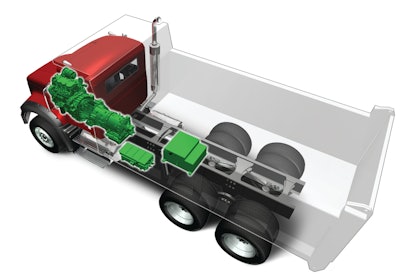
With the term hybrid being thrown around so much these days as manufacturers, and the global population, look for ways to reduce their carbon footprint, there can be some confusion as to what the word hybrid actually means. Tom DeCoster, Business Development Manager of Hybrid Drive Systems at Parker Hannifin Corp., Cleveland, OH (company information, 10055900) says when most people think of hybrids their minds automatically go to electric automobile applications.
However, a vehicle does not have to run on electricity in order to be considered a hybrid. The textbook definition of a hybrid simply states that it is a vehicle which uses two or more sources of power. There are many types of technology combinations which constitute a hybrid besides the more traditionally thought of engine and electric battery power combination.
“In some cases we may be operating with electric motors as a prime mover, in other cases it may be diesel engines, natural gas, or other energy sources,” says Steve Zumbusch, Director of Advanced Platform Innovations at Eaton, Eden Prairie, MN (company information, 10055335). “But 'hybrid' reflects the ability to manage power through the multiple sources.”
Hydraulic hybrids, for example, have become more prevalent within recent years due to the amount of energy they can capture and reuse. Hydraulic hybrids are especially applicable for use in heavier duty applications. “[If] the vehicle is very heavy, that’s where hydraulics shine,” explains DeCoster. “They can capture a huge amount of energy in a very short period of time, and then they can use that energy very efficiently and very quickly."
“So far all [people have] been exposed to is alternative fuels or electric hybrid,” he adds. “Here’s another technology that’s offering huge advantages and benefits, and will become more common as time goes on.”
The storing and reusing of energy is yet another way the industry defines hybrid. “Hybrid technology in general is really geared towards taking wasted energy and converting it to energy that can be used,” says Tim Wells, Product Manager at BAE Systems, Endicott, NY (company information, 10314740).
Because the use and type of hybrid system is dependent upon a vehicle’s duty cycle and the application in which it will be used , there are a wide variety of hybrid systems available in the market.
Electric hybrid drive system
The HybriDrive parallel hybrid system from BAE Systems (BAE) captures energy generated from braking events and transforms it into electrical energy that is stored in batteries and used when necessary to supplement engine power. “Energy that would go to waste is being used in lieu of fuel that would be consumed,” says Wells. Using the stored electrical energy for vehicle acceleration or when the engine needs to work hard, such as for climbing a hill, keeps the engine running at its most efficient point for maximum fuel efficiency.
Depending on the application in which the parallel hybrid system is being used, it can offer up to a 30% improvement in fuel economy. Wells notes that HybriDrive parallel system is best suited for vehicles which operate at slower speeds, are known for using a lot of fuel, and make frequent starts and stops.
In addition to the parallel system, BAE also has a series version of HybriDrive which has been in use in the transit bus market over the past 10 years (see sidebar, pg. xx to learn more about the differences between parallel and series hybrids). In the series version the vehicle’s engine runs a generator to provide electrical energy. Electricity generated by the engine is fed to the batteries and power electronics, enabling the vehicle to be driven at all times by an electric motor. Use of the series hybrid system on transit buses has demonstrated a 50% improvement in fuel economy. This is due in part to having electrified all the normally belt-driven accessories, adding the option of turning the engine off at various times and moving the vehicle.
Along with the fuel savings it provides, HybriDrive also provides noise reduction benefits. Because the engine is run at its most efficient point it is therefore not revving up, causing excess noise. Emissions are reduced as well due to the engine’s more efficient operation and lower fuel consumption. Simply put, “If you burn less fuel, you create [fewer] emissions,” says Wells.
Because of the speed and frequency with which the hybrid system communicates with an engine, BAE works very closely with engine manufacturers during the vehicle integration process. “We always have to know what [the engine is] doing and what it wants to do, and we may want to change that based on our control technology,” says Wells. In most cases, the engine manufacturer will grant BAE approval to change aspects of what the engine might normally do in various situations so the engine can better accommodate the hybrid electric control technology. Having the ability to adjust certain parameters on the engine enables BAE’s control technology to keep the engine at a lower idle at times when it might want to rev up, such as during vehicle acceleration, and instead use the supplemental electrical power from the hybrid system to operate the vehicle in its usual manner without having the engine do all of the work.
