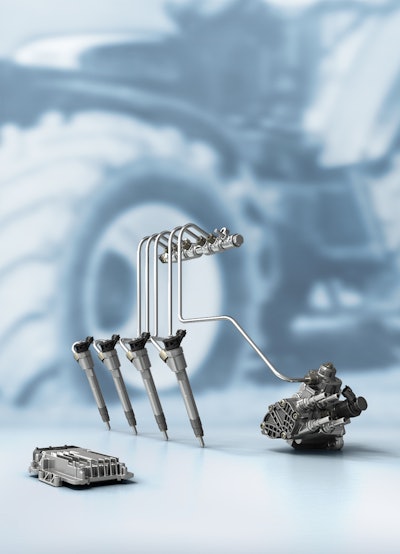
In the future, hybrid vehicles will become much more widespread, and Bosch is bringing electric drives to off-highway applications. The robust systems that recover energy from lifting movements are one example. Such systems will in the future make it possible to use hybrid excavators equipped with energy recovery systems on building sites. Moreover, this new technology can be used for engine downsizing and downspeeding purposes. This, in turn, could result in fuel savings of up to 40%.
Hybridizing heavy commercial vehicles significantly increases their efficiency, as fuel is the biggest cost factor for heavy machinery. At the same time, future emissions standards encourage the use of the new hybrid technology: thanks to lower fuel consumption, CO2 emissions will also be reduced. With a power rating of 65 kW, the new drive offers no loss in performance. In short bursts, up to 120 kW and a maximum torque of 1,000 Nm can be delivered.
With its new common rail system, Bosch is bringing a technology to the off-highway segment that has been tried and tested in road traffic. The high quality of its fuel injection systems helps make engines robust enough for the challenging conditions of off-highway applications.
A symbol of quality and efficiency, the CRS2-18-OHW system is suitable for small and medium-sized machines. While it is based on the CRS-16 system that is featured in millions of passenger vehicles, it operates at a much higher pressure of 1,800 bar. In addition, the CRS2’s injectors enable higher dynamics in controlling the nozzle needle. This, in turn, makes the intervals between injections especially short and the engine more flexible. With optimized combustion, emissions and fuel consumption can be reduced. The CRS2-20-OHW, which is currently in development, goes one step further. It is scheduled to start series production in 2014 and will operate at a pressure of 2,000 bar.
The CRSN3-25: equipped with new injectors and easy to install
CRSN3-25 is designed for heavy machinery. Here, too, Bosch has brought its high technology expertise from the commercial vehicle segment to off-highway applications. The CRSN3-25 is the newest product to be added to the common rail family, which was launched in 1999 and has since seen more than ten million systems produced. The injectors now operate with an injection pressure of up to 2,500 bar. Its parts, including the control valve, are subjected to rail pressure. This prevents seepage between the low- and high-pressure ranges. The system, which was further developed with changing requirements in mind, is compatible with existing engines and can be installed in engines of the previous generation. The CRSN3-25’s higher pressures also help reduce fuel consumption and emissions.
Bosch also offers products beyond the engine block that will make it possible to meet future emissions standards, such as Tier 4 Final and Stage IV. Exhaust gas treatment systems and sensors help reduce pollutant emissions and optimize fuel consumption. To this end, the reliable and highly precise sensors deliver information from the powertrain and exhaust system. The Departronic 2 uses this information for the targeted injection of diesel fuel into the exhaust-gas flow. This enables the closed particulate filter to regenerate in a controlled manner and at regular intervals. The new Denoxtronic 6.5 also helps reduce emissions significantly. Here, AdBlue (DEF) – a solution of 32.5 percent urea in water – is injected into the exhaust gas flow. The system reduces NOx emissions by up to 95% and fuel consumption by up to 5%. Thanks to its flexible modular system, the new generation of Denoxtronic can be easily installed into a range of engines. As a result, it can be adapted to many different markets, as it is capable of meeting varying market and installation requirements.
Bosch Emission Systems GmbH (BESG), a Bosch subsidiary, completes the product offer. The company, which is the Bosch Group’s systems integrator, puts the complete exhaust-gas treatment system together. BESG has developed a modular system for exhaust-gas treatment systems that makes it possible to adapt a system’s components to the requirements of different applications. For instance, the company has come up with a retrofit solution that makes it possible to install exhaust gas treatment systems in used construction machinery, where space for such systems was not initially foreseen. This keeps development, tooling, and validation costs down. Moreover, the Bosch subsidiary offers a complete service package from a single source: BESG combines individual components into a single system that is perfectly suited to a specific application; it then assesses the system on a regular basis with state-of-the-art diagnostics. In addition to highly efficient exhaust gas treatment systems, the service provider can also adapt its modules to suit vehicles up to 5,000 kW.