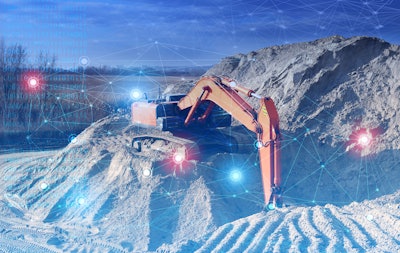
With an increase in automation throughout the machinery sector, technological advancements continue to drive growth and innovation within the global mobile hydraulic market. This growth trajectory looks to continue in the near future, with data from Allied Market Research projecting the mobile segment of the hydraulic power market to grow at a compound annual growth rate of 6.4% from 2023 to 2032.
Amid this growing market and the possibilities that come with trends such as automation and equipment electrification, original equipment manufacturers (OEMs) are faced with the challenge of not only keeping up with the competition, but also staying ahead of it.
For an update on the latest fluid power trends and solutions in the mobile equipment environment, OEM Off-Highway spoke with Mauro Silva (MS), sales technical expert responsible for mobile electronics and electrics, at Bosch Rexroth. Silva, whose components career kicked off in 2004 at AGCO Corporation Brazil, joined the application engineering team at Bosch Rexroth Brazil in 2009. In 2022, he moved to the states to join Bosch Rexroth U.S. and leverage the sales of mobile electronics and electrics in the U.S.
Today, Silva is focused on the company’s electronic and electric products. As he works to identify target markets, market segmentations and value propositions, he digs into problems to understand their causes and pinpoints solutions. Read on for Silva’s insights on the fluid power trends that are shaping the market today and where technology is leading the industry in the future.
What are today's most in-demand mobile hydraulic components?
MS: First is automation — we see an increased demand from OEMs highlighting machine automation. This aspect of off-highway machines is increasingly used to differentiate various OEMs offerings and add value for the end-user, while increasing productivity and operator comfort.
Second is power management — OEMs are ever more cautious about machines that are not as efficient as they could be, leading to bad ROI for their customers. Machine OEMs are demanding technologies and solutions for the most optimal hydraulics control. When adding electrified systems, it makes it even more critical to have efficient power management to thereby reduce battery cost and increase machine uptime.
What are some of the unique applications of automation within the mobile equipment industry, primarily in construction, ag & mining?
MS: We have two examples that have been implemented in thousands of machines by now: compact track loaders and excavators. One of the primary uses for compact track loaders is for the bucket or attachment self-leveling function. In today’s systems, this function is performed by a dedicated hydraulic circuit in combination with the main control valve. Using an electronic solution, this leveling circuit can be eliminated and the self-leveling can be performed via reading the kinematic position of an implement using an MM7 inertial sensor. Besides a higher performance, accuracy and flexibility, this solution represents cost savings by eliminating hydraulic hardware and hoses.
Regarding excavators, grading with a bucket has a higher dynamic complexity as more than one end-effector is present. Moreover, the bucket can grade slopes at various angles and must produce very linear and repetitive results regardless of the machine positioning. The system is similar to compact track loaders, where MM7 inertial sensors are used as the primary form of feedback, and the software adjusts with the complexity. These are only two examples, and the beauty of the off-highway market is that there are so many applications that these automation systems can be applied into, all of them with very interesting results.
How are these components offering OEMs an advantage?
MS: There are several, one of them is robustness and reliability. One way to see feedback in a machine’s joint angles is using angle sensors installed directly on the pins. This, however, results in radial or axial forces in the rotary sensor that can damage it. Using an inertia sensor completely avoids this failure mode as these sensors can be attached to the end-effector at any position along its body. One additional and very important advantage is productivity. Using these solutions results on the operator giving minimal commands for very repetitive movements, which results in less fatigue, improved comfort, and more importantly, very standardized, reproduceable results.
How is this changing operations, efficiency or productivity for end users?