Collaboration with the vehicle OEM is integral, as well. BAE works closely with the vehicle manufacturer to ensure all components and systems will work together properly and efficiently. Working with the OEM also guarantees components of the hybrid system are put in the best and most economical place to match the needs of the end user.
OEM collaboration also assures integrating a hybrid system like BAE’s will be cost effective to the end user. Wells says the system does add weight to a vehicle—between 800 and 900 pounds for the parallel version—making it important to know the duty cycle of the vehicle and whether the benefits of using the system, and the added weight it brings, will actually save customers money in the end. “The fuel economy benefits though do take into account that added weight,” says Wells.
According to Wells, one of the biggest challenges—for all industries—is how to incorporate new and advancing technologies such as HybriDrive in a cost-effective and weight-optimized manner. When BAE first introduced its series hybrid, the system used lead acid batteries which added approximately 4,000 pounds of weight to the vehicle. About four years ago Wells says the company switched to lithium ion batteries which brought the weight of the system down to 800 pounds. In addition to reducing the weight of the system, using lithium ion batteries brought about a change in the control technology BAE could utilize. “It added a lot of additional features that we have now like engine-off motoring and electrifying more subsystems,” says Wells.
As BAE continues to advance and develop its hybrid system further, reducing weight will continue to be an area for further optimization. Wells notes this will continue to be a challenge because not only do customers want the system to weigh less, but they also need it to be ruggedly constructed in order to survive—for at least 10 or 12 years—in heavy-duty applications.
Greater vehicle electrification is also a development goal for BAE. One way the company will accomplish this will be to replace subsystems currently driven mechanically by belts with electric driven motors. “We also want to slowly but surely increase engine-off motoring so that we do more and more things with the engine off and use the electrical energy instead,” Wells says.
If more electrical energy can be stored and used on the vehicle, the less the engine will have to be used, and thus less fuel will be consumed and fewer emissions released, and eventually it can get to a point where the engine will only be used when it makes sense to do so, such as during very high power demand tasks. “These are the types of things we are doing some of now, but that’s only going to expand more and more,” says Wells.
Hydrostatic regenerative braking
Bosch Rexroth’s, Charlotte, NC (company information, 10055110) hydrostatic regenerative braking system (HRB) is a hydraulic hybrid technology which captures braking energy that would otherwise go to waste and reuses it to help drive the vehicle. The system provides supplemental power to the engine so that it does not have to work as hard to perform certain tasks, leading to reduced fuel consumption.
As the vehicle begins to decelerate, the HRB’s axial piston unit captures kinetic energy created by the braking event and converts it into hydraulic energy. The energy is stored in high pressure accumulators until it is needed for vehicle acceleration. Once the vehicle accelerates, the hydraulic fluid flows back through the axial piston unit, which now acts as a motor to deliver energy to the vehicle’s mechanical drivetrain and supplement engine power.
Hydraulic technology was chosen because it is robust and durable, as well as a known technology. OEMs, end users and vehicle maintenance professionals have been working with hydraulics for years, so they are familiar with how it operates and how to fix it if necessary. Tom Garbacz, Director, Hybrids and Systems at Bosch Rexroth, notes this familiarity with the technology is an important aspect to consider when developing a hybrid system. “I think that [familiarity] plays a big role in the acceptance of the technology compared to an electric hybrid where [the technology] could be really foreign to some of the OEMs or service organizations,” he says.
The goal of HRB is to quickly store and use energy in an effort to reduce the workload put on the engine and save as much fuel as possible. Because of this, systems like HRB are best suited for heavy commercial vehicles which make frequent starts and stops throughout the day so that there are numerous braking events from which to collect usable energy. Currently Bosch Rexroth is focusing its efforts on implementing this technology on refuse trucks, but is also looking at additional on- and off-road applications.
Only available as a parallel system at the moment, HRB is an additional system integrated into the vehicle’s driveline after the transmission. Garbacz says parallel hybrid architectures such as HRB’s can be beneficial due to the fact that they can be deactivated without losing the ability to still drive the vehicle. “If the system was to go down, you could still drive and use the truck,” he says, which is especially useful for commercial fleets that cannot afford to have unscheduled downtime.
A potential challenge with HRB being a parallel system is the additional weight it can add to a vehicle, though it is something Bosch continually works to optimize. Garbacz notes that the added weight is taken into account when designing and integrating the system for a specific application, and built into the total cost of ownership of a vehicle utilizing HRB. “The HRB technology is very duty cycle dependent,” says Garbacz. “In applications where numerous start/stops at low speeds are present, the improved fuel efficiency gains make up for the slightly increased weight.”
