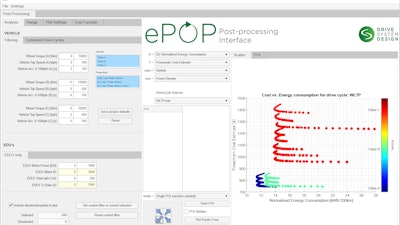
Drive System Design (DSD), a company specializing in the rapid engineering and development of electrified propulsion systems and associated technologies, has made significant enhancements to the latest generation of its proprietary Electrified Powertrain Optimization Process (ePOP). This advanced software-based tool combines DSD’s extensive expertise as well as its unique processes and toolsets to help electrified mobility providers swiftly identify the propulsion systems that best fit their specific needs.
DSD’s innovative and comprehensive analysis tool can quickly review tens to hundreds of thousands of powertrain combinations against cost, mass, range and efficiency, across multiple vehicle drive cycles, types and segments. Through the analysis, it can objectively pinpoint a highly targeted subset of powertrain configurations that best align with customer requirements.
The user interface enables deeper dive capability to plot out various attribute combinations, refine and focus on data inputs giving detailed insight into attribute tradeoffs (e.g. power losses vs. costs) and further analyze the most suitable powertrain makeup. Everything from rare-earth material costs, ratio span and count, performance, motor topology, inverter technology, power density and more, can be mapped out using ePOP.
A core focus of ePOP, which aligns with DSD’s expertise, is to go beyond how each individual motor, inverter and transmission behaves, and instead focus on how they work together at an integrated system level.
“With the shift in demand trending toward highly efficient electrified propulsion systems, the conversation has changed from which parts are most high-performing and cost-effective on their own to how do they work together as an optimized, integrated system that delivers ultimate efficiency at minimized cost,” said Lee Rogers, Senior Engineer at Drive System Design. “Our intuitive ePOP tool offers a simulated environment that gives us the whole system level picture, supporting us in answering those fundamental questions and significantly shortening the innovation stage of powertrain development for our customers.”
ePOP provides customers with a jump-start on the concept phase, especially when they come to DSD with a “clean slate” versus having a specific range of parts in mind. Within a 24-hour runtime, the tool gives DSD the ability to simulate over 100,000 powertrain variants, allowing customers to make strategic product decisions quickly. Overall, the whole process can take as little as two weeks, based on information and data points already loaded into the ePOP system. However, the DSD team can add or enhance the software as new elements or technologies arise.
First developed in 2018 to gather all DSD electrified propulsion development knowledge into a focused and effective toolchain, ePOP has undergone continuous evaluation to reach the level of intuitiveness, efficiency and analysis that it’s capable of today. To-date the tool has primarily been used for passenger and commercial vehicle customers, but as more sectors look toward an electrified future, DSD is evolving the tool to deliver the same critical information to the aerospace, defense and off-highway sectors using fine-tuned data sets and customized criteria most relevant to each market.
Leveraging the tool and using material cost information, DSD also can make trend predictions such as forecasting the technological impact of changes in rare-earth metal costs.
Watch our video interview with Matt Hole, Vice President of Engineering at Drive System Design, to learn more about ePOP and current testing needs for electromobility.