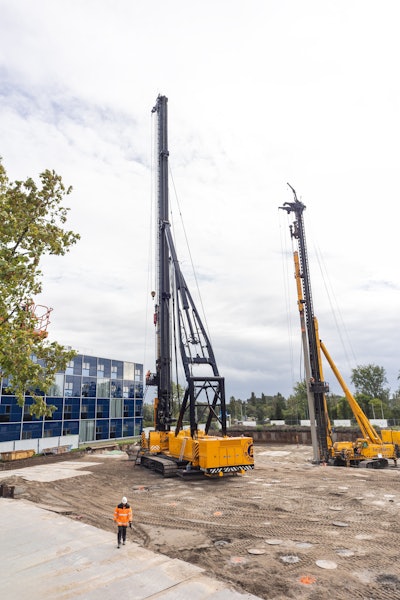
Electrification has always been a major aspect of off-highway vehicles and technology and recent trends have made it even moreso. The mining, agriculture and construction industries are grappling with changes and challenges to the power grid and how their vehicles are powered. This is even more acute with the tide shifting towards alternative energy and fuels as a viable source in certain applications.
These industry experts on the off-highway industry offered their insights on electrification in a roundtable format:
- Dr. Wilfried Aulbur, senior partner, Roland Berger
- Eric Azeroual, vice president, sales development and portfolio, Danfoss
- Lloyd Gomm, global director marketing, ZAPI GROUP
- Brady Lewis, P.E., manager, emerging products & technology, CASE Construction Equipment
- Athan Tsokolas, product manager - commercial Lithium-ion batteries, Vanguard
- Chris Wadsworth, VP and GM, global OEM, Wesco.
Question: What is driving the adoption of electrification in the off-highway industry, and how do you see this evolving over the next decade?
Dr. Wilfried Aulbur: The off-highway industry is pushing towards decarbonization to mitigate the negative impacts of climate change. The complexity of the industry regarding products and applications is a key reason why it is unlikely that we will find a one-size-fits-all solution for decarbonization of the industry. As a consequence, it is imperative to have an application-focused, technology agnostic approach to de-carbonization. Electrification will play a role, either via battery electric vehicles or hybrids, in specific applications. For example, 7 to 9-ton wheel loaders in China have penetration rates of more than 50% for electric vehicles. Key drivers here are a combination of three factors: The availability of the right product, adequate infrastructure and an overall total cost of ownership (TCO) that is competitive vs. alternative options. As battery technology continues to evolve and as battery costs are declining, we do expect more penetration in the off-highway space in the years to come.
Eric Azeroual: Emissions regulations were the catalyst for the development of electric off-highway machinery. Legislation continues to play a role today, but the drivers have started to change. Buyers are interested in performance improvements electric vehicles can provide — instant torque is one example — and TCO calculations are starting to favor EVs. I see this leading to acceleration of electrification in the off-highway industry. We don’t need to convince customers to use EVs; we need to solve the battery/charging problem. There’s some nuance here, as drivers vary by segment and by machine platform. For MEWP buyers, zero emissions means safe indoor operation. In construction, quiet operation can mean extended working hours, as noise ordinances may no longer be a factor.
Lloyd Gomm: There are four aspects to consider:
- Sustainability – Regulatory pressures pushing zero-emission compliance continue to be a factor, but the long-term operational benefits of electrification are becoming stronger motivation for OEMs to make the transition
- Technology – Advances in battery chemistry and charging technology are improving the performance and resilience of electric drivetrains, bringing them en par with traditional combustion engine systems
- Practicality – Besides significant cost-savings over time due to less maintenance and fossil fuel costs, electric systems offer efficiency, reduced-noise and ease of use for operators.
- Economics – The cost of batteries, the most expensive component in EVs, is decreasing, and the awareness of the lower TCO that comes with electrification is increasing.
Over the next decade, sustainability and technology will primarily drive adoption.
Organizations such as the IEA and the UN’s Sustainable Development Goals (SDGs) highlight the gap between goals and reality, indicating that regulatory pressure has yet to peak. As for the technology bottleneck, emerging innovations such as AI are set to overcome it, paving the way for both practical benefits and economic viability.
