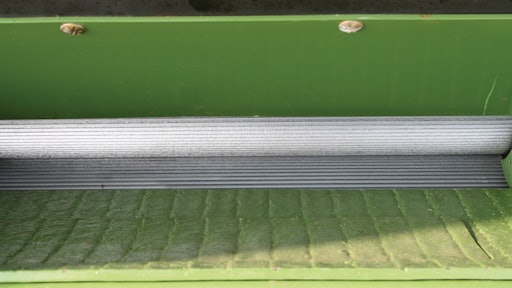
Engines have improved immensely over the last decade, but with end-users and OEMs faced with high fuel prices and ever-tightening emissions regulations, alternative methods are being sought that will glean more work from a gallon of diesel fuel. We're seeing hydraulic or electric assistance installed to work with the compression ignition engine, and in some cases that engine has been removed completely. Bolting a second diesel engine to the chassis might, at first glance, seem to be heading in the wrong direction.
Recently Grove and Krone have done just that, and the two machines actually fall in-line with the efficiency goal because of their two compression-ignition engines.
Unique advantages
In the history of on- and off-road equipment, twin-engined machines aren't unusual — although saving fuel wasn't always the primary reason for their installation. A pair of engines was generally employed in heavy equipment to give the machine the extra horsepower and torque to do its job.
Caterpillar and Terex have offered twin-engined scraper models for years. On a scraper, one engine drives the front wheels (the tractor) while the other runs the scraper and pushes the machine through a heavy loading application.
The new Grove TM500E-2 truck crane from Manitowoc uses two different engines to great advantage: one diesel is rated for off-highway use, while the other is an on-highway powerplant. Both engines are certified to current United States Environmental Protection Agency (EPA) emissions standards (Tier 3 and EPA 2007 regulations).
In the Grove application, each engine is controlled from the respective cab and is completely separate in its function. The chassis engine is controlled from a chassis cab, and the other engine is controlled from the cab on the crane superstructure. The superstructure cab features armrest-mounted electric dual-axis controllers. In addition, the operator can monitor all engine functions from the in-dash gauges. The machine uses CAN bus for communication, although the two engines do not interact.
The TM500E-2's highway carrier uses a Cummins ISC six-cylinder 300 hp diesel that propels the 60,000-lb. machine up to 65 mph. Once at the jobsite, the operator shuts off the chassis engine and fires up the Cummins QSB 3.3 L four-cylinder 110 hp diesel in the crane superstructure. Once the outriggers are extended the crane is ready to use.
"Having two engines significantly reduces fuel usage," says Ruben Olivas, global product manager for Grove's truck crane line in Shady Grove, PA. "By using the superstructure engine to run crane operations, owners can reduce fuel consumption by gallons per hour. This allows customers to get more work from their cranes while reducing operating costs."
Using a separate off-highway engine for the crane also allows the operator to fill that engine's fuel tank with less-expensive dyed off-highway diesel.
Twin-engined cranes are not new to Grove. In 1961, the company's first truck cranes, the TM5 and TM8, had a pair of engines. The last of the smaller truck cranes to utilize two engines was the early 1980s TM200. Larger Grove truck cranes used two engines through the 1990s.
The 45-ton capacity TM500E-2 replaces the single-engined TMS500E Grove truck crane. "We started out to refresh the truck crane line and ended up going back to the future," says Doyle Bryant, director of product marketing, Grove.
Grove engineers were attracted to the twin-engine solution because of the new on-highway engine emissions regulations. "The regulations impact the cost of diesel and fuel mileage and thus the cost of operation," says Doyle. "That pointed us toward a second engine. We can save these guys money by putting a smaller engine upstairs to do the crane functions."
The Cummins QSB engine operates the crane's 29-ft. to 95-ft. four-section, full-power boom. Maximum tip heights are 102 ft. and 110 ft.
The Grove crane's chassis is built to Grove's specific requirements by Autocar LLC, Hagerstown, IN, and utilizes a spring front suspension and air rear suspension.
The TM500E-2 will be formally introduced to the industry at CONEXPO, although units were expected to start shipping before the event. Three pre-production machines have been working in what Grove calls a pre-production partner program. Completed machines were shipped to Massachusetts, Chicago and Maryland/Pennsylvania and put to work.