MS: One major complaint we hear is the high turnover of operators, as well as the need to onboard novice operators entering the job market. Most of these operations where off-highway equipment is utilized rely heavily on training and learning on the job, which can be dangerous, time consuming, and inefficient. With the integration of semi-automated or assistance functions, the training time is greatly reduced as the software manages the complexity of any given task, ultimately allowing novice operators to perform as well as experienced operators in certain procedures or maneuvers. This last point can be clearly seen as efficiency improvements for the entire operation.
What are the main challenges OEMs face when it comes to fluid power? What are they trying to overcome and how can you help?
MS: Every application and every sector in fluid power has varying challenges. Some of the common denominators are efficiency, controllability, safety, and sustainability.
Regarding efficiency, our components’ latest generation for hydrostatic transmissions can achieve up to 8% improvement over the previous generation. Moreover, on the open circuit side, the ability of our A10VO eOC pump to lower margin levels and operate as multiple control types, all through software, addresses further efficiency improvement.
Regarding controllability, the electronic hardware that we supply can run very complex algorithms that have enabled Rexroth to move a lot of the mechanical complexity on our components to software. This in turn opens the door for very precise controls that brings best-in-class controllability and operability of off-highway machines.
Regarding safety, all of our solutions are validated through the most rigorous functional safety standards. As a global supplier of systems and components, Rexroth has the application know-how and regulation standards for every part of the world in mind during the development process. Therefore, we ensure that we can offer any performance level for all of our solutions per the OEM demand.
Finally, but not less important, sustainability. This topic is a growing aspect for us to become a supplier in many industries. In mobile applications, our hydrostatic components’ latest generation is up to 33% lighter, which means lower carbon footprint, and combined with the aforementioned improved efficiency improvements, they contribute highly to lower their carbon foot print over their product life cycle.
What are some of your latest product releases for fluid power?
MS: Our latest development is the A10VG Series 60, where we have optimized the design for its accurate control using electronics, minimized the noise level, and improved efficiency. This is truly a differentiator as we continue to emphasize the most important challenges in our industry.
Where did the need for this product come from?
MS: The basic requirement for higher efficiency and lower noise has been part of our product DNA for many years. What’s different with the Series 60 is that we are fully invested in electronic controls. This pump family will only be offered in an electronic control version, which allowed us to fully optimize its design and led to control moments on the swash plate that are identical across displacement sizes. There are favorable moments when the pump is operating as a pump, as well as when it is operating as a motor.
Regarding fluid power trends, where are we are headed next?
MS: At the moment, the trending technologies around fluid power are electronic controls, automation, connectivity and electrification. And that’s a long way from where we came from. We came out of open center systems with gear pumps, and that open center culture evolved with incremental improvements. We then migrated to load-sensing technology and flow sharing, which also evolved incrementally with electronic flow management. Now we're reaching a point where we're looking to electrify the machine and we are re-engineering the entire system to maximize efficiency. More and more we see that the electronic controls are being adopted in the machine. Even simple machines, like mowers, are being heavily automated and electrified.
How is the technology evolving? How do you view mobile hydraulics playing a part in the equipment of the future, specifically with regard to electrification?
MS: Regarding electrification we at Rexroth see the market increasing over the next decade. There are certain applications that might adopt it quick, as it has been done for compact equipment, while there are others where it might make less sense, or the adoption rate will be slower. We also see the hydraulic market plateauing and becoming stable over the next decade. Still, hydraulics will continue to play a crucial role in the off-highway market as a complimentary part to electrification. Our current strategy is to serve the high-power range machines and we have developed a full portfolio around this. We also see that this market is growing, specifically in ports and in large mining or recycling equipment.
What is coming down the pipeline from Bosch Rexroth in the fluid power arena?
MS: As always, we develop solutions side by side with customers with an emphasis on applications. Our clear focus is to develop hardware components that are increasingly electrified and continue pushing the limits on what can be achieved through software. More importantly, we are more and more focused not only on the component, the systems and stopping at the machine level, but rather emphasizing the need to develop solutions for holistic software-centric operations. This is the future of off-highway applications.