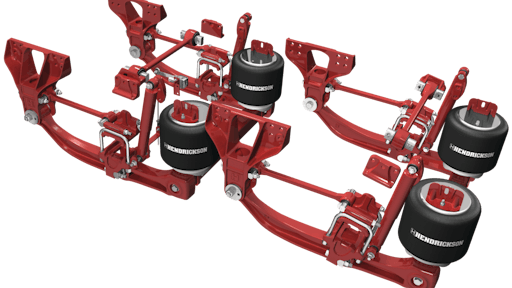
Every day suspension companies are finding new ways to optimize their products. Whether it's decreasing weight or creating a new spring design, companies are continually working to improve suspension systems to meet the ever increasing needs of their customers.
Ashley Dudding, Director of Engineering at Hendrickson’s Truck Commercial Vehicle Systems, Woodridge, IL, says there are numerous factors which suspension companies must keep in mind when designing a product. The application of the vehicle is the first factor to consider because it will determine which type of suspension, such as an air versus a spring, should be used. Dudding continues that various performance metrics, including durability and roll stability, are important aspects to consider as well.
Spring vs. rubber vs. air
Depending on the type of application a vehicle will be used in determines whether an air, spring, rubber or other type of suspension will be the best fit. Each type is designed to offer the best ride performance possible, but how they’re able to handle various environments is the key decision maker.
Hutchens Industries (Hutchens), Springfield, MO, designs mechanical steel spring suspensions, often referred to as spring suspensions, for on-highway trailers. Russ Brazeal, Vice President of Engineering at Hutchens, says the company focuses on this type of technology because while it’s an older technology, it’s also a proven one. Spring suspensions offer minimal initial investment and lower long-term maintenance. Brazeal says that as long as the fasteners are maintained, the suspension is basically maintenance-free, whereas an air suspension has air systems and air bags which can be more susceptible to damage.
With a mechanical spring suspension, the springs themselves are the primary energy absorber. Friction between the spring leaves, flat plates of steel shaped and cut to various lengths then bolted together, or in the suspension itself isolates load from the road to keep the vehicle stable and the operator comfortable. This self-damping method eliminates the need for shock absorbers like the kind that are found in air suspensions, says Brazeal.
Dudding notes that spring suspensions offer a more constant spring rate, which means that when the truck is empty the spring rate is similar to when the truck is fully loaded. This requires the spring rate to be high enough to provide good roll stability characteristics when fully loaded, which can be higher than ideal when in the empty state. This can sometimes cause an uncomfortable, stiff ride for vehicle operators, which is why Hendrickson developed its rubber spring suspensions for vehicles that are used both on- and off-road, such as dump trucks.
Rubber springs feature a non-linear, highly variable spring rate, Dudding says. They provide a lower spring rate when a truck is empty to give the vehicle operator a better ride. Once the truck is loaded the spring rate increases to provide higher roll stability, especially important in vehicles with a high center of gravity. This hleps ensure a comfortable ride in both loaded and unloaded conditions. Dudding says rubber suspension systems “have a lot of articulation, so they have very good off-road mobility.”
This is important when working in a mining application, for instance, where road surfaces are typically rough and trucks are loaded heavily with material to transport, says Dudding. In this type of application high roll stability is key to avoid tipping over when transported material is being unloaded. “[Rubber suspensions] have a spring rate curve that as you increase load on them they develop very high roll stability,” says Dudding.
Both Dudding and Brazeal note that air suspensions have increased in popularity for on-highway applications over the years. Dudding says this is because drivers in on-highway vehicles are very sensitive to comfort and high speed vehicle dynamics. An air ride suspension is able to provide comfort whether the vehicle is empty or loaded “because the air spring changes and gives you an optimized spring rate whatever the load is on the chassis,” says Dudding. Because on-highway vehicles generally don’t have as high a center of gravity, they don’t need a suspension that provides as high a roll stability. The duty cycle is also less severe, enabling an air suspension to last longer than it might in an off-road application.
Creating lighter weight suspensions
For years suspension companies have been working to optimize their products by designing lighter weight suspension systems. “We’re all in a race to the moon to find the lightest weight suspension,” says Brazeal.
Brazeal says Hutchens has been using a higher strength steel to help create a lighter suspension. The high strength steel enables the company to reduce the amount of steel it uses while still getting the same desired carrying capacity and durability. It helps lower costs as well because material costs have risen in the past few years.
The higher strength steel is being used in both the frame and the suspension’s springs. Fewer leaves are needed for the springs, which Brazeal says provides significant weight savings. “[Suspensions] several years ago may have utilized a 10-, 12- or 14-leaf spring,” says Brazeal. “Today they can use a two- or three-leaf spring.”
