to provide tools to manage data, while increasing product development efficiency. We have developed several products to support customers’ model-based design (MBD) tool chains. The adoption rate of our new products is accelerating. However, our customers continuously face challenges with the availability of trained resources to perform these complex tasks. This is a significant problem facing the industry. dSPACE, in addition to supporting various STEM activities, also supports ECOCAR, a national collegiate competition that helps students learn technology development processes with industry standard tools.
As a provider of design and simulation software, what are some of the biggest challenges dSPACE sees engineers facing now, and in the future?
What design tools does dSPACE foresee will be necessary to help engineers overcome these challenges?
It is commonly understood that engineers face three main challenges:
- System complexity is growing fast, and we need technology to effectively manage the deluge of data that results from product development. Data management is a huge issue for the MBD community. The existing PLM/ALM tools designed to manage end results of the development process are insufficient to handle the work products generated in the development phase and to streamline the development process by connecting all of the artifacts from requirements to the end results throughout the development tool chain. dSPACE introduced SYNECT, a data management solution for MBD, to provide a solution to this problem.
- Embedded software testing technology, like hardware-in-the-loop (HIL), will continue to remain the most efficient way to test. However, the availability of such a test infrastructure is limited. Therefore, there is a need to provide alternate methods to perform some of the software testing and validation tasks. Early validation of embedded software and leveraging a testing infrastructure for maximum efficiency is quite critical. To address this problem, dSPACE introduced VEOS®, a virtual validation platform that can run simulations in the PC environment, while providing connectivity to all of the engineering tools for experimentation and testing.
- Portability and reusability of simulation models. Engineers commonly use a variety of simulation models to suit their intent, resulting in various formats of models in various tools for the same component under development. The industry is addressing this key issue of portability of simulation models across the simulation environments and platforms, and also the reusability of this key engineering work product, through the definition of a new standard called Functional Mock-Up Interface (FMI). dSPACE is committed to supporting this standard. In addition to participating on the steering committee, we are already supporting this standard throughout our tool chain.
How does dSPACE see the use of design and simulation software progressing within the industry over the coming years?
With an increase in system complexity, we foresee the use of design and simulation software to continue to grow over the coming years. It is clear that without well-defined work processes, together with tools to enable efficiency, we will lose the promise of reduced cost of development through the use of model-based design. dSPACE is committed to supporting our customers to develop efficient product development processes through products such as our virtual validation platform, VEOS, our data management platform, SYNECT, and the support of standards such as AUTOSAR, ISO 26262 and FMI, as well as by providing guidance through reference workflows for setting up development processes that will comply with required standards.
Engineers are continuously striving to produce high-quality products, while being more efficient in the development process. They want to ensure that all of the defined requirements for the product are completely met and there are no gaps in development. To this effect, dSPACE understands that the embedded software testing process will need a variety of tools that will span from validating work-product quality to testing executable implementations. The dSPACE tool chain provides a complete backbone for the model-based development process.
Additionally, several of our strategic partners provide tools that help improve quality and extend capabilities for the efficient testing of embedded software. Many dSPACE and partner tools are qualified by suitable authorities for use in safety critical product development and provide a seamless tool chain environment. We are supporting this tool chain throughout the development process.