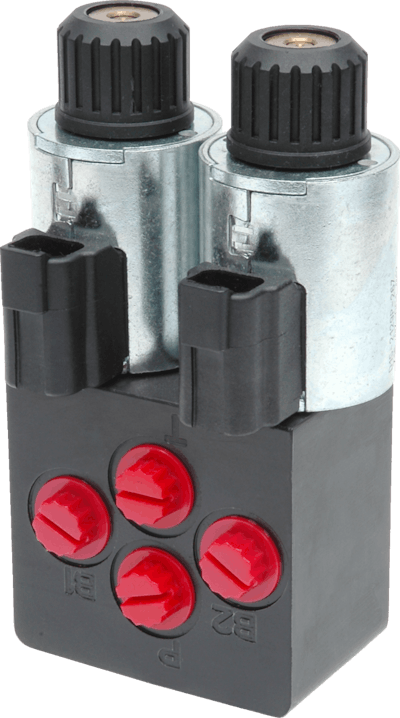
Though intelligent systems and electronic precision are continuing to be demanded in the heavy-duty equipment arena, hydraulics continue to reign in power density. Electrical and mechanical brake systems cannot, at this time, compete due to their size and weight. And, while pneumatic brake systems can come close to the benefits obtained by full power hydraulic versions, because of their lower operating pressures, the accumulators are larger which is often difficult to accommodate with vehicle space constraints.
Larger equipment in off-road markets such as construction, agricultural and mining have several benefits to gain from employing an electronic and hydraulic hybrid system (electrohydraulics or EH), building upon the existing hydraulic platform that has been established and enhanced throughout the years. “The full power hydraulic brake system uses the same operating fluid, reservoir and pump. There is no need to add an air compressor, air reservoir, dryer or other items specific to the needs of [a pneumatic] system,” explains Peter Backes, Senior Product Engineer, MICO, Inc.
“The fluid within a full power hydraulic brake system is virtually incompressible in comparison to air in a pneumatic brake system. This allows for very rapid changes in brake control by modulating pressure in the brakes,” Backes continues. The responsiveness of a hydraulic brake system is most apparent when executing control in anti-lock brake systems (ABS), traction control systems (TCS) and electronic stability control (ESC) events.
MICO, Inc will be launching its MOBEUSTM electrohydraulic braking system platform at MINExpo 2012 (Booth 7557) in Las Vegas, NV. MOBEUSTM, which stands for Mobile Braking Electrohydraulic Utilization System, consists of several of MICO’s electronic and hydraulic products contained in a fully optimized system to deliver an integrated braking package that offers advanced operator control through ABS, Traction Control and ESC. The company’s aim is not to sell the change to ABS and EH braking. “The change in the industry is already happening,” says Len Walton, Director of Sales and Marketing for MICO. “Military vehicles are being driven by 18 year old soldiers who are used to ABS, TC and ESC on their personal vehicles at home.” In several off-road industries, the decline in skilled operators has made vehicle operation simplification essential, so drawing similarities in drivability from familiar passenger vehicle brake systems is a step in the right direction to accommodate new operators and keep safety and productivity benefits possible.
The theory for ABS has not changed in nearly 30 years, though its applications are continuing to diversify as heavy equipment operators expect the drivability and responsiveness of automotive passenger vehicles. In an ABS event, the goal is to prevent the wheel from locking up which can improve vehicle control during braking, and reduce stopping distance on slippery (split or low coefficient of friction) road surfaces by limiting wheel slip and minimizing lockup. Reducing wheel slip improves vehicle stability and steerability during braking. Traction control improves vehicle acceleration under low traction conditions by controlling excessive wheel spin. Stability control adds sophisticated sensors which detail the yaw rate, acceleration and other vehicle orientations. [see figure 1 to see the relationship between tire slip and friction utilization]
The general theory of operation behind an electrohydraulic brake system has the electronic control unit (ECU) monitoring wheel speed and brake line pressures with sensors added to the machine. When wheel lock-up or wheel slip conditions exist, the ECU’s embedded software algorithms determine the current needed at the electrohydraulic control valves to improve the operator’s control of the vehicle. The traction control algorithm attempts to regain traction by braking the spinning wheels, and sometimes throttling back engine power through the vehicle communication network. System status outputs are provided to light ABS and low traction indicators for operator warning and to meet on-highway regulations (FMVSS 105 and ECE R13).
