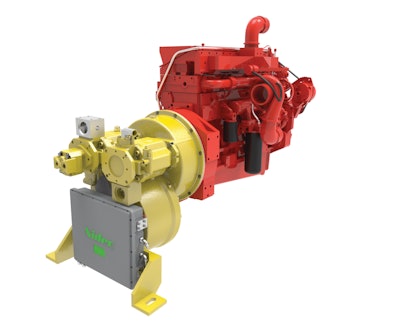
Some companies must reevaluate their business strategies in order to stay the course with the changing tides of technology and the direction of the industry. Others are fortunate to have an established foundation which allows them to capitalize on emergent trends with ease. Such is the case for Oerlikon’s Drive Systems segment (company information, 11531711), consisting of two distinct brands—Fairfield and Graziano—that gave way to the development of its new hybridpower electric drivetrain system announced at CONEXPO 2014. Oerlikon Fairfield (company information, 10056505) focuses globally on gear and drive products for OEMs. Oerlikon Graziano (company information, 10259533) is a recognized developer for electric passenger cars and an early manufacturer for two-speed electric drivelines.
“[Graziano] was an early manufacturer for two-speed electric drivelines, and currently has developed a multi-speed transmission tailored for electrified vehicles,” says Greg Moreland, Global Manager of Market & Product Research for Oerlikon Drive Systems. “Graziano’s subsidiary, Vocis Driveline Controls, has the capability to develop the control logic for these new vehicle designs. What is new for us is that we now have leveraged our capability across our organization to put together a complete driveline system for off-highway equipment.”
So, two years ago, Oerlikon Drive Systems began work with collaborative partners Cummins Inc. (company information, 10055252) and Nidec Corp. (company information, 11531704) on what would become its hybridpower electric drivetrain (product information, 11317459).
Intention
The hybridpower program was the outgrowth of a pure research and development program, along with the company’s historical involvement with electric drive technology. While Oerlikon recognized the industry’s growing interest in hybrid and electric drive systems and their expected increase in applications, the organization had already been developing products that support these systems. “Research in hybrids and power management systems is ongoing and is no longer only of interest only for passenger vehicles. We believe the application for these systems in off-highway vehicles will definitely increase during the next few years,” says Moreland.
Versus a standard mechanical drivetrain, hybrid electric drivetrain technology is able to capture and store energy that would otherwise go unused, which is the benefit that has garnered the greatest interest in the off-road community. Once the energy is harvested, it can be used to lower engine speeds thereby improving fuel performance, as well as channeled back into the system to address temporary energy demands in the duty cycle helping the machine to be more energy efficient and responsive.
“Our intention was to develop and offer a complete hybrid driveline system incorporating a generator, inverters, motors, final drives, capacitor, and the control module and software,” says Moreland. However, each of the elements could be tailored for specific applications. “Furthermore, OEMs may only be interested in certain items,” he explains. While the complete system may appeal to smaller OEMs who lack the internal resources to develop a complete hybrid system, larger OEMs may only be interested in the step-up generator or inverters, for example, and wish to bundle these with existing intellectual properties they have developed internally. “We plan to address both needs and provide configurable systems which match the technology requirements of the individual client,” Moreland says.
The concept system that debuted at CONEXPO (event information, 10207294) was designed specifically for a wheel loader, though as Moreland previously commented, the system is designed with modularity in mind in order to fit each application optimally. A Tier 3 or 4 engine-driven 227 kW switch-reluctance generator with step-up gearing produces electrical power, allowing alternators and starter motors to be eliminated from the system design to improve overall reliability. Cooled, dual power inverters are integrated into the front and rear axles, allowing them to function unconstrained by the mechanical driveline and provide simple, clean wiring.
As the application machine gets larger and/or heavier, there is more opportunity for fuel savings, with severe-duty start-and-stop applications holding the most chance for energy reclamation through the system’s regenerative braking system. The hybrid electric system uses a 1.2 mega-joule ultra-capacitor bank (with operating temperature range of -40 to 65 C) to store energy developed by the generator or recovered through braking.
“The use of ultra-capacitors in heavy equipment has been understood and employed in a few select applications for many years; but, the focus on energy management has been renewing interest as of late. Creating opportunities to consider [ultra-capacitor] inclusion into a much wider base of equipment can be addressed through our system,” says Moreland.
The hybrid system also features a custom software control unit provided by UK-based Vocis Driveline Controls; and finally, four high power density traction motor drives at each wheel end allow for higher motor speeds and good performance over a wide ground speed range. The system design reduces engine speed requirements while keeping a constant engine rpm and letting the driveline govern the speed of the vehicle.
“There are several manufacturers who have been developing technology using different approaches to the drivetrain and energy management,” says Moreland. “These approaches have sometimes included the use of batteries, dual generators and electric motors connected to mechanical transmissions in a parallel drive architecture, whereas Oerlikon’s hybridpower system is in a series configuration.” (Read more on the differences between parallel and series hybrid architecture in Joining Forces, 10166528.)
Throughout the electric drive system’s development process, Oerlikon’s experienced vehicle electrification engineers have been overseeing the program and are responsible for the system’s architecture. “They certainly have been driving the program. But, with a complex system, you need to be aligned with very capable partners who are willing to collaborate and make modifications to their existing products, if necessary. In that regard, the cross-communication between the firms involved has been extensive and ongoing,” says Moreland.
Collaborative engineering is not a new idea (see coverage of collaborative engineering from OEM Off-Highway’s March 2011 article, Collaboration and open innovation, 10226643), but its acceptance with companies is spreading quickly, creating an open dialogue about unique and previously guarded system properties in order to deliver the fully integrated systems OEMs continue to demand, rather than individual components.