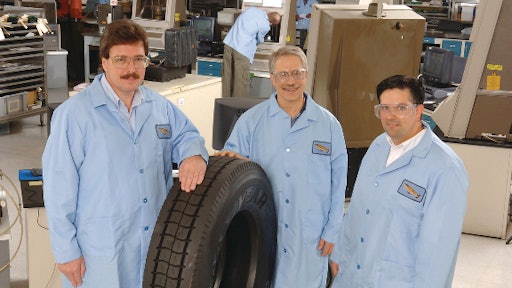
On the surface, a commercial tire looks like a simple piece of equipment: round and black with a tread to grip the road. Jeremy Miracle, Goodyear materials engineer, says otherwise.
"A tire is a pretty complex product," says Miracle. "It has 20 or more components, and each of those components might have from eight to 15 ingredients in a recipe. Our job is to come up with the ratio of ingredients to give us the properties we're looking for."
At the core of their efforts is a process known as compounding, or creating the recipe of ingredients for the different compounds that go into the various components that comprise today's tires.
The process often begins with a request for something new or an expressed need for a certain application. The needs can include improved treadwear, increased fuel efficiency, greater resistance to cutting, or more traction.
Engineers take the customer input and match it to a specific compound to deliver the desired performance. The information is then translated into physical properties for the tire. The engineers work closely with tire designers to create a product that will offer those properties.
Goodyear's compounding specialists use simulation tools to demonstrate how specific compounds will behave, then pass that information along to finite element analysis (FEA) modelers to predict how the tires will perform.
Meanwhile, additional compounds are mixed in the lab to test their properties. Those results, too, are given to the FEA modelers for more fine-tuning.
FEA modeling is a series of virtual tire drawings broken down into hundreds of small elements. The computerized drawings predict how the tire footprint will look under load, how it will respond when cornering, the amount of heat generation, and what kind of strain the tire is likely to undergo.
"This is a computerized way to look at different development designs before you build the tire," Miracle says.
Compound recipes begin with polymers. Each polymer exhibits certain unique characteristics and produces different tire properties. One polymer might be ideal for boosting traction, while another might yield longer tread life. Goodyear engineers have dozens of polymers to work with, many of them produced within the chemical division's lab.
"Natural rubber polymers give you greater tear resistance and lower heat generation, while synthetics will typically run hotter, which cuts into fuel economy," says Warren Bush, head of commercial tire compounding at Goodyear. "Some tread compounds could be 100% natural rubber and some could be 100% synthetic. Synthetics are good for their flex properties, which translates into greater longevity of the sidewall."
Goodyear materials engineers seek a balance between natural rubber and synthetics, depending on the tire's application and desired properties. "If we find a high amount of abrasion in stop-and-start applications, we may want to use synthetics more," Bush says. "But if we use synthetics more, we might compromise the tear resistance."
Goodyear engineers add reinforcing fillers for qualities such as abrasion resistance, strength and durability. Softeners or plasticizers bond the materials together and aid in the manufacturing process; protective chemicals are introduced to keep the materials from degrading and protect the tire from ozone and oxidation damage. During the curing process, the tire is subjected to high temperatures and high pressure. In this step, sulfur, zinc and softeners are added.
The tire development process typically runs from nine months to a year and a half, depending on the complexity of the redesign.
Goodyear's self-sealing DuraSeal technology was a combination of on-the-shelf compounds and materials that had to be developed and fine-tuned during the manufacturing process.
"It was a long process that required adapting technology from the passenger vehicle market to commercial truck technology," Bush says. "It was a formula modification that required time and innovation.
"A lot of people think that compounding is a black art, but it's really a science. We measure and test to know how certain [compounds and materials] perform. We use new and existing materials to change those properties to make better products."
Doug Siefkes is a business writer based in Seattle.