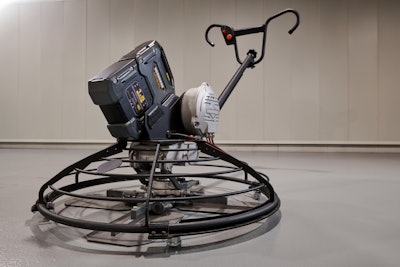
The demand for cordless battery-powered equipment is rising as emissions regulations tighten and gas prices continue to climb. There are several main factors contributing to the increased interest including improved operator experience, noise reduction and new insights unlocked with data captured by the battery.
Why Use Battery Power in Construction Equipment?
Historically, gas and diesel-powered machinery has been the power solution of choice in the construction industry. Recently, there has been a significant shift in interest within the construction sector as lithium-ion battery-powered machinery gains traction across the globe. This increase in demand can be attributed to the benefits that electric power brings within three main categories: noise, vibration and emissions.
Taking the Noise Down with Electric Equipment
The World Health Organization considers noise to be second only to air quality as the largest environmental nuisance, particularly when the exposure is prolonged. Not only this, but continual noise has been shown to impact end-user concentration and make it harder to hear directions or warnings which can lead to more on-site safety incidents. Many construction crews are benefiting from switching to quieter, battery-powered equipment that leads to a more comfortable and safer jobsite environment.In general, electric outdoor power equipment vibrates at a decreased level when compared to gas-powered counterparts. This enables the user to work more comfortably for longer periods of time without sacrificing safety, thus improving productivity.Briggs & Stratton (Vanguard)
Depending on the type of equipment, battery power can create a near silent operating environment. The reduction of noise helps to support the user’s experience by limiting the need for hearing protection while simultaneously reducing the noise impact on the local surroundings.
The lower noise levels of battery-powered equipment also mean work can be performed during off hours in quiet or sensitive environments like areas near hospitals, assisted living facilities or residences. As more major cities adopt noise ordinances, gas-powered equipment is more likely to be prohibited in these areas due to the noise levels associated with such equipment. In these scenarios, crews using electric equipment can be on the job longer and work more efficiently since they are not held to the noise restrictions and quiet hours a municipality may put in place.
Using Battery Power to Help Lower Harsh Vibrations
In addition to the significant reduction in sound pollution when using battery-powered equipment, there is also likely to be a reduction in harsh operation of the equipment. In general, electric outdoor power equipment vibrates at a decreased level when compared to gas-powered counterparts. This enables the user to work more comfortably for longer periods of time without sacrificing safety, thus improving productivity.
When switching to battery power, users can typically enjoy a more comfortable experience because there is less vibration. So, between the lower vibration levels and the reduced noise, OEMs that prioritize electric equipment are going to provide a better, less-taxing user experience for operators. This allows users to work more comfortably for longer stretches of time. All of that adds up and really can boost a construction company’s bottom line.
Using Electrification to Meet Emissions Standards
Globally, the construction industry is responsible for 11% of the energy-related carbon emissions. Battery power is an attractive solution because it creates no emissions at the point-of-use. Not only does electric equipment give OEMs and construction crews tools to meet increasingly strict emissions standards, but it also allows operators to use certain equipment in places where it was not previously possible like indoors and in confined spaces.
Electric battery optionsBriggs & Stratton (Vanguard)
Designing and Testing Batteries for a Construction Environment
Equipment that is used on construction sites must be able to withstand the harsh elements that come hand-in-hand with the industry. For this reason, batteries designed for off-highway use must go through rigorous testing protocols, including impact and vibration, to ensure that the battery performs safely and effectively under demanding construction site conditions.
Vanguard batteries are specifically designed, from the ground up, to be used in commercial applications that have high vibration, impact, temperature shocks and environmental exposure requirements. This level of testing and the way we’ve engineered our batteries to perform productively and safely in harsh environments is what our OEM partners appreciate most.
These batteries are constructed with multiple protective features including an outer metal shell. The electrical components are fully enclosed to protect from impact as well as dust and water entry while still allowing critical venting for the battery cells.
How to Measure a Battery’s Efficiency, Safety
The battery management system (BMS) found in premium Lithium-Ion batteries plays a crucial role in ensuring safe operation of the battery itself, ultimately reducing downtime and boosting productivity for end-users. Integrated into the battery, the BMS can run diagnostics continuously on the internal mechanisms of the pack. Data on different elements can be recorded and relayed to the user including temperature, charging speed and charge status. Combined, the data collected by the BMS can protect the health of the battery and provide meaningful observations around efficiency.
Think of the BMS as the brain that controls all the functions of the battery. A BMS evaluates the battery in relation to the equipment or charger, only allowing the flow of energy when properly connected and when environmental conditions and charge/discharge parameters are met. In basic terms, a BMS governs all the rules and boundaries to ensure a safe, long life for the battery.
With some BMS, thermistors on each cell module constantly monitor individual cell and pack temperatures, and the BMS logic will prevent the battery from exceeding safe limits for charging or discharging. Any irregularities will be automatically adjusted to maintain optimum performance.
By optimizing the charge/discharge rates based on ambient and pack temperature, state-of-charge (SoC) and state-of-health (SoH), the BMS keeps the pack from operating in fringe areas – where Lithium-Ion battery life is most compromised. It is the thoughtful engineering and design principles that mitigate many of the risks that are associated with battery power. This frees the user from having to manually monitor such elements.
While many elements in a Vanguard battery are hidden from view, they are constantly monitoring a multitude of factors to keep the user safe and the battery healthy for a long, reliable life.
Looking Ahead
While there is an obvious trend toward electric solutions, OEMs will need a strong partner to help navigate this huge shift in how the construction industry powers its equipment. Many large OEMs are preparing for a steep rise in the use of electric construction equipment due to the social, environmental, health and safety benefits that come with their use. When it comes time to select a battery to power their solution, they should understand batteries are not just a bundle of cells in an enclosure. OEMs should look for an expert in both the engineering of a battery and the integration of the solution to make the process as simple as possible.
Nick Moore is director of product management, electrification, at Briggs & Stratton.