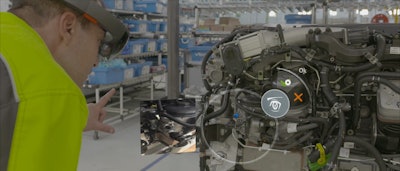
Working with Immersion, the European leader in virtual reality and augmented reality, Renault Trucks will be starting the first phase of testing a new, faster and more reliable quality control process using mixed reality in January 2018 at its Lyon engine site.
The French manufacturer Renault Trucks is studying the potential benefits of augmented reality, and more specifically mixed reality, for production processes. A multi-disciplinary team of 20 employees, created in a similar fashion to a start-up and benefiting from an internal incubator, has designed a prototype with Immersion for using mixed reality to control engine quality.
From augmented reality to mixed reality
Unlike augmented reality, which displays information on top of reality, both laid flat and on screens, mixed reality can add virtual objects into a real environment in the form of holograms, with which users can interact. This is the technology that Renault Tracks is experimenting for quality control at the Lyon site manufacturing engines.
As Renault Trucks has been using Virtual Reality for a number of years, it is convinced it can go further in its use of this technology to improve processes. Renault Trucks experts have identified the technical issues and uses for which Mixed Reality is suited. To put its research and analysis into practice, the manufacturer called on Immersion, which then provided support during the creation of the mixed reality application; from the initial reflection phase to co-designing the experiment and then designing the prototype.
"In practice, quality control operators will wear Microsoft HoloLens smartglasses in which all the digitalised engine parts will be integrated," explains Bertrand Félix, the Renault Trucks engineer behind this project. "Via the glasses and Mixed Reality interface, operators will see decision-making instructions that will guide them through the most complex control operations. At the moment, operators working on control points are still using paper instructions."
Merging the virtual with reality
Each of the engine parts, which are digitalised and superimposed over the actual engine, can be viewed separately, guiding operators towards specific parts of the engine and validating quality process stages one-by-one.
Keeping their hands free, operators can also be sent additional decision-making information, such as plans and verification and assembly instructions. Last but not least, this technology contains numerous embedded sensors enabling users to move around the engine.
Use of this new technology requires specific support. As it provides 360 degree support and focuses on "use" rather than just "technology", Renault Trucks consulted Immersion, one of the leading French members of Microsoft's Mixed Reality Partner Program. Its mission also involves rolling out use of the Microsoft HoloLens among industrial manufacturers.
"In addition to the expertise we have been acquiring in virtual reality since 1994, our added value lies in our multi-disciplinary team that really understands needs and uses in order to offer our customers a global experience," explains Jean-Baptiste de la Rivière, R&D and Innovation Director at Immersion. "With Renault Trucks, we have designed and developed a tool that is perfectly suited to the requirements of the factory, which can be integrated into the manufacturer's industrial processes." The result has come up to expectations – a high-performance solution that meets the requirements of Renault Trucks factories, both in terms of quality and agility.
A practical step towards 4.0 industry
Renault Trucks sees considerable advantages in this technology, as use of mixed reality both reduces and improves quality control operations. It also reduces the cognitive load of operators and accelerates their training. Other applications may be envisaged in a second stage, such as assistance with assembly or repair.
Renault Trucks has set itself the challenge of developing a paper-free, digitalized manufacturing process. This is why the prototype designed with Immersion is already in test phase in the Lyon engine site, with a view to industrialization in 2019-2020.