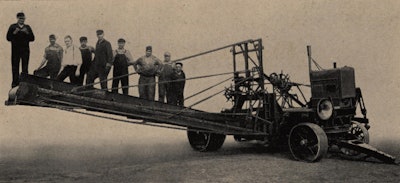
Let’s conclude our look at how Stroud Road Machinery Company of Omaha, Nebraska, trained its salesmen to promote its elevating graders in 1930 and 1931.
Balance
Stroud determined that an engine grader was best balanced by placing the engine on the left front end, diagonally opposite the conveyor. Stroud periodically demonstrated the balance of one its engine graders by positioning a group of employees on the conveyor with about 1,600 pounds on the end of the conveyor, several times the weight of material it would actually carry, the rear wheel on the opposite side lifted slightly.
Competitors’ frames, being more rigid, tended to lift a wheel under load, and digging capability could be compromised. The Adams elevating grader often required a man to ride the plow beam to keep the plow in the ground, and another besides the operator to work the carrier raise. Cat used a telescoping rear axle to balance the grader under load, which Stroud saw as compromising the axle’s strength.
Draft
Conventional wisdom had it that a lighter elevating grader was easier to pull. But other principles came into play as well: Machine weight; frame flexibility; conveyor efficiency; and wheel design.
A tractor-drawn elevating grader’s weight tended to fall on the back axle when pulled by a tractor, and reduced rolling resistance on that axle eased pulling. More weight and lack of rigidity in the frame helped keep all four wheels on the ground, resulting in better digging.
The conveyor’s efficiency also contributed to how easily the grader could be pulled. A heavier side sill, such as Stroud used, kept the belt running true by reducing resistance. Stroud also used roller bearings as standard equipment on the top and bottom rollers, and offered them as options on the idler rollers as well. The smoother the conveyor ran, the less rolling resistance there was, since material tended to move better and not bog the grader down; and on an unpowered grader, less load was placed on the rear wheels that drove the conveyor.
Lugs or flanges on the wheels kept the grader from sliding. Stroud found that lugs impeded draft less than flanges such as Caterpillar used.