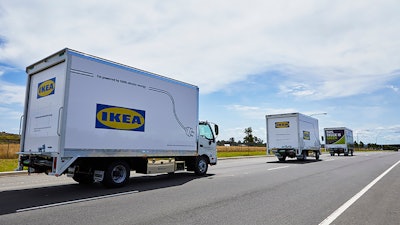
With new and existing OEMs preparing to produce electric powertrains for Class 3-8 vehicles, one goal is common: delivering efficiency per mile with reliability for the application needs of the market. This requires proper integration of various components and systems, including fluid conveyance systems.
As such, Stark Manufacturing will partner with customers’ design engineering groups to equip OE manufacturing facilities with a fully assembled fluid conveyance line package.
These line kits can be incorporated directly into an OEM’s production lines. They will include supplying an entire battery-electric vehicle (BEV) powertrain and HVAC line kit, including thermal management lines for battery/motor/electronics and AC assemblies for cabin/electronics. Doing so offers OEMs a total cost savings by consolidating order processing, shipping/packaging, logistics, and improving vehicle assembly efficiency.
The strategy is particularly attractive to the many BEV production startup companies, which typically have strong knowledge in technology behind powertrain electrification, but sometimes lesser experience in lower volume manufacturing. Therefore, startup production lines need all the scaling benefits available to lower costs.
Packaged kits customized for each vehicle model/configuration allows Stark to achieve this. The kits, including hard lines, hose assemblies, machined fittings, and fastening hardware, are staged at Stark’s Manufacturing facility and shipped ready for installation at the customer’s facility. Packaging may be expendable or returnable, based on the customer’s logistics needs. These kits reduce the need for dedicated warehouse space, reduce the production resources needed for assembly, minimize packaging, and facilitate the use of lean inventory control methods, including Kanbans and JIT shipments.
Stark Manufacturing
Collaboration aids integration
Before release to production, Stark’s application engineering team collaborates with customers’ battery thermal management design team to ensure system robustness. Having experience designing components for commercial vehicles’ useful life often exceeding 1,000,000 mi. (1,609,344 km) and extreme environmental conditions, Stark engineers consider durability, serviceability, and cost effectiveness. This is especially critical since data and system maturity is low with battery electric commercial vehicles, while uptime requirements are still a leading market benchmark.
Stark’s digitized production lines allow for in-house machined fittings to +/- 0.005 in. (0.0127 cm), bent aluminum or steel tubing to accommodate unique packaging and routing challenges, including a variety of common and exotic end-form geometries as well as braze or weld joints where needed. Quality verification includes 3D scanning for precision when hard fixturing is not feasible due to cost or complexity, and each assembly is leak tested using helium mass spectrometry. Stark’s aluminum tube assemblies have the highest useful life, offer not only flexibility and durability, but are lightweight, economical, corrosion resistant, and environmentally friendly. Combined in a kit with raw material sourced and produced within the U.S., OE’s can realize cost savings from consolidated orders, lower shipping/packaging, mitigated risks on logistics, and vehicle assembly efficiency and accuracy.