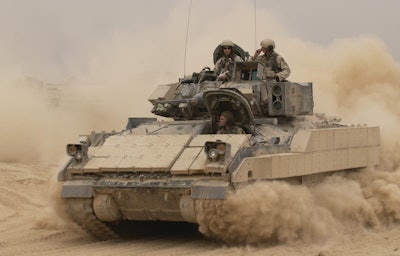
The truck market is changing. In commercial trucking, there are new laws that require trucks to stop in shorter distances and to use alternative energy sources to power the cabin when parked at night. These auxiliary power units (APUs) are more efficient than running the main engine; however, they add hundreds of pounds of weight to the vehicle, as does the new diesel emission equipment. To stop faster, brake engineers respond by increasing the size of the brake.
But, truck manufacturers aren’t sitting still while weight and fuel prices continue to climb. At the Mid-America Trucking Show in March 2012, efficiency offerings included low friction tires, tire pressure monitoring devices, aluminum wheels and hubs, light weight drive shafts, and fairings that reduce wind drag. One truck company even suggested removing the passenger seat to save on weight. Many companies are pursuing alternatives to the traditional diesel engine, including diesel electric hybrids, and those powered by compressed natural gas or propane.
The military has a reputation as an early adopter of new technology due to its unique needs and ability to pay for high performance materials. To protect the Warfighter, tactical and combat vehicles need thousands of pounds of ballistic and blast protective material. And, to provide balance with performance and price, military vehicle engineers are always searching for efficient materials, delivering high strength-to-weight performance.
The military demands high performance over a long life, as demonstrated by the popular M1 Abrams and the M2 Bradley (pictured) Fighting Vehicle, both of which have been in service for over 30 years. High strength aluminum alloys often deliver around 45-50% reduction in weight from traditional cast iron components.
Transition from military to commercial
How do we take these lessons learned in the military and carry over to success in the commercial market? Bulk haulers include trucks carrying liquids, raw food, and oil and water in the energy business. The owners and the fleet managers are aware of the cost per pound of the truck and the payload, and as such tend to be early adopters of new technologies because the payback is immediately measurable with each shipment of goods. With added equipment weight from technologies to handle reduced stopping distance and emissions, on top of rising fuel costs, bulk hauler manufacturers and owners are hungrier than ever to reduce the weight of the truck.
A recent application in military truck light weighting was engineered by AxleTech International. AxleTech designed and developed a steering knuckle for a tactical truck. This knuckle, cast using high strength 206 aluminum by Eck Industries of Manitowoc, WI, delivered 60 lbs. of weight savings per axle from the ductile iron design.
Capitalizing on 206 aluminum depends on the manufacturer. If the focus is on the rotational mass, program managers will specify the forged aluminum wheels and aluminum hubs. 206 has outperformed other cast aluminums for brake calipers, and is much lower weight than iron, and much lower cost than billet aluminum machining. Non-safety critical applications, such as driveline components, transfer cases, power take-offs (PTOs), and differential cases can be converted to 206 aluminum. In one application, a ductile iron differential case and carrier were converted to 206 aluminum delivering a savings of 115 lbs. In a large industrial truck, a single transmission case conversion from iron delivered over 200 lbs. of savings.
Challenges and objections to overcome
The first hurdle is to convince the decision maker—whether it is the design engineer, the program manager, the buyer or the customer—that something needs to be done to make the vehicle more efficient. The conversion from a high density material like ductile iron to a low density material like 206 aluminum should take package space, material performance and cost into consideration. Because ductile iron is stiffer than 206 aluminum, the critical cross sections need to become thicker, which means the component will be larger and may require more package space.
There are two ductile iron alloys common to the truck market, designated as 80/55/6 and 65/45/12 [measurements are: tensile strength / yield strength / elongation (%E)]. 206 aluminum is available in two tempers: 206-T4 is 55/36/10 and 206-T7 is 58/48/5. Compared to ductile iron, the tensile strength, yield strength and elongation are relatively close, yet the aluminum is 2.5 times lower in density. With reduced stiffness, the 206 aluminum component needs to be enlarged, yet is often 50% lighter than the original iron design.
The fatigue performance of a casting is another key metric in terms of mechanical properties. For aluminum castings, fatigue performance is a result of the soundness of a casting—usually a result of how well the design engineer collaborates with the foundry. It’s critical for the foundry to provide advice on the features and geometry as a function of castabilty. Likewise, knowing machine datums and areas of high stress, the foundry can place the gates and risers in locations that will not affect the performance of a casting.
Even with the considerable reduction in weight, aluminum components cost more. With castings, there may be opportunities to combine multiple components into one high strength aluminum casting, thereby lowering the overall cost by reducing the number of parts to track, and multiple tools and weld fixtures. In addition, a casting will often deliver a more reliable part consistently, reducing warranty claims. A typical conversion from ductile iron to 206 aluminum may cost $3-5 per pound saved.
Other common aluminum alloys can be suitable where stresses are lower or for smaller vehicles. Alloys like A356 are widely used in automotive designs for knuckles, control arms and differential cases. With typical mechanical properties of 37/27/7, the strength is sufficient for many applications. Where long-term appearance is critical, such as decorative trim, handles or mirror mounts, an alloy like 535 has an excellent polished appearance and is easily anodized in a range of colors.
While the on- and off-highway vehicle markets continue to strive for more efficiency amidst the challenges of government regulation requirements, long-term investments at higher up-front costs may prove to be one of the only solutions available for OEMs.