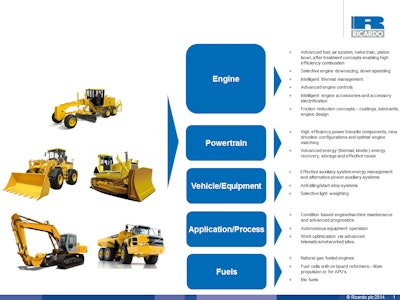
Current tailpipe criteria pollutant levels have already been legislated down to historic lows in the developed world in both on- and off-highway vehicle sectors, with the developing world following suit. As CO2-specific reductions have become the next target—and already implemented within the U.S. and EU automotive industries—the question has become if, and maybe more appropriately when, greenhouse gas (GHG) legislation will take effect in the off-highway sector.
Additionally, continued focus from the end-user community on reducing the total cost of ownership (TCO) over the lifecycle of an asset further prioritizes technologies that reduce fuel costs (typically the largest cost component in TCO). Within the broader GHG reduction technology suite, there are common technologies that are sector agnostic, especially at the powertrain level, and there are sector-specific technologies.
The GHG reduction technology suite can be broadly grouped into five categories—engine, powertrain, vehicle/equipment, application/process and fuels. Most of the technologies relevant to the off-highway sector are currently in use in various on-highway and select off-highway applications. Large-scale adoption of most of the technologies into the off-highway space will likely be driven by legislation or by the technology becoming mature, reliable and cost effective via mass deployment in the on-highway sector.
Engine technologies
Off-highway engine technologies have to date been primarily focused on criteria pollutant reductions – oxides of nitrogen (NOx), particulate matter (PM), carbon monoxide (CO) and hydrocarbon (HC). Meeting emission limits like Tier 4 consumed a majority of the product development resources for most engine OEMs and equipment manufacturers/integrators over the past five to seven years. Looking ahead, GHG reductions will be gained from continued advancements in various engine sub-systems such as the air system (turbocharging), fuel injection system, valve train, combustion, aftertreatment, accessories, cooling, lubricants, controls, materials and overall size/displacement.
Improved in-cylinder combustion will continue to be a key lever for fuel consumption reduction while the air system, fuel injection system, valve train, piston bowl shapes and aftertreatment technologies continue to be key enablers for improved combustion. Today, the typical fuel injection system pressure for Tier 4 systems is approximately 180 to 200 MPa, but overall injection pressures have continued to head upwards with 250 MPa systems currently available (from companies such as Denso) and 300 MPa systems being developed.
Common rail systems will continue to enable more precise control of the overall air/fuel mixing processes during each injection event by providing finer control of pressure, timing, number of shots (9+), adjustment/control of individual injectors and injection events, etc., with a continual focus on reducing system parasitic losses. Air systems—both fixed- and variable-geometry turbochargers (VGTs)—will continue to push overall pressure ratios upwards with improved turbocharger efficiencies and after/inter stage cooling. It will also see the incorporation of technologies like electric assist, electric VGT/waste gate actuation for improved control, and selective use of two-stage and sequential turbocharging.
Flexible valve trains with variable valve lift timing are available in many on-road applications and will continue to be adopted into the off-highway space. However, overall valve train flexibility will most likely be application dependent with variable timing as the most common level of valve train flexibility.
Higher efficiency aftertreatment systems will be used as an enabler for reducing fuel consumption by coupling them with advanced exhaust gas recirculation (EGR) systems (multi-stage cooling, dual loop, etc.) and adequate boosting to further optimize combustion. Engine designs will target higher peak cylinder pressure capability (240 bar Pmax +) which, coupled with advanced air systems, will continue to be an enabler for overall engine downsizing. Engine friction reduction will be a priority, and techniques ranging from selective downspeeding to advanced coatings like thermal spray (which is already used today on select new and remanufactured engines), diamond-like carbon (DLC), control of lubricant viscosity, and various other design features (crank offset, ring pack tension etc.) will be implemented. Another key area of focus will be parasitic loss optimization to reduce losses in the cooling, lubrication and fuel systems via selective electrification of accessories, increased use of intelligent cooling and lubrication tied to actual engine demand.
Lastly, improved control over the variety of engine operating variables will play a key role in optimizing overall combustion and associated fuel consumption. Continuous and closed-loop model-based control techniques enabled by more powerful ECU processing capabilities and advanced sensors will continue to be adopted.
At the end of the day, no single operating variable or technology is likely to be the silver bullet for achieving GHG reduction goals. An engine is akin to an economy; it is a complex multi-variable system with numerous interactions and trade-offs. An engine design and performance engineer uses the aforementioned technologies listed to be able to dial in a calibration that meets specific emissions requirements and fuel consumption targets, while at the same time meeting customer expectations at a market acceptable price point.
Fuels
With the abundance of natural gas in North America and increasing interest in its exploration, production and trading around the world, there is both an environmental and economic argument for using gas to power off-highway mobile equipment. While issues related to fueling infrastructure, on-board gas system packaging and capital expenditure premiums exist, a global environment with favorable gas pricing and/or gas adoption policies will see selective growth of gas-fueled (dedicated and/or dual fuel) construction equipment.
Select exhibits at trade shows and small-scale sales orders of compressed natural gas (CNG) powered construction equipment have been observed in the past two years, especially in China. While natural gas certainly offers an opportunity to reduce tank-to-wheel GHG emissions versus diesel fuel, its overall effectiveness will still continue to be a function of the robustness of the overall engine and gas system design, which will help mitigate any concerns associated with methane slip. Additionally, from a broader well-to-wheels perspective, further GHG reductions are attainable with the use of natural gas by reducing the carbon intensity along the overall supply chain – gas generation (renewable sources versus petroleum), gas transportation (trucking versus pipeline versus shipped), etc.
