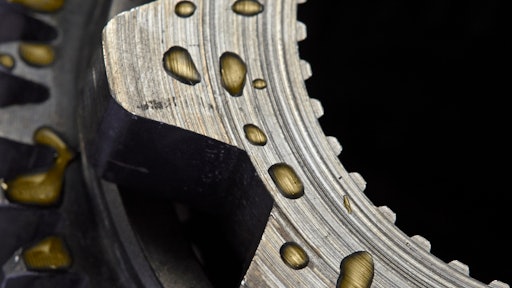
Lubricants play an important role in protecting vehicle hardware, helping to manage friction and prevent premature component wear. And when formulated appropriately, a lubricant can improve performance and prolong the life of hardware, says Anouska Norman, Product Manager, The Lubrizol Corporation.
“To achieve this, the lubricant must be matched to the hardware – any old lubricant won’t do, especially as engine and transmission technology grows in sophistication,” she says. “If an incorrect or substandard lubricant is used, it can shorten hardware life leading to costly repairs, prevent the vehicle from working properly, or working at all, and in some cases, could lead to irreparable damage.”
Because of this, it is important for manufacturers and lubricant formulators to collaborate early on in the development process. Doing so ensures they will develop a system that works well together and avoids potentially costly issues in the field.
As powertrain technology continues to advance due to emissions regulations and increasing electrification, early collaboration has become even more important to ensure lubricants perform as they should in the evolving system designs.
Low viscosity oils
To achieve desired efficiency gains, use of low viscosity engine oils and lubricants has increased in recent years. Stede Granger, OEM Technical Manager at Shell Lubricants, says these fluids have less flow resistance, friction and energy loss which helps to increase efficiency.
“As the fluid gets thinner, it flows more easily through the engine and transmission. This reduction in viscosity improves the overall efficiency of the transmission,” explains Norman. However, she says it’s important to formulate the lubricant so that it still provides the protection necessary for the application.
In some cases, a manufacturer will make changes to its engine or transmission to be more compatible with the lower viscosity oil. Granger says surfaces with a smooth finish are able to tolerate lower viscosity oil and so a manufacturer will change the surface of its rotating parts to accommodate the lubricant. Certain types of coatings are also tolerant of lower viscosity oil, and can be used to ensure compatibility. Lubricant formulators need to be cognizant of any changes made to an engine design in order to ensure proper engine oil performance.Shell Lubricants
Granger notes that engine oil performs many functions; one of the most important is keeping engine pistons and piston rings clean. “In the diesel combustion process there’s some really high combustion pressures and temperatures that are a result of the combustion process,” he says. “As they strive to [design] more fuel efficient engines, and clean[er] burning engines, those temperatures and pressures are going up. As a result, the pistons can run hotter and when [that happens] that can be more demanding on the oil.”
The oil needs to keep the pistons and piston rings as clean as possible to ensure they last the life of the engine. Because of this, a lubricant formulator like Shell needs to be cognizant of any changes a manufacturer might make to increase engine efficiency. Older oils will likely not work as well due to the engines running at hotter temperatures. Granger says development of products like Shell Rotella have a lot of additives built in to keep the pistons and piston rings clean over the entire life of the engine.
To keep up with changing engine designs and needs—such as extended oil drain intervals—Granger says next generation oils are now formulated to be more oxidation resistant and able to handle higher temperatures for longer periods of time.
Granger says when developing its next generation products, Shell will often work with engine manufacturers as they also develop their latest product. Tests are run on prototypes, sometimes evaluating just one aspect of a lubricant, such as viscosity, to see how the products may work together. Changes are then made or other features added to further test and evaluate compatibility.
Early collaboration with manufacturers not only ensures an engine and oil will work together, but also that the right oil will be available for customers once the new engine hits the marketplace.
