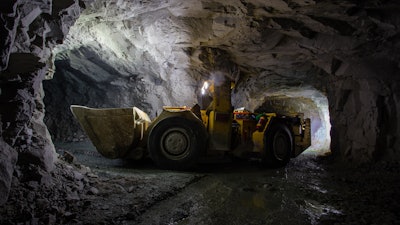
Battery-powered mining vehicles are ideally suited for underground mining. Because they do not emit exhaust gases, they reduce cooling and ventilation requirements, cut greenhouse gas (GHG) emissions and maintenance costs, and improve working conditions.
Almost all underground mine equipment today is diesel powered and creates exhaust fumes. This drives the need for extensive ventilation systems to maintain safety for workers. Moreover, as today’s mine operators are digging as deep as 4 km (13,123.4 ft.) to access ore deposits, these systems become exponentially larger. That makes them more costly to install and run and more energy hungry.
At the same time, the market is changing. Governments are setting environmental targets and consumers are increasingly willing to pay a premium for end products that can demonstrate a lower carbon footprint. That is creating more interest in decarbonizing mines.
Load, haul, and dump (LHD) machines are an excellent opportunity to do this. They represent around 80% of the energy demand for underground mining as they move people and equipment through the mine.
Switching to battery powered vehicles can decarbonize mining and simplify ventilation systems.
This requires batteries with high power and long duration – a duty that was beyond the capabilities of previous technology. However, research and development over the last few years has created a new breed of lithium-ion (Li-ion) batteries with the right level of performance, safety, affordability and reliability.
Saft
Five-year expectation
When operators buy LHD machines, they expect a 5-year life at most due to the tough conditions. Machines need to transport heavy loads 24 hours a day in uneven conditions with moisture, dust and rocks, mechanical shock and vibration.
When it comes to power, operators need battery systems that match the lifetime of the machine. The batteries also need to withstand frequent and deep charge and discharge cycles. They also need to be capable of fast charging to maximize the vehicle’s availability. This means 4 hours of service at a time, matching the half-day shift pattern.
Battery-swapping versus fast charging
Battery-swapping and fast charging emerged as the two options to achieve this. Battery-swapping requires two identical sets of batteries – one powering the vehicle and one on charge. After a 4-hour shift, the spent battery is replaced with a freshly charged one.
The advantage is that this does not need high power charging and can typically be supported by the mine’s existing electrical infrastructure. However, the changeover requires lifting and handling, which creates an extra task.
The other approach is to use a single battery capable of rapid charging within around 10 minutes during pauses, breaks and shift changes. This eliminates the need to switch batteries, making life simpler.
However, fast charging relies on a high-power grid connection and mine operators may need to upgrade their electrical infrastructure or install wayside energy storage, especially for larger fleets that need to charge simultaneously.
Li-ion chemistry for battery swapping
The choice between swapping and fast charging informs which type of battery chemistry to use.
Li-ion is an umbrella term that covers a broad range of electrochemistries. These can be used individually or blended to deliver the required cycle life, calendar life, energy density, fast charging, and safety.
Most Li-ion batteries are made with graphite as the negative electrode and have different materials as the positive electrode, such as lithium nickel-manganese-cobalt oxide (NMC), lithium nickel-cobalt aluminum oxide (NCA) and lithium iron phosphate (LFP).
Of these, NMC and LFP both provide good energy content with sufficient charging performance. This makes either of these ideal for battery swapping.
A new chemistry for fast charging
For fast charging, an attractive alternative has emerged. This is lithium titanate oxide (LTO), which has a positive electrode made from NMC. Instead of graphite, its negative electrode is based on LTO.
This gives LTO batteries a different performance profile. They can accept very high power charging so that charging time can be as little as 10 minutes. They can also support three to five times more charge and discharge cycles than the other types of Li-ion chemistry. This translates into a longer calendar life.
In addition, LTO has extremely high inherent safety as it can withstand electrical abuse such as deep discharge or short circuits, as well as mechanical damage.
Read Saft's white paper on batteries for underground mining.
Battery management
Another important design factor for OEMs is electronic monitoring and control. They need to integrate the vehicle with a battery management system (BMS) that manages performance while protecting safety across the entire system.
A good BMS will also control the charge and discharge of individual cells to maintain a constant temperature. This ensures consistent performance and maximizes battery life. It will also provide feedback on the state of charge (SOC) and state of health (SOH). These are important indicators of battery life, with SOC showing how much longer the operator can run the vehicle during a shift, and SOH being an indicator of the remaining calendar life.
Plug-and-play capability
When it comes to specifying battery systems for vehicles, it makes a lot of sense to use modules. This compares with the alternative approach of asking battery manufacturers to develop tailor-made battery systems for each vehicle.
The big benefit of the modular approach is that OEMs can develop a basic platform for multiple vehicles. They can then add battery modules in series to build strings that deliver the required voltage for each model. This governs the power output. They can then combine these strings in parallel to build the required energy storage capacity and provide the required duration.
The heavy loads at play in underground mining mean that vehicles need to deliver high power. That calls for battery systems rated at 650-850V. While uprating to higher voltages would provide higher power, it would also lead to higher system costs, so it is believed systems will remain below 1,000V for the foreseeable future. Saft
To achieve 4 hours of continuous operation, designers are typically looking for energy storage capacity of 200-250 kWh, although some will need 300 kWh or higher.
This modular approach helps OEMs to control development costs and reduce time to market by reducing the need for type testing. Mindful of this, Saft developed a plug-and-play battery solution available in both NMC and LTO electrochemistries.
A practical comparison
To get a feel for how the modules compare, it is worth looking at two alternative scenarios for a typical LHD vehicle based on battery-swapping and fast-charging. In both scenarios, the vehicle weighs 45 tons unladen and 60 tons fully loaded with a load capacity of 6-8 m3 (7.8-10.5 yd3). To enable a like-for-like comparison, Saft visualized batteries of similar weight (3.5 tons) and volume (4 m3 [5.2 yd3]).
In the battery-swapping scenario, the battery could be based on either NMC or LFP chemistry and would support a 6-hour LHD shift from the size and weight envelope. The two batteries, rated at 650V with 400 Ah capacity, would require a 3-hour charge when swapped off the vehicle. Each would last 2,500 cycles over a total calendar life of 3-5 years.
For fast-charging, a single onboard LTO battery of the same dimensions would be rated at 800V with 250 Ah capacity, delivering 3 hours of operation with a 15-minute ultra-fast charge. Because the chemistry can withstand many more cycles, it would deliver 20,000 cycles, with an expected calendar life of 5-7 years.
In the real world, a vehicle designer could use this approach to meet a customer’s preferences. For instance, lengthening the shift’s duration by increasing the energy storage capacity.
Flexible design
Ultimately, it will be the mine operators who choose whether they prefer battery swapping or fast charging. And their choice may vary depending on the electrical power and space available at each of their sites.
Therefore, it’s important for LHD manufacturers to provide them with the flexibility to choose.
This article was written and contributed by Xavier Iraçabal, Mobility Product Manager from Saft.