Cheaper pricing over diesel, a better developed infrastructure than natural gas and simplified emissions compliance technology will drive the use of other lower carbon-intense fuels like propane in select parts of the world. The application of hydrogen-powered fuel cells for propulsion, especially in smaller equipment like material handlers will continue. The fuel cell itself can be powered by hydrogen reformed from various hydrocarbon (HC) fuels with similar tank-to-wheels GHG intensity. Any significant migration of fuel cells for propulsion into a broader segment of construction equipment is still likely to be well into the future, upwards of 15 to 20 years.
The application
Though an asset and its associated technology building blocks may be efficient, its overall effectiveness from a GHG reduction standpoint is still a function of how efficiently the asset is deployed and maintained, and how effectively the desired process is carried out. No engine and powertrain is equally efficient across the whole operating range.
Today, a single off-highway engine is typically deployed into a variety of equipment with significantly varying duty cycles. While application-specific calibrations are carried out, engineers still calibrate a powertrain to operate optimally in select key regions of an application’s duty cycle, and any significant deviation from this in real-world use—either due to operator habits, terrain variation or site-specific usage patterns—will have impacts on overall GHG emissions of the equipment.
In the short-term, operator training will continue to be a key means to ensure effective asset usage. Fleet performance monitoring and work cycle optimization technologies, which today are used in select large-scale operations, will be increasingly deployed with a focus on providing the end-user with maximum asset availability and the lowest TCO, thus ensuring the lowest overall GHG emissions at the worksite level.
With sophisticated on-board controllers, the OEM and end-user have access to increasing amounts of equipment data which will be used in conjunction with improved physical and empirical models related to component and sub-system performance to add even more sophisticated predictive diagnostic capabilities. This in return will empower the end-user to make timely decisions regarding equipment maintenance. Predictive diagnosis of worsening component performance or of an impending failure will increasingly be a tool to limit any increases in GHG emissions.
Intelligent equipment that is fully networked and operates autonomously, which is a current reality in some fleets and equipment in the mining and agricultural sectors, will likely see selective adoption in the broader construction equipment sector. As asset lifecycle costs become increasingly more important than a vehicle’s purchase price for a growing number of end-users around the world , a variety of the technologies that today are sold as premium add-on options or services will make their way into the broader construction segment and act as an enabler for reducing equipment GHG emissions.
The overall vehicle
At the broader vehicle level, reducing idling, selective lightweighting and intelligent auxiliary systems power management will be some of the key GHG reduction technologies. Idling technologies typically range from time-based load sensing to engine speed drops to idle and multiple-idle settings. Technologies like start/stop, which are increasingly prevalent and becoming relatively mature in the automotive sector, will likely see penetration in the construction equipment sector. Additionally, select idle-reduction technologies also go hand in hand with intelligent auxiliary systems power management. When the equipment is not working, the use of a fuel cell or electrical APU to carry out a variety of auxiliary functions like cab HVAC and electric needs enables the engine in the equipment to be temporarily shut off.
Lightweighting will likely be deployed on a selective basis in the off-highway sector, and efforts will be targeted in specific areas—for example, select engine components, equipment body panels or castings. While weight reduction is not the top priority in the heavy-duty construction market, trimming weight can have other added impacts like increased payload capability in hauling applications.
The key challenge for off-highway OEMs in embracing new lightweight materials will be processing and manufacturing related, since the industry has predominantly catered to processing steel. However, with increasing focus on weight reduction in the on-highway sector, the overall expertise of the supply base in processing and manufacturing new lightweight materials is growing, which should bode well for off-highway OEMs if and when a greater emphasis on lightweighting is made.
The powertrain
Going forward, powertrain system design will progressively focus on one or more key elements, depending on application/duty cycle. First, an increase in power transfer component and system efficiencies. This will involve a combination of evolutionary efficiency gains at the component level (pumps, motors, transmissions), complete component architecture changes (e.g. CVTs) and new driveline configurations. Secondly, ensuring engines run at the most optimal performance, i.e. highest efficiency speed/load operating points for maximum possible duration of a specific duty cycle.
Maximizing energy recovery and storage from the engine and machine operation in a cost-effective manner will also be a major focus. While hybrids have accounted for 20 to 30% of new equipment sales in select markets recently, it is still a small fraction of the overall global construction equipment fleet today. Going forward, this share will continue to climb along with the use of batteries as storage medium and other energy recovery technologies like turbo-compounding and flywheel energy recovery systems.
Finally, the effective utilization of recovered energy will be essential. Engine, powertrain and machine system communication is key to ensuring effective utilization of the recovered energy, thus leading to reduced GHG emissions. The ability to use the energy to improve engine and machine transient response, power auxiliary systems, downsize components and even overall engines dictates the overall GHG reductions achieved.
Market acceptance of GHG reduction technologies can and will be impacted by one or more factors like legislation, technology cost maturity (including reliability) and end-user purchase criteria. As legislation related to GHG emissions continues to tighten globally in adjacent sectors, technologies continue to mature, and (most importantly) end-user focus shifts from being heavily focused on capital expenditures to being TCO-focused, these technologies in the construction equipment sector will increasingly have economic merit in addition to the GHG reductions achieved.