"That program has worked out real well. We've received good comments back from the customers that used them," says Bryant. "They loved the two engines in the new crane. The first customer noticed right away that the upper structure is sipping fuel, as he didn't need to fill up the tank every day like they would normally. It's amazing when you think we used to have two engines in our trucks. "
Full power
One of the most powerful machines you'll find among the 1,600 exhibitors at World Ag Expo in Tulare, CA, is the forage harvester, designed to compress and chop standing green corn into fine, uniform particles to be used as cattle feed. It takes a tremendous amount of horsepower to do the job quickly and efficiently. As the chopper is moving through the field, it's blowing the material into a trailer that travels alongside the machine.
In August 2007, the Spelle, Germany-based farm machinery division of Bernard Krone GmbH introduced the Krone BiG X 800 forage harvester. It's an 836 hp machine powered by two separate engines, each delivering a different horsepower rating. The Mercedes-Benz OM 460 LA and OM 926 LA engines are sitting side-by-side in a massive "V" formation and are connected by a gearbox which sends power to the chopping unit, infinitely variable hydrostatic ground drivetrain and the wheel-hub motors.
The secret to the machine's performance is where much of the early development work was focused. The engine's different outputs are synchronized through a unique electronic system developed by Krone and Mercedes-Benz, which configures a synchronized gearbox to couple the crankshafts of the two in-line 510 hp and 326 hp engines.
The electronic control system orchestrates the two engines while at the same time ensures the optimized utilization of each engine. Patented software operates the engine control system to balance the load on either engine. Information is sent over the machine's CAN bus (two engines, transmission and chopping information) and is shown in the cab on an EasyTouch 7 in. display to the driver's right.
The BiG X 800 uses much of the same technology found in the class-leading BiG X 1000, which was first announced by Krone in 2005 and which went on sale in the United States last year. The BiG X 1000, however, uses two of the same model diesel engines: two Mercedes-Benz OM 460 LA inline sixes put out a total of 1,020 hp at 1,800 rpm when working together. Thanks to the software, both engines run at the same speed and torque load.
For Krone's customers the dual-engine layout provides several benefits. For one, it can be powered by one or both engines, depending on the job requirement.
On the BiG X 800, for example, the primary 510 hp unit powers the forager in road transport and in light grass foraging, whereas the second engine kicks in as power requirement increases. The forager boasts six pre-compression rollers and an 800 mm wide chopping cylinder with 28 knives arranged in a chevron formation that work together to achieve uniform pre-compression of the crop material and thus an excellent quality of chop. In addition, the Krone forager benefits from a straight and direct crop flow.
Owning and operating the BiG X 1000 requires access to enough acreage to keep it fed. It can harvest 14 tons of corn silage in two minutes. The first BiG X 1000 that will be working crop land in the United States, was sold last year. One customer has already ordered a second unit.
To see where efficiency is found in a machine with two 12.8 L engines, it's important to understand how operators think about their foragers. It's all about achieving the highest output by maintaining a low ground speed. "The faster your groundspeed, the more fuel you are consuming to chop the crop," says Hartwig Janssen, product manager, Krone North America, Memphis, TN. "With a larger machine and a bigger head, the operators don't have to drive as fast as they would to cover the field with a smaller head."
Depending on the average yield and the field condition, a 10- or 12- row head is wide enough to get the fuel saving effect. Yield conditions vary a lot: the average corn yield in Idaho for example is 27 tons an acre, while in Wisconsin the average is 17 tons an acre. The decision as to which size corn head gets put in front of one of the BiG X foragers is based on local growing conditions.
The challenge of using a wider corn head — a 14-row unit is available in Europe for the corn found there — is that the "drum on the BiG X 1000 can take a lot more power to chop efficiently and uniformly and not plug. You get more done while using less than 1/10 a gallon of fuel per ton. It all comes down to the output," says Janssen. Productivity can increase by more than 20% with a larger head.
Additional fuel savings can be found when, in lighter chopping conditions or while transporting the machine, the rear secondary engine can be shut down.
Cool stuff
While it's the practical aspect that has engineers specifying, not one, but two diesel engines for a single machine, there's a definite "cool" factor, too. Take Krone, for example. The German company has been in the United States since 1973 with hay tedders and rakes, all important and respected products to the hay grower, but not particularly exotic.
Janssen says the introduction of the BiG X line of forage harvesters — especially the twin-engined 800 and 1000 models — has helped give the entire Krone line attention worldwide.