The MOBEUS electrohydraulic brake system is built upon the existing full power hydraulic brake system supplied by MICO. The EH system is established by taking the full power brake system and adding a layer of sensors, controllers, and valves and connecting them all through a wired network. MICO’s proprietary LINC (local interface network communicator) provides system diagnostics in the field and is made up of a laptop, the diagnostic and tuning software, as well as a USB-CAN adapter to communicate with the vehicle’s electronic control unit (ECU). “Everything [in the brake system] is the same; you just add more sensors and actuators to it. The total cost of adding sensors has come down significantly in the past few years,” comments Manfred Maiers, EH Group Director, MICO. “Fundamentally, all MICO stability control systems are similar at the core, but differ through tuning to the specific application like the vehicle’s weight distribution and other parameters.”
Historically, MICO has tuned the stability control system on the vehicle itself, but the company is finding it needs a prototype in order to tune the system correctly and “the military is not comfortable supplying us with a prototype, so we train them to tune the system themselves,” Maiers says.
The basic system evolves to suit the application based on the number of axles by adding more components and manipulating the controller algorithm. “The most important thing with adding ABS and traction control to a brake system is the safety it adds for steerability and control of the vehicle, especially heavy equipment.” ABS configurations are described by the number of sensors and the number of modulator valves on the vehicle. For example, a system that four sensors and two modulation valves is denoted as 4S / 2M. If the vehicle has four wheels (such as a dual axle ag-trailer) then it follows that all wheels are sensed but some wheels share modulation valves. The MICO traction control option adds one additional modulation valve for the TC function.
While the system is able to be retrofitted onto preexisting systems, ultimately EH technology should be developed and implemented during the vehicle design phase. If a system is simply retrofitted, sensors such as the wheel speed sensors that would benefit from being embedded into the axles are left to be mounted externally and exposed to potentially hazardous and rugged environments, especially in off-highway applications. And, while the concept of embedded sensors is not foreign to an axle manufacturer, incorporating a sensor into the overall axle design is always preferred versus adding it in after the initial design is already done.
“What we’re trying to do is build a system that can be easily configured to work on different vehicles without redesigning them,” says Maiers. “By using existing MICO hydraulic brake products and incorporating the electronic system, we’re essentially shifting from being a component supplier to being a system provider.”
The system is created to be regulated globally, meaning the Functional Safety regulations that have been in Europe for nearly 10 years are met by the MOBEUS system. “We’re not going to wait for the regulations to enter North American markets, we want to comply with the most stringent international standards,” says Maiers. When ESC detects loss of steering control, it automatically applies the brakes to help "steer" the vehicle where the driver intends to go. Braking is automatically applied to wheels individually, such as the outer front wheel to counter oversteering or the inner rear wheel to offset operator understeering. The MICO ESC system also reduces engine power until control is regained.
ESC does not improve a vehicle's cornering performance; instead, it helps to minimize the loss of control. ESC helps during oversteer and understeer situations. Oversteer can occur if the driver swerves to avoid an obstacle, making the vehicle turn more than intended, ultimately spinning. The rear of the vehicle might skid out and turn the car in the same direction as the steered direction, but at a faster rate and not under the control of the driver. ESC can prevent this by braking individual wheels to maintain control. Understeer can occur if the vehicle drives too fast into a corner. This would result in a loss of steering control as the vehicle continues to follow a straight path. ESC can help retain steering control and allow the vehicle to travel in the desired direction. According to Insurance Institute for Highway Safety and the U.S. National Highway Traffic Safety Administration, one-third of fatal accidents could have been prevented by the technology.
