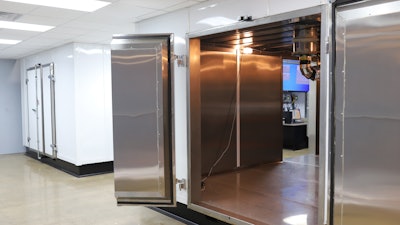
Wind tunnels have a long history in the testing of vehicles and vehicle components, but what if there is a better way?
Dual test benches have emerged as an appealing alternative to the wind tunnel. This setup is capable of precisely replicating real-world conditions in a controlled environment without the power requirements, overhead, and risk associated with wind tunnels.
They help develop new products and optimize customer systems for efficiency, durability, quality, and cost-effectiveness at a fraction of the cost of traditional wind-tunnel testing or other testing solutions.
READ MORE: T/CCI Opens New Advanced Testing Center
Advantages to using dual test benches
There are many benefits to test benches for determining how something will perform in the real-world.
Cost-Effective
With a price tag of roughly $15-30 million to build or $2,000-3,000 per hour to rent, wind tunnels are extremely resource-intensive. Investing in a system bench is significantly more cost-effective than wind tunnels and over-the-road testing, where the vehicles themselves cost millions of dollars.
Test benches can run 24 hours a day for a fraction of the cost of a wind tunnel. This allows the team to provide solutions for specific customer applications, even on limited-quantity partnerships.
With a dual system bench setup it is possible to test key measurables in a wide variety of conditions. This allows a user to understand where potential problems could arise and make adjustments to designs before the first product reaches the customer—again saving cost.
The “heavy lifting” can be done on the system benches. This leaves only final testing in the tunnel prior to the over-the-road portion of the vehicle validation process.
Versatile
An advanced testing center is capable of a multitude of tests that never would have been done in a wind tunnel. Wind tunnels are appropriate for vehicle testing, for instance, but do not always meet the testing needs of HVAC, refrigeration, and compressors.
Dual system benches are capable of testing all components of heating systems, as well as air conditioning and battery cooling. Battery cooling is a big need, particularly when it comes to electrification of off-highway vehicles. These benches are not your average walk-in chiller units—it is possible to test in climate conditions ranging from -40-120 F (-40-48.9 C). Test benches also have vibration and thermal imaging capabilities to evaluate potential hot spots in condensers.
Flexible
Using a wind tunnel, you have to take receipt of a vehicle, spend a week installing an instrument, and then test the entire vehicle.
If a vehicle is too large to fit in, or it is halfway around the world, you do not want to have to ship it to test in a wind tunnel. With dual system benches, if a customer wants testing done, they can send the system by air freight and it can be set up and evaluated.
The system benches have a very sophisticated data logger, allowing you to simulate a certain condition. The flexibility is far beyond any other methods.
Safe
With wind tunnels, you are dealing with experimental vehicles that are full of fuel. This requires two people in the area at all times. Dual system benches do not come with the same concerns.
Wind tunnels still have their place, but they are costly and take time to set up. Vehicles are at a premium since they are experimental, expensive to build, and costly to ship—especially off-highway equipment.
Dual system benches have emerged as an efficient and versatile alternative to wind tunnels and other testing solutions.
By reducing the time that vehicles need to spend in a tunnel and road testing, these labs allow users to more quickly and economically find problems, make changes, and bring products to market. These benefits are immediately shared by customers.
This article was written and contributed by Richard Demirjian, President of T/CCI Manufacturing.
About the author
Richard Demirjian is the President of T/CCI Manufacturing, a supplier of compressor technology to the trucking, off-highway, specialty vehicle and transport refrigeration markets with a global footprint that includes manufacturing operations in China, Argentina, India and the United States.