Hydraulic hybrid system
First launched at bauma 2013 (learn more, 10884362), Spicer PowerBoost is a hydraulic hybrid system from Dana Holding Corp., Maumee, OH, which captures and reuses otherwise wasted energy from the drivetrain and working hydraulics to help power a vehicle. The system is an add-on solution that is compatible with the company’s existing transmission portfolio.
Spicer PowerBoost (PowerBoost) captures kinetic energy from the drivetrain, particularly during braking and working events—such as shuttling operations. “When the vehicle is accelerating and decelerating severely, there’s a big opportunity to capture energy otherwise wasted,” says Ettore Cosoli, Head of Off-Highway and Vocational Vehicles, Hybrid in the Advanced Engineering and Innovation Group at Dana (company information, 10056523). The captured energy is then stored in an accumulator for use when additional power is needed, such as when accelerating from a stop, lifting a load or driving into a pile of dirt.
As a supplemental power source to the engine, the hybrid system can offer fuel savings between 20 and 40%. Cosoli says the amount of fuel saved is dependent upon the application and duty cycle of a vehicle. Heavy-duty equipment with frequent, intensive power demand fluctuation, and short and medium Y cycles will benefit most from using PowerBoost. Currently the system is being integrated into off-highway equipment—mostly construction and material handling vehicles at the moment—with additional applications, including refuse trucks, planned for the future.
According to Cosoli, the core of the hybrid system is the mindware embedded into the Spicer PowerBoost Hub which is a mechantronic unit that acts as an energy management system, determining when, where and how energy will be captured, stored and used. Via the advanced control system, energy is directed to and from pumps, motors and accumulators in the driveline and used depending on specific vehicle needs. “[It is capable of deciding] how to modulate the power absorbed by the diesel or by the accumulators in order to optimize a specific target, for example fuel savings or productivity,” says Cosoli.
For productivity improvements, the hybrid system injects stored energy from the accumulators into the driveline so that the vehicle’s traction is actually being powered by the stored energy instead of the engine. This enables the engine’s power to be fully devoted to other vehicle tasks, such as moving a bucket of dirt, which Cosoli explains is beneficial to increasing productivity compared to that of a conventional, non-hybrid vehicle.
The PowerBoost system can also be configured to minimize engine idling by shutting off the engine and using energy stored in the accumulator for low-energy operations such as inching or low travel speeds. “When the full power of the diesel engine is not [required]…the system has the ability to buffer energy into the accumulators and then use this extra energy when needed,” notes Cosoli.
With the extra energy PowerBoost provides, the engine can actually be downsized, helping reduce some of the weight and space constraints OEMs may be facing when designing a vehicle, particularly for applications close to the 56 kW threshold. “Compact vehicles below 100 kW could benefit from the potential downsizing of the engine below 56 kW,” Cosoli explains, “and [use] the extra power from the hybrid solution to compensate.”
As Dana continues to further develop and enhance its hybrid technology, it will expand beyond just capturing energy from the driveline. The next stages in the company’s development process will involve capturing energy from a vehicle’s working hydraulics. Once this technology is fleshed out, Dana intends to combine driveline hybridization and hydraulics hybridization into a full vehicle energy management system. In addition to performance and productivity boosts, extra features such as start and stop quiet mode, and hummering mode will be added to the PowerBoost system. Operator assistance features, such as parking assistance, are also in the works.
Hybrid power via regenerative braking
Originally begun as a hybrid technology for the on-highway market, Eaton is now evolving how its Hydraulic Launch Assist (HLA) technology is used in off-highway equipment, as well. “It provided tremendous technology that we’re now in the process of carrying over into these other markets,” says Zumbusch, Director of Advanced Platform Innovations at Eaton.
HLA uses regenerative braking technology to capture, store and reuse otherwise wasted energy released during braking events. As a vehicle begins to brake, the generated kinetic energy drives a pump/motor as a pump, enabling it to transfer hydraulic fluid to a high-pressure accumulator. Nitrogen gas in the accumulator is compressed by the hydraulic, and the system becomes pressurized. For vehicle acceleration, the hydraulic fluid carrying the captured energy is fed out of the accumulator, causing the pump/motor to be driven as a motor which enables it to provide torque to the driveshaft and propel the vehicle forward.