Brady Lewis: More and more, we’re seeing projects with unique jobsite requirements. Whether it’s urban centers with rules for noise or emissions, confined or congested jobsites, nighttime projects or work that requires indoor operation — EVs provide a clear advantage for these kinds of jobs because they produce zero emissions, minimal noise and require no diesel fuel. EVs also open doors to winning contracts on projects that prioritize green credentials, which are becoming increasingly common.
These trends will only continue. Increasing urbanization will result in more confined and congested jobsites. Cities and states are introducing more rules and incentives to encourage construction crews to minimize disruptions and environmental impact. Some states like California are even offering heavy-duty voucher funds to incentivize the purchase of clean off-road equipment.
Electrification in the construction industry is still in its infancy, and the technology will rapidly evolve over the next 10 years to drive greater adoption. Consider how far EVs in the automotive industry have come in the past decade, as the median driving range has more than doubled in just 10 years. EV construction equipment could see a similar pace of change, which is why CASE continues to invest in electrification R&D.
Athan Tsokolas: Several factors are driving the adoption of electrification in the off-highway industry. Currently, emission restrictions and noise regulations are pushing the shift toward electric solutions, particularly in regions with strict environmental standards. Electric equipment's ability to operate indoors and in enclosed spaces, where combustion engines can’t, is a major advantage.
Looking ahead, key drivers will be decreasing costs and TCO. As technology advances, batteries and electric powertrains are becoming more affordable, making them accessible to a wider range of users. Additionally, enhanced features like autonomous operation and efficiency strengthen the business case for electrification.
Chris Wadsworth: Clean-energy initiatives and zero-emissions goals are driving the increased interest in electrification of off-highway vehicles. Across the globe, companies are working to comply with government regulations and achieve their own sustainability objectives which, in industrial industries like construction, agriculture and mining, require a massive shift away from gas and diesel power. However, the cost to electrify a fleet of off-highway machines requires a significant investment in R&D and willingness to reinvest profits back into the business. So, while companies are eager to invest in electric vehicles (EVs), as it stands today, it’s difficult to do at scale in a cost-effective manner. Plus, there are still lingering questions about how EVs will hold up over time and what type of return on investment they'll be able to provide.
Aside from emissions goals, the promise of autonomous vehicles supported by AI is also driving interest. Without a human operator, these machines can run 24 hours a day, enabling more loads at a mining site, for example. Supported by machine learning technologies, these trucks will also be able to quickly learn the routes in a mine, speeding efficiency and reducing labor costs. This is especially relevant as labor shortages persist especially among remote locations and high-risk environments.
These initiatives are not a small undertaking and strategic partnerships will be key to designing, testing, and implementing electrical systems, batteries, chargers, and autonomous vehicles that can make good on their promises to reduce emissions. Over the course of the next decade those relationships, coupled with improved technology innovations, will help lower the total cost of ownership and ensure those in the industry can capitalize on the promise of electrification.
Question: Which off-highway segments (e.g., construction, agriculture, mining) are leading in electrification, and why?
Dr. Wilfried Aulbur: Electrification in the construction, agriculture and mining industries is a question of application and sub-segments. For example, in construction it is comparatively easier to electrify smaller products such as skid steers. However, these products consume less energy and their overall hours of operation are comparatively low which means that their overall impact on emission reduction is limited. Large equipment is more difficult to electrify given the power and infrastructure needs. This equipment is used more extensively, has higher horsepower engines and as a consequence drives a significant amount of emissions.
In addition, the majority of this equipment is used to drive necessary infrastructure projects in emerging markets which often have less developed infrastructures. Hence for these applications alternative options such as biofuels are more amenable. Which biofuel is chosen depends on the regional context with countries such as Brazil focusing on bio-ethanol while other geographies will focus more on biodiesel or renewable diesel.
Electric solutions in agriculture will focus on segments such as turf where the relatively benign work cycle lends itself to electrification. In mining, we see an effort to electrify even large 240t mining trucks. Here the situation is somewhat different in the sense that companies are making relatively large margins compared to other industries and are driving decarbonization actively to become part of green supply chains.
