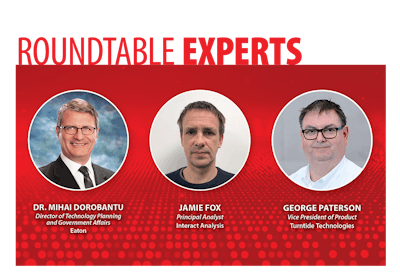
Powertrains comprises the main components that generate power and deliver that power to the road surface and are critical for off-highway vehicles and technology to be successful. The mining, agriculture and construction industries often deal with challenging terrain and conditions and need the technologies to match these conditions. The future of the off-highway industry will depend a lot on powertrains and there are many challenges and opportunities ahead.
These industry experts on the off-highway industry offered their insights on powertrains in a roundtable format:
- Dr. Mihai Dorobantu, director of technology planning and government affairs, Eaton
- Jamie Fox, principal analyst, Interact Analysis
- George Paterson, vice president of product, Turntide Technologies.
Question: How are advancements in fuel efficiency influencing the development of diesel engines in off-highway machinery?
Dr. Mihai Dorobantu: Off-highway engines operate mostly in high-power mode, requiring different technologies than on-highway engines. For example, Eaton’s EGR control technology, tested at Purdue, has shown better than 5% fuel consumption improvement in off-highway cycles. Technologies that deliver 1-2% improvements on-highway can achieve 4 to 6% in off-highway applications. Eaton’s EGR pump, responsible for 5% of fuel savings, plays a significant role alongside friction and parasitic loss reductions. Combined, these advancements can reduce fuel use by more than 10% while cutting NOx emissions by 80 to 90%.
Question: What challenges are associated with integrating alternative fuels (e.g., hydrogen, biofuels) into off-highway powertrains?
Dr. Mihai Dorobantu: Hydrogen offers zero emissions, but presents technical challenges. It requires greater air supply, advanced injectors, and specialized valves to handle Hydrogen combustion stability. Eaton addresses these hurdles with technologies like superchargers, hydrogen recirculation blowers and sodium-filled valves. However, key barriers remain, including hydrogen’s high cost (currently $20/kg vs. a target of $5/kg), limited availability, and expensive storage tanks ($30,000 to $50,000).
Jamie Fox: The major challenges for hydrogen are high machine cost and high running cost due to low efficiency, and the lack of refuelling infrustructure and a hydrogen ecosystem. Hydrogen fuel cells also suffer from complexity and poor resistance to dust and dirt. Hydrogen ICE machines are more familiar, but have even lower efficiency in some operating conditions. Biofuels currently suffer from issues of availability and high cost. Biofuels also use a large amount of land which may make them unrealistic on large scales.
In farms where there is existing suitable material already on the land, this may be less of a concern. However, both hydrogen, biofuels and other alternatives seem to be a niche opportunity only. I expect diesel to dominate in the short term. In the long term, full electrification is the likely winner in compact machinery, smaller tractors and mining. In larger equipment including bulldozers and larger tractors, diesel will remain in place for a long time, and the long term direction is not yet clear.
Question: What are the current trends in powertrain control systems and their impact on vehicle efficiency and operator experience?
Dr. Mihai Dorobantu: Advanced EGR control, precise combustion timing and co-optimization of aftertreatment systems with engine operations are driving improvements. Additionally, as hybrid powertrains gain traction, optimizing the interplay between combustion engines and electric motors is critical for enhancing efficiency and operator experience.
Question: How is the industry addressing the demand for lower emissions in powertrains while maintaining high performance?
Dr. Mihai Dorobantu: The industry has shown that reducing emissions and fuel consumption without sacrificing performance is achievable, as demonstrated in on-road applications. Off-road systems are now benefiting from similar advancements. A program at Oak Ridge National Laboratory optimized an off-road engine to cut fuel consumption by 12 to 13% and NOx emissions by 90%, exceeding its initial 10% fuel reduction target. Eaton and the DOE are collaborating on technology demonstration programs to further this progress.
Jamie Fox: High performance is achievable with electric powertrains, although it does require a significant amount of knowledge, and development of software, hardware, systems integration, and testing. If performance is required for many hours a day however, it may be worth considering other powertrains such as biofuels, hydrogen, and the most efficient diesels to reduce emissions.
George Paterson: Electric-battery power is the ideal way to reduce emissions. When charging can be accomplished without the use of diesel generators, electric power can be the cleanest source available if generated from renewable resources. Add high-torque, stackable axial flux motors, and performance and space savings are optimized. Batteries are being designed with advanced lithium cells that allow fast charge and discharge to meet the demands of high-performance applications.
Question: What is the industry's approach to lifecycle sustainability, particularly concerning the recyclability of powertrain components?
George Paterson: Turntide partners with a battery recycler to make sure we provide sustainable options for original equipment manufacturers and their end users. Currently, more than 95% of lithium-ion battery components can be recovered through the recycling process. Increasing regulation in the industry means that more batteries will enter the recycling chain.
Question: How are manufacturers balancing the need for power and torque with the push for more efficient and sustainable powertrains?
Dr. Mihai Dorobantu: Manufacturers are leveraging hybrid systems to improve efficiency while enhancing performance. Heavy-duty hybrids can reduce CO₂ emissions by 30 to 40% while improving low-end torque, acceleration, and gradeability. Electrification enables rapid acceleration and improved power delivery, creating powertrains that outperform traditional systems in efficiency and functionality.
George Paterson: High-torque, small-footprint axial flux motors are extremely efficient for traction and hydraulic applications. They are particularly well-suited for fully electric or hybrid equipment or vehicles. Advanced manufacturing techniques mean that more of the motors raw materials can be recovered and recycled.
Question: What are the latest advancements in lubrication technology for extending the life of powertrain components?
Jamie Fox: For hydrogen internal combustion engines (ICE), the current lifetime of injectors is very low, and this is mainly due to the lack of lubrication in these machines in operation. Therefore, new injectors, with new types of coating, have been developed, but this market is not very mature. A very substantial improvement in injector technology is necessary before this technology is fully commercialized. However, many industry experts believe that this is plausible. Bosch is one of the leaders in this area.
Question: What methods are most effective for monitoring wear and tear on critical powertrain components?
George Paterson: On benefit of battery-electric systems is that they are durable, reliable, and virtually maintenance free. This includes the high-performance axial flux motor and modular battery systems.