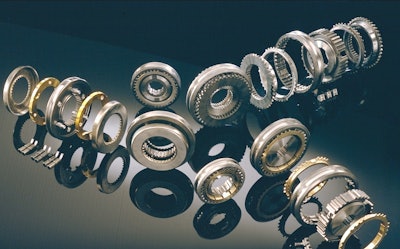
Oerlikon Graziano will launch a new product family called “Shifting Solutions” at bauma 2013 in Munich April 15 to 21, Hall A5–Booth 133, which will combine the company’s design and manufacturing expertise into an engineering consultancy. Shifting Solutions will concentrate on the company’s growing presence in the construction and off-highway industry and provide complete transmission competencies.
“The gearshift system, whether by powershift or synchronizers, is at the heart of any new transmission” says Andrea Serra, Oerlikon Graziano’s Product Manager Synchronizers and Powershift Design. “By designing and supplying assemblies that are optimized for each new application, we help our customers produce more competitive products. Shifting Solutions offers vehicle manufacturers the option of a complete transmission system designed and produced for their individual application.”
Shifting Solutions draws on Oerlikon Graziano’s extensive heritage, extending over three decades. Since designing its first synchronizer in 1983, the company has produced over 20 million units. Current annual output is over 1 million, in sizes from 62 mm to 170 mm diameter. Its history in powershift clutches is equally strong, having introduced Electron Beam Welding (EBW) technology as far back as 1980.
“There will always be customers who require standard off-the-shelf assembly at a cost-effective price, and we will continue to support them,” says Serra. “But for many others, the best solution is to produce a tailor-made design to give an optimum result, integrated into the overall transmission concept to eliminate compromise.”
To provide a complete design and manufacturing service, Oerlikon Graziano uses state-of-the-art analytical tools, such as Finite Element Methods (FEM) to model strength, stiffness and temperature gradients during initial design. Extensive test facilities including vertical and horizontal rigs, heavy-duty fatigue testing, climatic chamber and vehicle test facilities for noise, comfort and shift quality ensure that each new design is fully developed and validated.
The company’s design capability is complemented by investment in the latest manufacturing facilities and methods. By producing Powershift clutches using laser and EBW technology with broached drum details, even the most complex geometries can be manufactured robustly and cost-effectively.
Oerlikon Graziano’s state of the art manufacturing facilities are combined with comprehensive quality control techniques. It is committed to carrying out 100% inspection of manufacturing welds by ultrasound techniques. To maintain maximum control of quality standards, the company is extensively vertically integrated, including process steps such as metal-forming and heat treatment.
Technical highlights from Oerlikon Graziano in recent months include the company’s patented long-life activation system for robust synchronizers with increased endurance life, and a new servo-synchronizer concept. Aimed at the truck and off-highway sectors, the servo-synchronizer uses self-energizing principles to deliver up to higher performance and lower drag torque than an equally sized double cone system of conventional design.
“Our team of engineers works intimately with our customers from the outset, providing on-site engineering support to help achieve rapid program implementation,” says Serra. “We just need to know the transmission application and envelope and then we take care of the rest. Our expertise and experience in synchronizer and powershift technologies enable us to provide a level of service our competitors can’t.”