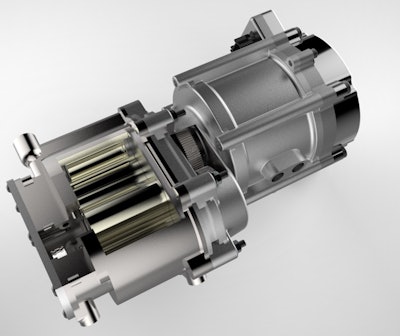
Power management company Eaton has announced it is contributing several components to truck manufacturers participating in the U.S. Department of Energy’s (DOE) SuperTruck II program.
SuperTruck II is a partnership between the DOE, truck manufacturers and equipment suppliers seeking to improve freight efficiency more than 100% over an equivalent 2009 model, and improve engine brake thermal efficiency performance by 55%. The $100 million program is funded by the Vehicle Technologies Office of the U.S. DOE and industry partners.
Eaton is supplying a number of leading-edge technologies that improve fuel economy and reduce emissions to Original Equipment Manufacturer (OEM) teams. These include a high-efficiency transmission that achieves additional fuel savings by enabling engine-off coasting and waste heat recovery; a 48V mild hybrid electrically regenerative accessory drive that charges the vehicle’s batteries, efficiently runs the air conditioner and other accessories, and replaces the alternator in linehaul commercial vehicles; and precise exhaust gas recirculation controllers that enable simultaneous fuel and emissions reductions. The Eaton 48V mild hybrid accessory drive captures energy while driving and is used to keep the sleeper cab comfortable overnight without idling the engine.
“This is a great opportunity for Eaton technologies to contribute to a program focused on improving the efficiency of commercial vehicles,” says Dr. Mihai Dorobantu, Director, Technology Planning and Government Affairs, Eaton’s Vehicle Group. “We’re excited to work with several OEMs involved in SuperTruck II as we strive for a common goal of cleaner, more fuel-efficient commercial vehicles.”
SuperTruck II is a continuation of the DOE’s SuperTruck initiative, which launched in 2010 with the goal to improve heavy-duty truck freight efficiency by 50%. The long-term objective of the project is to develop technology that can lead to cleaner, more efficient heavy-duty trucks, which haul 80% of goods in the United States and use about 28 billion gallons of fuel per year, accounting for around 22% of total transportation energy usage.
In addition to the components Eaton is supplying to the SuperTruck teams, it offers several other technologies that help truck manufacturers achieve stringent upcoming fuel economy and emissions regulations.
“Since 2008, Eaton’s Vehicle Group has been laser-focused on reducing emissions and fuel consumption,” says Dorobantu. “We have—and continue to develop—technologies that reduce NOx emissions and improve the overall fuel economy of internal combustion diesel engines, as well technologies for electric, hybrid and fuel cell commercial vehicles.”
Several products take advantage of Eaton’s modular variable valve actuation technology, which allows OEMs to choose the technologies they want to use based on their needs.
Examples of what Eaton’s Vehicle Group offers include diesel cylinder deactivation (CDA) and variable valve actuation (VVA) technologies. Both technologies can be used to reduce fuel consumption between 5 and 25%, increase the rate of aftertreatment warmup and maintain higher temperatures during load operation. CDA and VVA technologies can also be used at road loads to achieve active diesel particulate (DPF) regenerations without requiring the traditional method of dosing the diesel oxidation catalyst.
Eaton’s CDA technology can operate at up to 3-4 bar BMEP at all speeds, which reduces emissions by improving aftertreatment thermal management while providing better fuel economy. Similarly, intake valve modulation can be used at higher loads to enable Miller cycle operation to improve engine fuel efficiency.
Another technology to help on the path to regulation compliance is Eaton’s TVS EGR pump, which is designed to save fuel while meeting new global emission regulations.
Eaton’s positive-displacement TVS EGR pump enables the use of a high-efficiency turbomachinery to lower engine pumping losses and increase fuel economy. The TVS EGR pump is driven by a 48-volt electric motor, making its operation completely independent from engine speed and significantly more controllable than competitive pumpless EGR systems.
Additionally, Eaton’s new engine decompression brake can help OEMs with regulatory compliance. Fuel economy and emissions regulations are driving engine downsizing and down speeding in commercial vehicles, which is resulting in the need for higher braking efficiency to maintain braking effectiveness at lower speeds.
Other variable valvetrain functions include early exhaust valve opening (EEVO) and internal exhaust gas recirculation (iEGR), which help heat the exhaust for improved catalyst efficiency and improved emissions.
Eaton’s hydraulic lash adjuster (HLA) technology optimizes the valvetrain performance by providing precise valve seating over the life of the vehicle. Other benefits include noise reduction and service elimination for manual valvetrain lash settings.