Ahead of regulations
The Department of Defense (DOD) recently required the use of an ESC in the Joint Tactical Vehicle family of vehicles (JLTV) program. The MICO ESC system meets the equipment and performance requirements stated in Federal Motor Vehicle Safety Standard (FMVSS) 126, "Electronic Stability Control Systems."
In May of 2012, the U.S. Department of Transportation (DOT) National Highway Traffic Safety Administration (NHTSA) proposed Federal Motor Vehicle Safety Standard (FMVSS) No. 136: Electronic Stability Control Systems On Heavy Vehicles (To read this proposal in full, go to www.oemoffhighway.com/10760121). The summary of the preliminary analysis states that the standard would only apply to “truck tractors and buses with a gross vehicle weight rating (GVWR) greater than 11,793 kilograms (26,000 pounds). Specifically, the applicable buses (large buses) are those that have 16 or more designated seating positions (including the driver), and at least 2 rows of passenger seats, rearward of the driver’s seating position, that are forward-facing or can convert to forward-facing without the use of tools. This proposal does not apply to school buses and urban transit buses sold for operation as a common carrier in urban transportation along a fixed route with frequent stops.”
The proposal continues, “ESC is one of two types of stability control systems that have been developed for heavy vehicles. The other one is roll stability control (RSC) which is designed primarily to mitigate on-road, un-tripped rollovers. ESC, on the other hand, not only includes the RSC functions but also is designed to mitigate loss-of-control (LOC) crashes that are caused by yaw instability. The National Highway Traffic Safety Administration is proposing ESC for addressing both first-event rollover and LOC crashes. …The proposed performance criteria are 1) Engine Torque Reduction, 2) Lateral Acceleration Ratio, 3) Yaw Rate Ratio, and 4) Lateral Displacement.”
“It’s a significant savings to prevent accidents from happening, but there has been a draft to get ABS on trailers for about four years now, and its sitting there because a lot of OEMs are pushing against it due to cost concerns,” says Maiers.
“There are different reasons for EH functionality becoming regulated. Companies like Bendix and Wabco, two of the largest ESC system producers, push to get ESC legislated [in the states] because it is in their best interest. In Europe, ABS on agricultural tractors and trailers is being required as tractors will drive on the highway a lot more than in the U.S. because of the smaller field sizes separated by public roads. What we’ve seen in the past is about a 5 to 10 year lag between when legislation gets passed in Europe to get passed in the U.S. So we’re looking at as far out as 2020,” says Doug Lamoureux, Strategic Product Manager, MICO, Inc.
Benefits built upon existing technology
MICO entered the electrohydraulic market in the mining industry with brake-by-wire systems. “The mining industry can really benefit from the reduced tire wear benefit possible with ABS and traction control,” says Lamoureux. “When it comes to ABS, there are studies that show approximately 5% savings in tire wear on heavy-duty class 8 trucks, which is a significant savings on replacement tires and maintenance downtime,” agrees Maiers. In an industry such as mining where a single tire can cost over $25,000, a 5% savings is a large number. A typical ABS system costs in the range of $2,500.
Military vehicle government bids are beginning to require EH technology. MICO EH systems are currently on three of seven JLTVs trying to land a contract. “The military is looking to hydraulic ABS because of the power density and the smaller overall system size,” says Lamoureux.
The construction industry has not expressed much interest in ABS or traction control as of yet, however there are benefits to be gained from employing an on-board system that can increase productivity in difficult environmental conditions. “If you have a huge articulated hauler that is slipping in muddy conditions, traction control can be instrumental in keeping the vehicle productive on a jobsite,” says Walton.
As electrohydraulic systems continue to permeate the off-road vehicle market, the safety and efficiency benefits add value to overall equipment design and performance for an OEM and equipment owner. Vehicle electrification and smart systems are quickly being adapted as costs come down on sensor technology. And, as MICO is demonstrating, the trend of becoming a system integrator and offering more than just components is rapidly becoming commonplace in the off-road market. By leapfrogging technological advancements and meeting global standards, system suppliers can encourage faster adoption into markets that are leery of cost increases by demonstrating return on investment and productivity and safety benefits in the long run.