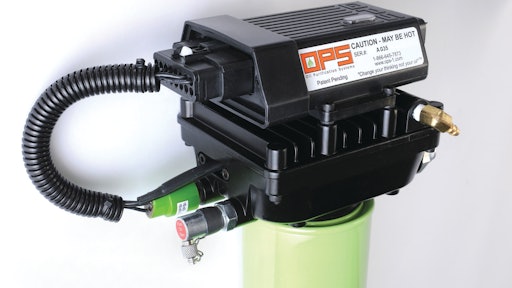
When it comes to engine innovation, the research and development is often required to focus on two primary objectives: 1) increase performance and 2) meet regulated mandates. In the past years, the most obvious engine related mandates have been the emissions regulations put in place by the EPA and EU.
The constant attention to emissions reduction has eaten up a lot of engineering resources, both time and budget. And, while environmental cleanliness is of great importance to the general public in sweeping statements of “green grandeur,” as many OEMs have clarified before, people aren’t willing to pay extra for environmentally friendly equipment. Ultimately the engine and overall machine has to perform better.
Founded in 2002, Oil Purification Systems Inc. (OPS) opted to take a closer look at a system that hasn’t received as strong of attention. “We’ve tried to take a look at the oil filtration system, something that has been around for a while that we felt was underappreciated in terms of the value it could deliver to an organization and the end customer,” explains Greg Slawson, president and CEO of OPS. The company’s line of products builds upon tested and proven products, offering a supplemental filtration system that uses electronic controls to continuously optimize the fluid cleaning process.
The lineup includes Eco-Pur, Intelli-Pur and Intelli-Pur II, Environ-Pur and Enviro-Pur Maxx, among others—the differentiator being engine size and the rate of contamination that is trying to be managed.
Addressing oil contaminants separately
Improved filtration can have a positive financial and economical impact by reducing oil related costs by extending oil maintenance intervals. Secondly, improving oil quality can help to extend the life of the engine system and overall machine. “In that regard, we’re very much in line with OEMs that want to be able to produce an engine or asset that’s going to last as long as possible with minimal maintenance costs,” says Slawson.
“Our approach has been to treat the different sources of contamination differently,” he says. There are two different types of oil contaminants—solid and liquid. Solid contaminants refer to particles that are easy to see and touch like wear metals and dirt. Liquid contaminants include things such as water from the combustion and air intake processes, and glycol from coolant intrusion which can accelerate the formation of acids. “Traditional paper media filters can hold a little water, but can’t get it out of the system.”
OPS ensures efficient and effective filtration of physical particles by bypassing the system and taking small amounts of oil and filtering it allowing it to filter particles as small as 3 microns. Typical full flow filters are only able to catch particles around the 20 micron range, and the problematic contamination particle size is only 10 microns.
The company controls or reduces liquid contaminants in the oil through its electronic evaporation process. OPS creates a catalyst for the liquid molecules to turn into gas or vapor, then creates a pathway for the gas to vent to the atmosphere. The catalyst is agnostic to oil, knowing that each company and fleet owner has a favorite brand or type.
“None of the emissions are harmful that come out of our system,” says Slawson. “We’ve gone through the testing qualifications for the California Air Resource Board (CARB), which is the most stringent in the country. Typically it is water vapor exiting the system.”
System integration is just the beginning
Once the OPS system is put into place, it is only the beginning of the process. After the system is integrated, oil samples are taken and analyzed to show how the oil is behaving. The sampling will also find what the sources of contamination are. “If you have an engine that has a high level of diesel fuel in it that is causing the viscosity to migrate, it’s impacting the overall quality or lubricity of the oil,” Slawson explains. “You’re going to be able to pinpoint where that fuel is coming from, giving the end user a real preventative maintenance tool.”
Certain indicators can let an owner or operator know if the preventative maintenance schedule needs to be reevaluated. “They may not be changing their air filters quickly enough, for example. It’s a great tool to build around to make sure an owner is always optimizing his asset utilization, while at the same time eliminating future repairs that may be more expensive.”
OPS does not claim to rid a system entirely of contaminants however, understanding the dirty environments and long duty-cycles off-road equipment can be operated in. “What we try to do is manage the rate of contamination by eliminating or reducing the solid and liquid particulates that are introduced into the system,” says Slawson. “What we don’t want to do is be so efficient that if there is another problem with the engine, the system would hide that.” If there is a real problem with an engine, such as a rapidly wearing cam shaft, the samples being tested will show high levels of iron or aluminum.
CAN bus
The electronics of OPS filtration products are all written in CAN bus to monitor the internal happenings of the system, including temperature, pressure and flow. The filtration process requires that energy in the form of heat be added to the system to optimize the evaporation process. The added heat does not elevate the oil to a higher temperature than a normal engine would. The electronics monitor the temperature (taking into consideration the ambient temperature to regulate the amount of added heat needed for the evaporation process) and slowly reduces the energy as the oil temperature heats up.
“We’re monitoring those attributes and storing the data in OPS’ system,” says Slawson. “But we can integrate with any OEM if they wanted to make our system an option. We could also offer a data feed to them. Right now we’re working on various qualitative sensors to be able to report oil quality. We can do that using CAN bus to the ECU, or we could send the data through text messages to dispatch a maintenance person, for example or even send it to a website.”
The electronics allow the operator to be hands off to the system. The only system requirements are to change the filter at the designated maintenance time. “It’s like any other filter; it has a finite capacity and depending on the rate of contamination, it’s going to get full.”
For the construction industry, Slawson sees opportunity for fleet managers to be able to utilize equipment without an unexpected oil change or other maintenance. Construction equipment is not consistently used. There are peak operating seasons, job specific equipment perhaps only used for a few weeks, but used 16 hours a day and 7 days a week. Unplanned maintenance costs money and time (which always equals more money lost during equipment down time).
In May of this year, Republic Services (a provider of waste management services) signed an agreement to install the OPS Eco-Pur fluid cleaning system on all of its new 2011 trucks. Republic already had over 1,000 systems installed prior to signing the agreement. In the press announcement, Roy Svehla, senior manager for corporate maintenance at Republic Services stated, “Oil samples don’t lie. Our analysis shows we can safely extend oil drain intervals on even our dirtiest vehicle types, and we are targeting specific vehicles to extend even longer. OPS worked closely with use in tracking and monitoring oil samples at multiple locations to ensure that the oil was clean and our equipment was running as efficiently as possible.”
Republic is installing the Eco-Pur system at their body manufacturers on new 2011 vehicles prior to delivery, and plans to work directly with their chassis manufacturers to install the Eco-Pur system on new deliveries from 2012 going forward.