Eric Azeroual: Mining, material handling and lawn and turf are generally well electrified today. Mines are closed sites where installation of fast chargers makes sense. For underground mines, ventilation can be 30 to 35% of operating costs. If we reduce or eliminate that cost through emissions-free machinery, that’s a huge benefit to owners, and there’s little debate between electric and conventional vehicles. Material handling and lawn and turf are heavily electrified, due to lower power requirements and shorter duty cycles.
Construction and agriculture aren’t as advanced, and that’s primarily due to charging infrastructure, power needs, and machine duty cycles. This is rapidly changing, however. Almost every construction OEM now has a lineup of battery-powered equipment, and we’re starting to see production in significant volumes, especially in mini excavators.
Doosan electric excavators are built using sustainable techniques and materials to minimize their carbon footprint for customers and dealers across Europe.Danfoss
Lloyd Gomm: Electrification has become dominant in material handling, though not always considered an off-highway segment. Forklifts, in particular, see more than 66% electrification adoption. It is also highly prevalent in aerial work platforms, which can be considered as part of the non-road mobile machinery segment.
The success of electrification in these major industrial applications sets the stage for the transition of others, such as construction. Construction is positioning for significant electrification in the coming years to meet the needs of ever-increasing urban, rural development, and compliance with stricter zero-emission regulations. The expanding charging infrastructure, led by the build-out of commercial passenger vehicle charging networks, is helping construction overcome one major limitation — availability of utility power for recharging equipment.
Brady Lewis: As emissions and noise become an increasing concern for urban construction contractors, utilities teams, municipal governments and even landscapers, the construction equipment industry has seen significant advancements toward electrification. With machines that produce zero emissions and minimal noise, it changes the game for where, when and how these crews get work done. Whether it’s urban centers with strict noise or emissions mandates, confined or congested jobsites, nighttime projects, landscaping in quiet residential areas or indoor work for building construction or utilities, electrified machines are providing a clear advantage for these kinds of jobs.
Athan Tsokolas: Construction and mining are leading the electrification of off-highway segments. Construction — particularly indoor applications — benefits from reduced emissions and noise. Mining adoption is driven by safety improvements and automation possibilities that electric vehicles offer. Compact equipment is also embracing battery power because smaller machines can utilize smaller, lower voltage battery packs, which helps reduce costs. Compact equipment is frequently used in enclosed spaces for applications like construction finishing, which benefits from zero-emissions (at the point of use) power.
Chris Wadsworth: It’s hard to find a segment of the off-highway industry that is not interested in electrification. However, given the level of investment required, just how willingly businesses are to fully shift to EVs is another matter entirely. Instead, there has emerged a company profile that is most likely to take the leap into electrification. These often are global organizations who must navigate varying carbon emission requirements and ISO certifications across multiple different countries. Instead of customizing each fleet per region, these organizations are seeking out ways to streamline and design EVs that can be used in any area in which they operate. These entities place a high value on partnerships that can help them through every phase of electrification — from design to operation — and avoid one-off investments wherever possible.
Question: What factors are most critical to achieving cost parity between electric and diesel-powered off-highway equipment?
Dr. Wilfried Aulbur: The key challenge is to achieve TCO parity per unit of output, e.g., per ton of mined material. Drivers in this equation are capital expenditure (Capex) and operational expenditure (Opex) related costs. On the Capex side, the cost of electric vehicles needs to come down to be competitive with ICE vehicles. In addition to vehicle costs, we need to find ways to optimize capital expenditure for putting charging infrastructure into the ground. On the Opex side, overall energy cost per hour of operation needs to be significantly lower than the diesel equivalent.
The more the equipment runs, the more benefit such a cost delta can generate to allow investments in higher equipment and infrastructure costs. However, there are a lot of other factors to consider as well. For example, how much of a detriment are charging times during the work cycle of a product? Each application tends to be different and results for, for example, mining trucks will differ from the specific mine in which they operate. Innovative approaches in on-highway provide us with hope that some of the challenges will find pragmatic and workable solutions over the next years.
Eric Azeroual: Electrified vehicles are becoming more competitive, but initial purchase prices remain high due to the cost of batteries. Battery prices are decreasing, but they’re still one of the most expensive machine components. Pricing is multiples of on-highway vehicle battery costs, driven by the lower volumes, customized packs, and ruggedness required for off-highway use.
