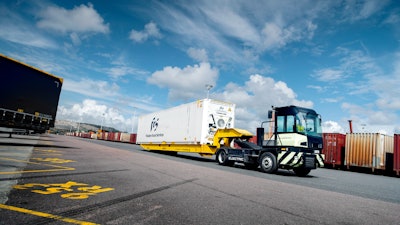
Electrification brings many benefits to off-road machines such as zero exhaust emissions, improved efficiency and significantly reduced noise levels, so why aren’t we seeing more of them yet? Zeyd Okutan, Volvo Penta’s Product Manager responsible for the company’s Industrial Segment Electromobility Product Planning and Strategy, explains what direction the industry is heading in and what needs to happen before electric-powered machines become the norm.
It’s a fact that the benefits of switching diesel-powered machines to their electric counterparts are numerous. They will reduce emissions and help us to fight the climate crisis, significantly reduce noise and vibration levels, improve energy efficiency, reduce energy costs and increase uptime as they have fewer moving parts than their conventional counterparts – meaning that there is less to go wrong. But for electric off-road equipment to become the norm, we’ll need to see the right charging infrastructure rolled out, regulatory reform, incentives from governments, an acceptance and trust in the technology, a reduction in cost and an increase in the pace of technological change.
Paving the way for electromobility
If we look at the passenger car industry, people have been predicting the transition to electric powered vehicles for years. Things really took off when investments in infrastructure and government tax incentives paved the way for change. Of course, consumers were also concerned about the performance, reliability and cost of battery technologies, and these have improved, but it was the reduction in price that really made electric powered cars a realistic option. In off-road machinery we expect to see a similar thing, where incentives and infrastructure readiness play a significant role in demand.
The transition in the passenger car industry is being and will be followed by commercial vehicles like city buses, city distribution trucks and haulage trucks. These will come before off-road machinery because, when it comes to non-road machinery, there is a huge increase in the variety of applications the machines work in. For example, today Volvo Penta diesel engines are providing power to hundreds of different applications in different environments and conditions. Each machine and application has its own requirements based on how it’s used and the legislation for that industry, so there will be no one-size-fits-all solution.
In order for the transition from fossil fuels to electric power to happen, high-power charging infrastructure needs to be taken out of cities to places like industrial sites, agricultural farms, ports and mines – and this needs to be combined with supportive incentives and affordable prices. We have started to see a few examples of this happening in places such as Europe, China and California in the United States.
Another challenge in the off-road industry is how to sort out the energy demand for high power consuming machines. The tipping point here will be similar to passenger cars – when battery-powered industrial machines are affordable, the off-road industry will be ready to make the transition. Battery costs will be the key to this as an industrial vehicle consumes a lot more energy than a passenger car, hence battery costs are much higher. The cost of an electric vehicle compared to a conventional vehicle is significantly higher, and most of this cost comes from the battery itself. Over the last 10 years there has been a good downward trend in the cost of batteries which has helped the passenger car industry, we hope to see the same happening for off-road machinery.
Volvo Penta’s electric driveline uses proven Volvo Group technology and is tailored to meet the application, usage, climate and environment the machine will operate in.Volvo Penta
Collaborating with customers
At Volvo Penta we have lots of customers interested in collaborating with us on both hybrid and fully electric off-road machines. We take a full system approach and want to become the world leader in sustainable power solutions – and we’re well on our way to bringing zero emission results to the market as part of our electromobility journey. We have several development projects ongoing where we have partnered with customers to develop the best electric driveline solution for a specific vehicle.
One of our projects is a fully electric terminal tractor. Here, we’ve converted a terminal tractor to make it emission free and fully electric by incorporating a Volvo Penta electric driveline. We see material handling as the most promising segment for electrification and we believe there is a strong business case due to the high machine utilization in this application, the fact that the machines normally operate in confined areas using known duty cycles, and that there is good accessibility to an electrical charging infrastructure. This is also an area where we are already seeing some incentives to go electric from governments and local authorities. We therefore decided to create a proof of concept for this segment. We’ve been testing the terminal tractor doing real work at a harbor in Sweden in order to implement market feedback into our development work.
Another interesting project we’ve been working on is developing an electric driveline for leading fire service vehicle manufacturer Rosenbauer’s pioneering fire truck, enabling an innovative new solution with zero exhaust emissions and significantly reduced noise levels. By walking away from conventional commercial vehicle concepts and developing an electric solution for the truck’s driveline instead, Volvo Penta and Rosenbauer have introduced a completely new vehicle architecture that looks set to revolutionize the fire service industry.
The truck – named “Revolutionary Technology” (RT) – will soon begin real-world customer testing with fire departments in Berlin, Amsterdam and Dubai. The RT comes under our special vehicle segment and we see this as the second most promising area for industrial electric machines. Other vehicles in this segment include airport ground support equipment and refuse trucks. Looking at the other segments we operate in, I would say that agriculture and mining are the next most favorable when it comes to electric power, followed by construction and forestry.
Volvo Penta has developed an electric driveline for Rosenbauer’s revolutionary fire truck.Volvo Penta
The power of the Volvo Group
As Volvo Penta is part of the Volvo Group, it is in the privileged position to have the strength of the group behind it and all the benefits this brings for sharing technologies. This means that it doesn't need to reinvent the wheel as it starts development work with proven Volvo Group electromobility technology that has already been used globally for a variety of applications across the Volvo Group.
Volvo Buses is one of the world leaders within advanced electrification and hybrid technology, their first hybrid bus went on the market in 2009. The proven Volvo Group design is based on mature technology concepts that have undergone hundreds of thousands of testing hours and real-world use, so our customers have the huge advantage of benefitting from proven, reliable components. By combining the experience from Volvo Buses, Volvo Trucks and Volvo Construction Equipment with the customer, market and application knowledge of Volvo Penta, we can optimize the design and adapt the complete electric driveline system for a specific vehicle, taking into account the exact application, usage, climate and environment it will operate in.
The future is electric
I believe that the off-road industry is already very interested in electrification and OEMs and customers can certainly see the drivers, but they are also aware of the challenges. Even though the large OEMs might be ready to bring this transition to the industry, the speed of change will be defined by the end customer and their needs. Zeyd Okutan, Volvo Penta’s Product Manager responsible for the company’s Industrial Segment Electromobility Product Planning and StrategyVolvo Penta
At this point, I think we can safely say that the transition to electric power will begin in the applications with the smallest energy demand and where there are good charging possibilities during a standard working day. Some segments will go straight to fully electric and some will opt for hybrid machines, this will depend on the equipment’s energy use. For example, a tractor has a very unknown duty cycle and carries out various tasks for different lengths of time – sometimes they can work 24 hours a day, so it’s better suited as a hybrid machine. Whereas in underground mining, where you don’t have the benefit of clean air, fully electric is preferable.
In 5 years, I predict that we’ll see a significant amount of electric off-road machines. And in 10 years, I hope we’ll be looking at somewhere between 20-30% of equipment being powered by electricity.