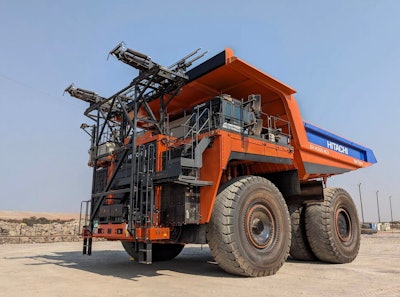
Hitachi Construction Machinery emphasized operating costs, productivity, the environment and mine safety in their press conference ahead of MINExpo on Monday in Las Vegas. Hitachi Construction Machinery is forging a path toward Zero Emissions, Zero Downtime and Zero Entry Mines to reduce fuel consumption and interruptions for a lower cost per ton while enhancing safety by removing employees from mining operation danger zones.
Combining excavator technology with sustainability
When paired with reliable EX5600-7 excavators, their next-generation EH4000AC-5 rigid dump trucks make for a sustainable and efficient mine site. EH4000AC-5 dump trucks have been designed to reduce fuel consumption while enhancing productivity, reliability, and safety. Work mode selection allows workers to choose the optimal mode based on the mining site environment and operating conditions.
In ECO mode, the engine output is lower than the default setting, resulting in reduced fuel consumption. H/P mode provides higher engine output. This model has also been designed with the potential retrofit expansion to trolley diesel and battery systems, making it next-generation capable for reduced emissions. The EH4000AC-5 also has one of the largest payloads in the industry at 242 tons.
Regenerative braking also adds charging capabilities to the battery management system.
The drive towards zero emissions requires a holistic approach that extends beyond the equipment. Mine sites operate 24/7 and they need management solutions to reduce environmental impact while achieving sustainable resource extraction. Fleet management and digital mining solutions from Wenco, a subsidiary of Hitachi Construction Machinery, and Envirosuite, an environmental intelligence company, provide real-time data to enable responsible mining practices.
Hitachi Construction Machinery offers a full suite of digital solutions to solve environmental and greenhouse gas challenges. Through business partnerships and startups, there is a suite of innovative solutions across the full spectrum of mining operations. One example is analyzing driver operation data and machine emissions to calculate optimal operation routes.
The EH4000AC-5 evolved the Hitachi AC drive system cultivated through the current EH AC-3 series models and strengthened the brakes, suspension and other aspects of the undercarriage to achieve smooth, stable driving and superior deceleration performance even under the industry's highest payload of 242 tons.
It also is designed to provide a comfortable operator space and operating environment which enables the operator to achieve the desired level of maneuvering performance. Furthermore, the change to a fully electric specification equipped with batteries and trolley dynamic charging systems that receive power from overhead lines installed at mines is also compatible with the EH4000AC-5 similar to the current EH-AC3 series models.