Using rubber spring technology can also help decrease the weight of suspensions. Hendrickson has been working with rubber springs for several years. Designed to replace the flat leaf springs used in traditional suspensions, the rubber springs are able to carry the same load as a steel spring but weigh much less. “You literally save hundreds of pounds just in the springs,” says Dunning. A mechanical suspension with steel springs could weigh between 1,200 and 1,400 pounds for a 46,000-lb. capacity suspension. A suspension with rubber springs, however, would weigh less than 900 lbs., says Dunning.
LORD Corp., Cary, NC, has found its post vulcanized (PV) bonding process can offer weight savings for suspension systems as well. PV bonding (see sidebar pg. 24) is typically used to bond cured rubber to itself or a component in situations where a component, like a suspension system, is too large to fit into a traditional rubber-to-metal bonding process, says Todd Wallis, Automotive Marketing Manager, Americas at LORD Corp.
Wallis says that in the past, something like a suspension’s stabilizer bar usually required bolting, clips or other fastening devices in order to attach the bar to the vehicle’s frame or other components. The PV bonding process, however, enables the stabilizer bar to be affixed without the additional pieces. Eliminating the need for bolts or clamps to attach the stabilizer bar helps to reduce the suspension system’s overall weight.
Regulatory effects
While creating a lighter weight product has always been one of the primary goals in suspension design, over the past few years it’s become increasingly more important. Brazeal and Dudding both note that payload is an important factor to consider because, especially for on-highway vehicles, contracts are based on how much product can be transported in a certain amount of time. Increasing fuel costs and the implementation of emissions regulations over the past few years have been affecting payload, requiring vehicle manufacturers to find ways to alleviate those affects.
The increased weight of emission-compliant engines has led to a need to decrease weight elsewhere on a vehicle, such as on the trailer or suspension. Dudding notes that some vehicles have had 400 pounds of weight added to meet emissions regulations. “We’ve seen a lot of activity to mitigate the weight gain due to the Tier regulations,” he says.
The recently implemented FMVSS 121 reduced stopping distance regulation for on-highway vehicles has also had some effect on suspension systems. In order to meet the regulation brakes increased in size. Designed with the FMVSS 121 in mind, Hendrickson developed its STEERTEK NXT axles, which provide a weight savings of up to 47 pounds while accommodating the higher brake torques required to meet the reduced stopping distance regulation, says Dudding.
Military applications
Like any off-highway vehicle, those intended for military applications have extremely rough terrain to maneuver through. Designing a safe and durable suspension is especially important because military vehicles are often operating in life or death situations.
LORD Corp.’s Magneto Rheological (MR) Fluid suspensions use MR fluid in the dampers to provide highly responsive, active damping over a much broader control range, says James Yakel, Business Development Manager at LORD Corp. The dampers, paired with a central electronic controller, allow the suspension system to adapt to the terrain the vehicle is driving over, adjusting as necessary to the varying levels of vibration, shock or motion. “The system is designed to significantly improve the effectiveness of the typical military vehicle reducing the time required to conduct missions by offering improved safety and controlled speeds,” he says.
The company designed the MR suspension to easily replace passive damping suspension systems currently in use by many military vehicles. Yakel says the passive systems, which utilize shock absorbers, don’t adjust to changing conditions in driving terrain like an active system does, causing discomfort and travel fatigue for vehicle occupants. Able to fit in the same space as a passive damper, the MR fluid system does weigh slightly more because of the fluid density and heavier-duty construction. However, Yakel notes that the improved roll-over control provided by the MR suspension enables other components, such as roll or stabilizer bars, to be reduced in weight or eliminated completely.
Hendrickson has been working with AxleTech International, Troy, MI, to develop a suspension system specifically for Navistar’s mine resistant ambush protected (MRAP) vehicles. The MaxxPro Dash Suspension System is an independent suspension system with high speed planetary drive axles. Dudding says the independent suspension enables very large wheel travels, as high as +/- 7 inches for 14 inches of total travel, whereas a typical conventional spring suspension might offer +/- 3 inches. The increased wheel travel provides good off-road mobility, allowing the vehicle to articulate over terrain with ease. It also creates a soft spring rate for good isolation and ride quality. With an independent suspension there is high primary roll stability as well, says Dudding, enabling the vehicle to keep its balance.
Future Trends
Optimization will continue to be the goal, and challenge, in suspension design. A continued effort to reduce weight will be key, as well as enhancing the reliability of suspensions.
Dudding says along with weight and performance optimization, there will always be investigations into new technologies or finding a way to make existing technologies work in other applications. For instance, Hendrickson’s high speed planetary axle and independent suspension system is geared towards military applications, but Dudding notes “you will see some of that technology migrate into specialty vehicles like fire trucks” or other vehicles with high performance requirements.
“The challenges are always selecting the right suspension while maintaining a safe, stable vehicle that will carry the load,” says Brazeal, “and providing the durability that’s expected, while maintaining minimum weight and cost.”