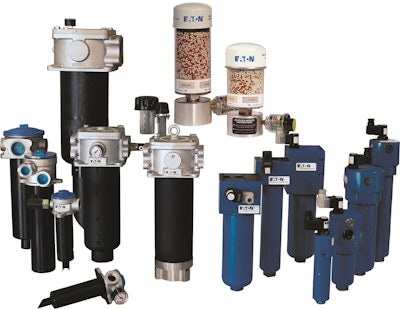
The Filtration Division of power management company Eaton showed its product line of innovative hydraulic filtration and contamination control products at bauma 2016 in Munich, from April 11–17.
Visitors to the booth will meet Eaton’s experts to learn how to reduce operating costs and increase process efficiencies for hydraulic systems of all types. Filtration solutions for mobile machines such as agricultural and construction machinery, as well as industrial trucks demonstrate highly efficient and reliable performance even in extreme climatic conditions and constantly changing requirements.
A range of filters for hydraulic drive systems were represented. These included:
- HPV 240 pressure filters with cold start valves. The filters provide a permanent supply of clean oil to prevent any damage to downstream components.
- The easy-to-change TEF 625 in-tank return line filter with a removable bowl to prevent contamination from entering the reservoir and reduce the possibility of oil spillage during changes.
- The TRS 226 return-line filters with suction connection are tank-top-mounted, in line types that supply clean suction flow and prevent cavitation.
- The tank-mounted TSW 426 suction filters that can be directly mounted onto the reservoir and connected to the suction-line. A check valve prevents oil from draining out of the reservoir during servicing. Continuous operation of the filter supports longer hydraulic oil usage.
Using any of these filters – HPV 240, TEF 625, TRS 226 or TSW 426 – results in longer product life with better fuel usage.
Users can choose from more than 4,000 high performance filter elements available with various filter materials, different construction types and micron ratings to help protect critical system components and achieve cleanliness class requirements.
Visitors interested in contamination control will be able to see the CCS 4 contamination control system. This helps to promptly initiate actions and cost-saving measures before any failure can occur. It enables users to evaluate the precise condition of a system by knowing the particle size distribution of the contamination plus water saturation and fluid temperature.
The CCS 4 system was recently used in Florida by Vac-Con Inc., maker of truck-mounted machines, to minimize penetration of water and other contaminants into its trucks’ hydraulic systems. It led to a significant reduction of failures in the field and resulting warranty costs, while ensuring the cleanliness of oil going into the company’s trucks.
In general, using the CCS 4 system results in better control and longer product life and safety, with better fuel usage.