Advances in battery technology that reduce costs and improve energy density will be a critical factor in achieving cost parity. Solid-state batteries, for example, provide higher power density and they are lighter and faster to charge. Improving machine efficiency will also have an impact by reducing battery sizes, particularly on larger machines. Production scale will reduce EV machine prices as adoption ticks up. In that way, continued emissions regulations and incentive programs driving buyers to EVs will also play a role.
Lloyd Gomm: Three things to consider:
- Batteries – Batteries are the most expensive component in an electrified machine. While battery material costs are coming down, efficiency and performance are expected to improve. New chemistries are on the horizon, offering higher power densities. Battery health is also a key consideration. Poor care of batteries leads to reduced life, lower performance and early replacement — all of which will be detrimental to the TCO.
- Charging infrastructure – access to charging infrastructure is improving with continued build-out of charging networks (with higher power levels) to meet the needs of more electric passenger cars/vehicles.
- Reduced operational costs – Electrified systems are less complex than combustion engine equivalents. This reduces the need for more specialized service technicians, less parts to service or replace (from wear, tear or failure).
Electrification is well established in construction lifts in North America.Delta-Q Technologies/Discover Battery
Brady Lewis: The battery system is the most expensive component in an electric machine, so everything we can do to optimize energy demand and battery life will help bring cost parity with diesel machines. That means purpose-building machines as EVs and looking at every aspect of the machine to optimize energy efficiency. Optimizing systems, from the transmission and drivetrain to the heating and cooling, can significantly reduce the demand on the battery and allow for more cost-efficient designs. It's also important to note that the cost associated with EV batteries is quickly declining as the supply chain begins to mature, and the energy density is improving as the technology evolves. As this trend continues, we expect to see better cost parity between electric and diesel-powered machines.
Question: How can OEMs and suppliers address concerns around TCO for electric off-highway vehicles?
Dr. Wilfried Aulbur: Addressing cost in electrified off-highway vehicles takes a broader look at the ecosystem and requires collaboration from OEMs, suppliers, fleets, charging infrastructure providers, utilities, etc. In principle, we are dealing with a chicken and egg problem. Without competitive vehicles and adequate infrastructure, fleets find deployment of relevant volumes of electric off-highway vehicles unattractive. Without volumes, OEMs and suppliers are hard pressed to reduce cost and charging providers have no business case for their infrastructure investments.
Ways out of this challenge must include leveraging automotive and other scale effects as much as possible. Modular design can help drive these scales and efforts to improve the overall cost position of the company can help drive costs down as well. Innovative financing models can reduce the initial burden on fleets and share the technology risk between fleets and OEMs.
Eric Azeroual: TCO can favor electric machines. Operating costs tend to be lower because electricity prices are more stable and generally less than fuel prices. Maintenance costs are also lower because there are fewer moving parts and service items in an electric vehicle. For assurance that an electric vehicle will provide TCO benefits, buyers should perform a detailed life-cycle cost analysis that accounts for upfront cost of the machine and charging infrastructure, including subsidies, as well as long-term costs including energy, maintenance, productivity/downtime, battery replacement and, eventually, estimated resale value.
Lloyd Gomm: Awareness is essential. A significant discrepancy exists between perceived and actual total cost of ownership (TCO) in electrified machinery. Studies confirm that electrified machinery maintains a consistently lower TCO versus combustion equipment. The challenge lies in effectively communicating these long-term savings to drive adoption.
Brady Lewis: The total cost of ownership for an EV can include both the upfront purchase price and the ongoing costs of operating the equipment. Many customers are saving on the ongoing operating costs, primarily driven by maintenance savings and the relative cost of electricity vs. diesel fuel. The upfront purchase price is the most significant item for someone trying to "run the numbers." In that regard, off-highway OEMs making EVs can see the progress made in the automotive industry. As with any new technology, the early product generations are more expensive. As technology matures and increasing volumes improve economies of scale, the cost typically decreases.
Chris Wadsworth: At this point in time, EVs are a significant investment for any organization deploying or selling off-highway vehicles. Streamlining development and working with experienced partners that can help navigate the design process, provide clarity on the right technical innovation, and understand the intricacies of deploying electric fleets on a global or regional scale can help address total cost of ownership concerns from the outset.
