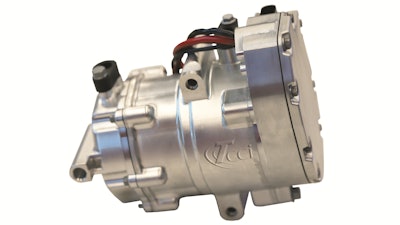
Earlier this year, I spoke at a conference about electric refrigerant compressor selection and integration for heavy-duty and off-road applications, and was impressed by the level of enthusiasm for the topic. It is clear there is great demand for electric vehicles in the off-road segment and specifically for construction, agriculture and mining (CAM) equipment.
Evolving regulations are leading many to embrace electric and hybrid vehicles. Several governments in Europe, for example, are moving toward outright bans on diesel engines—in some instances as soon as 2025—meaning construction equipment will have to be diesel fuel-free. It is not only regulators who are leading the push toward electric vehicles. Because these vehicles are showing improved efficiency, comfort and lower total cost of operation, the biggest private-sector manufacturers are introducing electric wheel loaders, dozers, excavators and more. Although EVs make up only 15% of construction, agriculture and mining vehicles sold today, IDTechEx expects that share to become higher than 50% by 2029.
Many of the same components are used for an electric vehicle, except that an electric compressor will be needed. In fact, even non-electric vehicles are using Auxiliary Power Units and electric compressors for an alternate source of heat and A/C instead of idling a diesel engine. As demand for electric compressors grow, I have found that many people reach the conclusion they need an electric compressor, but do not know how to choose the right one. There is a lot to consider when selecting and integrating an electric compressor, such as the necessary performance, displacement and voltage.
READ MORE: Alternatively-Powered Vehicles Accounted for 15% of EU Bus Market in 2019
Compressor Sizing
Compressor performance and sizing is a good place to start when considering the characteristics of electric compressors. I will first note that electric compressor and belt-driven compressor displacement cannot be compared.
Characteristics to help frame the issue include:
Operating Speed
Belt-driven Fixed Piston
- Ratio of engine speed (depends on driving condition)
- Idle ≈ 1,000 rpm
- Cruising ≈ 2,500 rpm
Electric-driven Scroll
- Chosen by vehicle controls (independent of driving condition)
- Idle: 1,000 -5000+ rpm
- Cruising: 1,000-5,000+ rpm
Volumetric Efficiency (effective displacement %)
Belt-driven Fixed Piston
- 1000 rpm ≈ 75%*
- 2500 rpm ≈ 65%*
- 5000 rpm ≈ 45%*
Electric-driven Scroll
- 1000 rpm ≈ 86%*
- 2500 rpm ≈ 87%*
- 5000 rpm ≈ 89%*
Performance at Idle per cc of Compressor Displacement
Belt-driven Fixed Piston
- 100% (1000 rpm)
Electric-driven Scroll
- 115 ~ 590% (1000 ~ 5000 rpm)
*These numbers are just trends for discussion. Operating conditions have a large impact on actual performance.
A scroll design makes for a much smoother and quieter ride. It has higher efficiency and coefficient of performance (COP) without sacrificing performance, which translates into less energy use and increased battery operating time or driving range.
The cool-down behaviors of belt-driven and electric compressors differ. Since the electric compressor speed is not tied to engine speed, it can provide maximum performance at any engine speed, unlike the belt-driven compressor. The capacity can be controlled to match the cooling demand, providing optimum comfort while maintaining energy efficiency. The design allows the compressor and AC system to be operational even when the engine is not running — saving fuel, reducing emissions and providing operator comfort.
Operating Voltage
The operating voltage of the compressor is another key factor in performance. The higher the voltage, the more power that will be available to the compressor and the better it will perform. For a given cooling load, the current in the compressor is the electrical power required to operate divided by the operating voltage. As voltage decreases, the current increases. Current is the limiting factor for compressor cost, since doubling current quadruples the size of the wires and electronics needed to prevent overheating. As the voltage goes up, the current can go down and this allows for an increase in the displacement of your scroll. Running a large displacement scroll at a low voltage results in a very high current, which is simply not practical or feasible depending on the electronic design.
Common nominal voltage architectures include:
- 24-48V: 48V is a practical limit to avoid high voltage electrical safety requirements (peak voltages <60V).
- 300V: Common system voltage in automotive; can take advantage of economies of scale
- 600V: Higher power and faster charging is good for heavy duty and medium duty. It is low scale so far but increasing in adoption
While it is technically possible to make a 12V compressor, it is going to have extremely low performance because air conditioning requires a lot of power compared to most electrical loads. Stepping up to 24V greatly increases the practical power limit and therefore the system performance.
An overview of electrical system constraints which should be taken into consideration when selecting the right electric compressor for an application.T/CCI Manufacturing
For an electric vehicle, as much as 400V or 800V may be necessary to provide the power for the powertrain and users will want the compressor to run at the same voltage for lower total system cost. This is convenient, because higher voltages are good for driving larger compressors and vehicles with higher voltages tend to require more battery and cabin cooling.
We expect to see ever-increasing voltages in the next 5 years. The numbers are all over the map today, but standardized voltage and general compressor requirements should start to emerge. The industry will have greater clarity from the manufacturing and design side and, once that happens, we foresee focused efforts and major advancements in the technology.
Refrigerant System Integration
Refrigerant system integration is another key factor in performance. Key considerations are the refrigerant system design, operating conditions and peak cooling loads. The refrigerant system could be used for cabin cooling, battery cooling and power electronics (electric drive unit) cooling. Although each of those systems need cooling, the peak loads often do not occur simultaneously. Moreover, the cooling loads cannot be simply added together because the operating temperatures of the various heat loads (and therefore the refrigerant temperature, pressure and density) are not the same. Since compressor performance is highly dependent on compressor inlet refrigerant density, the true operating conditions must be calculated to size the compressor properly. Heat pump operation is another key factor to consider. Heat pump operating conditions can create very low refrigerant pressure and density, reducing performance greatly. Waste heat recovery and supplemental heating improve performance but increase system complexity.
Conclusion
Emissions and electrification are the two global trends that are going to affect all regions of the world, so the shift toward hybridization and electric vehicles is only increasing. With this shift, accessory components—especially compressors—need to support the new power systems. With increased adoption of electric motors across a variety of industries, the requisite technologies for electric compressors are becoming better and more affordable.
Innovative electric designs allow the compressor and A/C to be operational even when the engine is not running—saving fuel and providing operator comfort. For fully electric vehicles, electric compressors are required to enable cabin comfort and to keep the electric powertrain from overheating. By utilizing a variable speed scroll compressor, the refrigerant system capacity can be matched to vehicle cooling demand, maximizing system efficiency and therefore battery run time.
Whereas many people are confident about navigating their needs for a traditional compressor, I find that customers have many questions regarding the specifications of electric compressors. Those who understand their needs and the influence to the compressor will be prepared to embrace the change. Erik Huyghe is the Director of Advanced Engineering for T/CCI Manufacturing.T/CCI Manufacturing
Erik Huyghe is the Director of Advanced Engineering for T/CCI Manufacturing, a world leader in compressor technology including electric, reciprocating, swash plate, wobble plate and variable compressor designs.