Lubricant considerations for vehicle electrification
Introduction of more electronic componentry in today’s vehicle and equipment designs has brought about the need to re-evaluate the lubricants used. Norman says the higher voltages and increased use of copper wire in electrified systems increases the potential for corrosion. Electrical conductivity of the lubricant is also a concern as it could contribute to the risk of shock through the transmission or axle housing.
The speed at which electric motors operate continues to increase, as well, causing more heat to be generated and the chosen lubricant to be capable of efficiently managing that heat while also ensuring harmful deposits do not form which could cause hardware damage.
Granger notes electrified systems have introduced more copper into the lubricant, requiring it to be able to work in a copper-filled environment. “As oils age they can generate oxidative products which can be acidic, and we have to be sure when the oils age they can still protect components,” he explains.
Early collaboration with manufacturers ensures an engine and oil will work together.Shell Lubricants
How these challenges are overcome varies. Granger says in the case of increased conductivity, changing the type of additives in the lubricant can be beneficial.
He notes evaluating how the lubricant will perform in the field is an important aspect when formulating it. In some instances, a lubricant will pick up water vapor from the environment, causing changes in conductivity. Working with the OEM early on to assess how a lubricant and the system in which it’s used will perform in the real world is critical to overcoming this issue.
Materials used in a system and their compatibility with a lubricant should be a key consideration for manufacturers. “If the lubricant and materials used are not compatible we could see corrosion, degradation of materials, leakage and shift issues such as shudder (jerky shifting), and noise,” says Norman.
She notes that in one case study, an equipment manufacturer chose a new polymeric material for use in its transmission housing without considering fluid compatibility. “When the transmission was evaluated at operating temperature the polymeric material lost its structural integrity,” she says. “Had the fluid properties been considered earlier, alternative polymeric materials could have been suggested.”
Norman says a lubricant formulator can provide guidance on material choice and lubricant to ensure an OEM achieves its performance targets. “This collaboration will help the manufacturer to create a system that delivers the desired performance while optimizing efficiency and hardware longevity.”
In addition, collaboration with lubricant experts helps to ensure the appropriate tests are conducted to evaluate system fluid and hardware performance in areas which will help reduce risk of failure in the field.
When diesel particulate filters (DPF) were first being developed, Norman says vehicle manufacturers worked closely with lubricant formulators to ensure efficient operation. “Certain additive chemistries can cause deposits to form in the DPF which restrict exhaust flow,” she explains. “In turn this increases exhaust back pressure, reduces fuel economy, shortens the useful life of the DPF, and can cause severe engine damage. Oxidation can increase fluid conductivity over time, which can be potentially harmful to an electrified transmission.The Lubrizol Corporation
“By working together in advance of DPF deployment, a formulation architecture was developed which was less prone to deposit formation. This style of lubricant maintains proper exhaust flow,” she says. “Without this synergistic development DPFs would have needed to be oversized and costlier.”
Norman says that today’s hybrid transmissions have been designed to work with existing fluids. However, as they continue to evolve there will be opportunities to enable enhancements through the use of fluids specifically optimized for the new designs. “By developing the hardware and lubricant in tandem, we will see more efficient systems leading to better vehicle performance and fuel economy.”
She says Lubrizol has developed lubricants which specifically address the technical challenges anticipated with future hybrid and electric drivetrains. “These lubricant technologies will be able to provide performance in electrical compatibility, at extremely low viscosities, in an operating environment of sustained high temperature and potentially high speeds.
“In some areas existing performance criteria may need to be adapted, for example enhanced bearing protection and heat transfer for higher speed electric motors along with stronger foam suppression for the increasingly thinner fluids,” she says. “The increased use of copper components and alloys will also drive more attention to copper corrosion performance and test methods, and improved copper corrosion. In other areas, we have entirely new performance requirements such as conductivity targets and compatibility with polymeric materials of construction.”
As OEMs adopt an electrification strategy and other techniques to improve overall vehicle efficiency, a lubricant that is designed and optimized as part of the system will enable and ensure the hardware performs at its optimum condition, thereby enabling efficiency.