Additionally, some companies that are looking to “dip their toe in the water” are utilizing rentals or other subscription models to better understand the capabilities and costs before making a larger investment. OEMs and suppliers that understand these models can help their customers determine which model would best fit their needs.
Question: How do you see collaborations between OEMs, suppliers, and technology companies shaping the future of electrification and electronics in this space?
Dr. Wilfried Aulbur: There are different approaches in the off-highway space regarding new technologies. Some players are leveraging their market might and dominant position to establish de facto independent ecosystems. Others focus on solutions that are more clearly positioned as retrofit options and as "color-blind" options that function across various vehicle brands. Which way is ultimately successful will depend on the value that is created for customers.
Eric Azeroual: Collaboration can make or break an OEM’s electrification efforts. While larger OEMs generally have dedicated electrification teams, smaller OEMs may need to extend the capabilities of their internal teams with external support. Suppliers and systems integrators can evaluate vehicle needs and assist with machine design. Danfoss works with OEMs not only to design and optimize the electric powertrain, but also the hydraulic architecture to maximize efficiency and performance. As a system supplier, we have a comprehensive understanding of the application. We know how to put everything together in a system. We don’t just offer components; we help customers integrate them into their vehicles.
Collaboration extends to buyers, as well. OEM representatives should be ready to assess a customer's facility and power needs, addressing potential infrastructure limitations and guiding them through the complexities of charging infrastructure and integration. Guidance on how electric vehicles impact operations may also be needed: how and when to charge vehicles, how long it will take, factors affecting charging speed, how to train new operators, and more. This will ensure a smooth transition to electric machinery with fewer surprises.
Lloyd Gomm: Given the relative infancy of electrified non-road machinery, cross-industry collaboration is essential to accelerate adoption. The success of these partnerships revolve around:
- Cross-sharing successes and learnings around development, as well as market dynamics, regulations and emerging needs
- Developing greater supply chain resilience across critical materials
- Component standardization and modularization (including software) to reduce cost and improve interoperability
- Supporting charging infrastructure development enabling widespread deployment.
Athan Tsokolas: Vanguard believes the future of electrification and electronics in the off-highway sector hinges on collaboration. Our Battery Technology Partner Program fosters a collaborative ecosystem across the entire value chain. We connect OEMs to suppliers and technology companies to help drive innovation and accelerate the development of cutting-edge electrification solutions. This integrated approach ensures that OEMs, particularly small- to mid-sized ones, have access to the latest advancements in battery technology and benefit from shared engineering expertise.
We also recognize the challenges OEMs face in sourcing and integrating various components for electrification. To address this, we're developing a complete electrification ecosystem that includes electric motors and motor controllers specifically optimized for our Vanguard battery technology. This provides a streamlined, fully integrated system solution and simplifies the process. OEMs get seamless compatibility, reduced integration challenges and optimized performance when they prioritize a single-system solution. This complete system and collaborative approach drive a future of broader electrification adoption.
Chris Wadsworth: Collaboration is a critical part of making electrification more widespread in the off-highway industry. End users, OEMs, manufacturers and distributors must all communicate and work together to figure out the best path forward. Technology is constantly evolving and improving; staying on top of those nuances and understanding how they impact design can be overwhelming. By communicating and collaborating, the industry can avoid a one-off, overly customized and time-consuming approach and instead streamline the process by developing one EV that can operate in multiple geographies.
Question: What is the projected timeline for widespread electrification in off-highway vehicles?
Dr. Wilfried Aulbur: Widespread electrification of off-highway machines cannot be defined at the overall industry level. As we discussed earlier, some segments and applications lend themselves to electrification and should see significant penetration over the next 5-10, in some cases 15-20, years. Other areas will probably decarbonize using other technologies such as biofuels.
Eric Azeroual: This really depends on the segment and the machine platform and size. Small lawn and turf will approach 100% electric in the next 10 years. Small material handling machinery is already 50% electric. The cost difference between conventional and electric MEWPs is much smaller than other platforms, to the point that a significant majority of new machines are electric. For larger machinery across off-highway segments, widespread electrification depends primarily on the development of charging infrastructure, battery advances, and market conditions, so it’s difficult to predict a concrete timeline.
