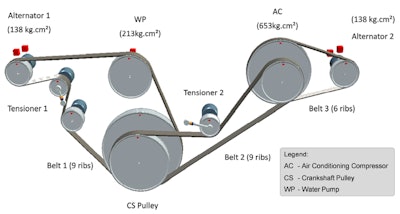
Authors:
Robert J. Laing, Engineering Director, Aftermarket and Commercial
James Muenzenberger, Sr. Manager, Business Development
Litens Automotive Partnership, Canada
Johannes Niederbuchner, OAD Engineering, Litens Automotive GmbH,
Germany
Paper summary:
Reducing vehicle fuel consumption and CO2 emissions are global priorities, due to environmental concerns and newly legislated consumption limits for commercial duty vehicles. Every region in the world has placed new challenges in front of the commercial vehicle manufacturers and suppliers. Means to achieve these strict requirements are numerous. Choosing the path to compliance is complicated and many factors need to be carefully considered.
Recent studies have shown that considerable opportunity lies in the optimization of heavy duty truck accessory drive systems. This study shows that hypothetical optimization strategies can result in fuel economy savings of up to 4%, depending on the duty cycle and application. Every application has a unique opportunity available and requires its own strategy in order to achieve these theoretical improvements; therefore, one cannot conclude that this opportunity exists for every application. However, it does appear clear that reasonable savings can be achieved. Some of these savings can be achieved without major redesign of existing engine configurations.
By utilizing simulation and other predictive tools in engine development, it is possible to estimate fuel consumption, improvement opportunities and CO2 emission reductions resulting from optimizing the auxiliary drive system. Proprietary and innovative clutching, isolating and decoupling technology, which has been widely adapted in passenger car and light truck systems, is now proven to be robust enough for the increased loads and duty cycles seen in Heavy Truck applications.
This article will illustrate several of these technologies; the analytical tools used to quantify and predict improvements as well as provide several real world examples. These robust technologies include overrunning and decoupling pulleys for alternators and crankshafts; controlled switchable water pump pulleys, controlled multi-speed alternator or fan pulleys, and controlled switchable hybridization modules.