Using the captured braking energy as an additional power source provides fuel efficiency as well as energy efficiency benefits. “We can actually make it selective so that you can shift between Economy Mode and Performance Mode,” notes Zumbusch. He says the main difference between these two modes is how the engine is run. In Economy Mode the engine is kept running at its optimal fuel efficiency point while the energy stored within the accumulator is used to provide the necessary power for completing specific vehicle tasks. Once the accumulator is empty, the engine takes over provision of the power. And it is all done a manner that is relatively transparent to operators, enabling them to continue working without interruption. In addition to fuel efficiency benefits, Economy Mode can help reduce noise levels.
Performance mode, on the other hand, uses both the stored energy and the engine to provide power for vehicle tasks. When the accumulator is empty, the engine is solely responsible for providing power. The main goal of this mode is to improve the productivity of the vehicle, which Zumbusch notes some customers value more than increases in fuel efficiency. He says this is why Eaton built the capabilities to switch between the two modes into its hybrid system.
Dan Koehler, Segment Director for Construction and Material Handling at Eaton, points out that with hydraulic hybrids there is an opportunity to downsize the engine due to the supplemental power the hybrid system provides. The additional power source enables OEMs to install a smaller sized engine without losing productivity. Not only does this help reduce the amount of space needed for the engine, but it also reduces the cost of the engine and its aftertreatment system. “And because we’re running more efficiency, the heat load rejection required is less,” adds Zumbusch. Cooling components such as radiators and fans can now reduce in size, as well. “And when you run with smaller fans, that requires less horsepower to run which means more horsepower leftover for operating the equipment. It has a snowball effect on it that certainly impacts the engines.”
The current hydraulic hybrid system for on-highway vehicles is a parallel system added to the drivetrain of the vehicle. According to Zumbusch, many in the on-highway market were not ready for a fully hydraulic hybrid system as they were used to mechanical transmissions which had a connection between the engine and wheels. “Going to a full hydraulic system wasn’t an easy leap for them,” he says. With a parallel system, operators could get the fuel savings and efficiency benefits of a hybrid, but if necessary, turn the hybrid system off and rely solely on the mechanical system.
However, the next generation of the system has added a series hybrid solution. “Those are the ones that actually have better opportunities for vehicles both on road and off road because it gives us more opportunity to manage the engine power as well,” notes Zumbusch. Because off-highway applications have become comfortable with hydraulics and hydrostatic transmissions over the years, the use of hydraulic energy recovery technologies is as much of an adjustment.
Applications which HLA are best suited for include those with frequent starts and stops, as well as those that have periods of high power and low power usage. A lift truck, for example, may do several lifting operations throughout its workday as opposed to a lot of moving around the work site. In this case, HLA can be designed to capture the energy that would otherwise be released, and wasted, as the truck’s lift moves down. “Duty cycles are everything when it comes to which machines are candidates for getting a lot of improvements in fuel savings versus something else,” says Zumbusch. “When we took a look at taking this technology off-road it was really a study of duty cycles and what types of machines are used in what way, not only in machine type but also by the region that it runs in and the type of work the machine is being tasked with.”
Hydraulic hybrid drive system
Designed for Class 8 refuse trucks, RunWise is Parker Hannifin’s Advanced Series Hydraulic Hybrid system which captures and reuses the energy recovered during braking events. “We can capture approximately 70% of the energy that’s available in a braking event,” says DeCoster. As an advanced series system, RunWise replaces the transmission and controls a vehicle’s engine.
When the brakes are applied, RunWise’s secondary pump/motor mechanism acts as a pump to capture brake energy that is normally dissipated as wasted heat. This energy is stored in the system’s two accumulators and used as necessary to provide power for vehicle acceleration. For vehicle acceleration, the pump/motor mechanism is used as a motor to deliver the stored energy. The vehicle runs completely on the captured and stored energy, enabling the engine to remain at idle until there is a power demand that absolutely requires use of the engine, such as when the accumulators have run out of stored energy.
Once the accumulators are empty, the engine is revved up just enough to power RunWise’s primary pump which then drives the vehicle hydrostatically.
A power drive unit (PDU) replaces the transmission and handles the gear changes of the vehicle. According to DeCoster, RunWise is a three gear system of which the first two are hydrostatic. In first gear—which runs from 0 to 25 mph and is also known as “garbage collection mode,”—all acceleration and braking is completed by the hybrid system’s pump/motors. During this mode the engine is not in any way connected to the rear axle. Second gear—between 20 and 25 mph—the hybrid system’s pump/motors again perform all vehicle acceleration and braking.