Lloyd Gomm: We see electrification progressing in stages, closely tied to voltage levels and power demands:
- 2025 – 2027 will see greater electrification of compact, off-highway, 30 to 150 HP machinery
- 2027 – 2030 will mark the rise of commercial, 200 HP+ vehicles.
With continued advancements in battery technology, infrastructure, and policy support, electrification could become the industry norm by 2035.
Brady Lewis: The adoption rate of electric vehicles in a given industry is difficult to estimate now, let alone predict for the future. Like the automotive world, there is a lot of variability across geography, industry and governments. For CASE Construction, we believe the use of EV machinery will continue to grow in the industry. As we prepare for our customers to be successful in the future, we are purposefully bringing a variety of EV models to market where it makes sense for them. At the same time, we will continue to build and develop innovative diesel-powered models. We see EVs as another tool in the toolbox for our construction markets, and we are improving them by applying the same philosophy of customer focus and practical innovation we’ve used for the past 180+ years.
The CASE 580EV, the industry’s first electric backhoe in full production, combines innovative design with powerful functionality for a big leap forward in electric construction machinery.CASE Construction Equipment
Athan Tsokolas: Predicting the future is always a challenge, but within the next 5 to 10 years, electrification will be the dominant technology in the compact off-highway sector. This projection is based on key factors, including the growing adoption of electric equipment as end users experience benefits like improved performance, reduced noise and lower emissions. These advantages enhance the operator experience, reduce costs and boost profitability.
Investment in electrification R&D drives innovation, yielding more efficient and cost-effective solutions. This, in turn, is driving down the cost of batteries and related technology, making it more accessible to a wider range of users. Finally, OEMs are playing a crucial role by actively developing and releasing new electric off-highway equipment, further expanding the options available to customers and demonstrating their commitment to this technology. As these benefits become more apparent, the technology matures and the industry continues to embrace electrification, we can expect to see a significant shift toward electric solutions in the off-highway sector.
Question: What is one breakthrough technology or trend that you believe could revolutionize the off-highway industry in the next 5 to 10 years?
Dr. Wilfried Aulbur: In my view, the immediate future over the next 5-10 years is not about the next brand-new technology but more about how we deploy existing technology and make it work for customers on jobsites. A lot of the basic technology work around decarbonization and autonomy is available today. The next few years will have to focus on how to bring this technology to bear to improve jobsite efficiency at acceptable cost levels.
Eric Azeroual: The breakthrough the off-highway industry needs to accelerate electrification is energy-dense batteries. This would enable smaller battery packs with the same energy capacity, significantly impacting the efficiency and cost of electric vehicles.
Lloyd Gomm: Digital twins technology allows for simulated replicas of real systems. Not only could this validate electrified designs with clear-cut data, it could also serve as the basis for OEM design teams to refine existing machinery with much greater certainty — and at a fraction of the cost. Electronic power take-off (ePTO) is another development that reduces vehicle emissions, improves hydraulic system efficiency and noise reduction compared to traditional combustion-engine support PTO.
Athan Tsokolas: Over the next 5 to 10 years, key technological advances could revolutionize the off-highway industry. Autonomy will continue to advance, which will boost productivity and enhance safety. Simultaneously, ongoing advancements in battery technology promise greater energy density, faster charging and lower costs. But a truly transformative breakthrough lies in the development and widespread adoption of swappable battery technology.
Imagine a future where, instead of tethering equipment to charging stations, operators can quickly swap depleted batteries for fully charged ones. This eliminates downtime and allows for continuous operation — a critical advantage in demanding applications. At Vanguard, we're optimizing our swappable battery technology and collaborating across the off-highway industry to build a robust ecosystem for its success. This involves standardizing battery interfaces and ensuring compatibility across a wide range of applications. Greater OEM adoption will exponentially increase this technology's value by creating an industry-wide compatibility network. This collaborative effort will ultimately unlock the true potential of swappable batteries.
Chris Wadsworth: Off-highway EVs can’t deliver advantages consistently without a charge! For example, what good is an autonomous truck that can run for 24 hours straight if it has to stop and charge every eight hours? Continuous improvement with battery technology, including longer battery life, faster charging, and even onboard charging systems will make a significant difference in the years to come. Additionally, mesh communication networks, used in combination with LIDAR and other sensors, can potentially enable an entire mine or jobsite to function autonomously.