When approaching speeds around 42 mph, the system goes into direct drive, also known as third gear. Direct drive is the only time during which the engine is mechanically connected to the rear axle in order to provide power for acceleration and braking. DeCoster explains that “once you get to direct drive it becomes more efficient to run the vehicle in [this mode] than it would in hydrostatic.” Because the first two gears are used when there are a frequent number of stops and starts, there are enough braking events to provide the hybrid system the amount of energy it will need to power the vehicle. Direct drive, on the other hand, is best suited for times when there will be consistent vehicle travel and minimal braking events.
Running the majority of the time on captured and stored energy allows RunWise to provide fuel savings in the range of 35 to 55%. DeCoster notes that the use of stored energy also provides natural productivity gains, between 5 and 15%. Typically with an automatic transmission the power has to run through the transmission and often the torque converters slip. With the hybrid system, however, power can be delivered very quickly to provide slightly faster vehicle acceleration.
Brake maintenance on vehicles equipped with RunWise is essentially minimized due to the hybrid system’s pump/motors performing most of the braking instead of the actual brakes. The only time the friction brake system is used is when an operator has to stop very quickly, when the vehicle is under approximately 2 mph. “So any time from 2 mph to top speed, if you’re applying brakes, you’re primarily using the RunWise system to do the braking,” says DeCoster.
This reduced brake system use means the brakes are being maintained, and replaced, fewer times than on a conventional vehicle. According to DeCoster, instead of replacing the brakes two to four times a year, it is closer to once every seven years, if ever during the entire life of the vehicle. And because there are fewer brake replacements being made, less waste material is added to landfills.
Because RunWise interacts so much with the engine, Parker works closely with the OEM’s engine manufacturer to ensure proper communication and efficiency between the two systems. DeCoster explains that the engine manufacturer provides an engine calibration telling Parker which speed zones within the engine it can and cannot operate so as not to interfere with emissions control technologies. Parker then writes its own calibration that avoids emissions-related zones and instead operates the engine within the most efficient zone that remains. “Our control engineers then take that calibration and work to make the most efficient use of the engine’s power to keep the engine optimized for performance,” he says.
While RunWise is currently designed for use in refuse trucks, there are other applications in which the technology is applicable, and Parker intends to investigate those as it further develops the technology. “Where hydraulic hybrids shine is in a high payload with high start and stop duty cycles,” says DeCoster. “So refuse, transit buses, shuttle buses and delivery vehicles.”
Power inverter for electric drive systems
To help power hybrid electric vehicles, Phoenix International, also known as John Deere Electronic Solutions, Fargo, ND (company information, 10055947), has developed an electric drive system consisting of a power inverter which is closely integrated with a high power electric motor and receives commands from a system controller. The power inverter operates in torque mode for normal driving, speed mode during shift management, or voltage control mode if being used as a generator. Power is delivered to the drivetrain in motoring mode or used to capture braking energy for later use in what’s known as generating mode.
According to David Gordon, Business Development Manager at Phoenix, the inverter (product information, 10635589) is the brains of the electric drive system, managing power flow to and from the electric motor. The inverter reads the position of the electric motor in very high speed control loops and utilizes advanced switching methods to achieve inverter efficiencies of over 98%. Depending on the electric motor used, drive system efficiencies over 90% can be achieved. The inverter also monitors the electric machine for proper operation while constantly communicating with the system controller, which is the brains of the hybrid vehicle.
The system controller commands the electric drive system in the same manner as a traditional drivetrain for power delivery and features electric braking capabilities which can be incorporated with traditional brakes. Gordon notes that the electric drive system may also support peak power delivery where the system controller commands peak output for short durations under special conditions (0 speed start on hill, high negative torque braking situations) while protecting against excessive wear which would sacrifice reliability.
With the electric drive system torque can be delivered instantaneously, providing smooth and quiet acceleration of the vehicle. This helps make for a more comfortable ride for vehicle operators, as well as reduces noise levels on the jobsite which can be especially important if the vehicle is operating in an urban environment.
Gordon notes Phoenix inverters are well suited for high voltage, high torque/power applications. “Knowing that electric drives have been used in locomotives and large mining equipment for many years indicates that the limits are not so much in power but in making the drive systems compact enough that they can fit on the smaller vehicles but still deliver the high power expectations,” says Gordon.
Currently, the company is partnering with Benteler Engineering Services to implement Phoenix’s power inverter as the main power electronics module in refuse vehicles produced by MAN Trucks (learn more, 10815601). Gordon says Phoenix is working with Benteler to install the inverter into the vehicle and tailor it to provide optimal performance in the application.
While hybrid systems can take many forms, their main goal is to capture, store and use otherwise wasted energy. This energy can then be put to work supplementing engine power, enabling the engine to operate more efficiently which leads to a reduction in emissions and fuel consumption.