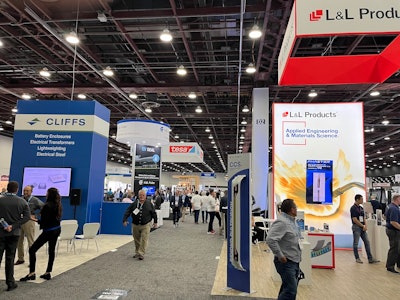
The Battery Show in Detroit had plenty of its namesake around, mostly for the automotive industry. That’s appropriate because of the location, but the emphasis goes beyond the traditional car battery. There were batteries of all shapes and sizes and the need for them crossed into many industries.
It’s not just the batteries themselves, though. There are many companies and industries looking to improve the batteries’ efficiency—especially as more are investing and looking into electric vehicles (EVs) as the next evolution for on- and off-highway vehicles.
The revolution promised a few years ago with the rise of Teslas and other automotive vehicles hasn’t quite happened the way some imagined, though. Even with that, companies in industries such as agriculture, construction and especially mining see the potential and they need good technology and components to ensure a longer life. This is especially critical for industries that work in remote locations such as mines and where downtime and safety are critical aspects. Flexibility and understanding the environment and setting are critical.
Rod Dayrit, global business development director for the ZAPI GROUP, said, “For the given environments, we want to make sure our product is robust and reliable and is high-performing because of the markets we cater to.”
How to improve, though? New technologies and batter chemicals are part of the equation. Automation is also on many minds when it comes to improve the manufacturing process.
Using digitalization to improve processes
Digital transformation has been a major focus and priority for manufacturers the last several years. The ability to use technologies and concepts such as virtualization, artificial intelligence/machine learning (AI/ML) and digital twins, in particular, can help reduce upfront production costs.
Michael LaPerre, sales director for Hexagon Manufacturing Intelligence, said they’re emphasizing zero prototyping with off-highway vehicle manufacturing.
“Technology can help prepare and determine what you do before it’s done. We have the ability to increase iteration and test more ideas in a virtual environment that can then prove out its performance in the real world,” he said.
LaPerre said that, in the end, the testing process is about improving quality. Improving the quality of the work being done and the testing behind it, he said, will in turn improve the quality of the product design.
Puneet Sinha, senior director and global head of battery industry for Siemens Digital Industries Software, talked about how they used digital twins to work with their customers. “There are different priorities and we adhere to different circumstances with our customers. We also factor in size, cost and performance,” he said. “We take those things into account and we understand the requirements.”
Taking the initiative with product development
Eric Carneiro, sales director for BorgWarner, said one of the company’s big priorities is working with the battery technology they currently have.
“We want to improve efficiencies with the current product and improve power and efficiency with what we have,” he said.
Carneiro noted this is important because there has been a lull in the industry as a whole due to after-effects from the COVID-19 pandemic and the supply chain challenges. As a result, companies are holding onto their equipment longer than they might have.
“Original equipment manufacturers (OEMs) are rethinking their development cycles and are slowing down,” he said.
For the off-highway industry, they might be a step behind adoption compared to commercial vehicles, but Carneiro is confident about the future, believing industries will get there in due time.
Woldemar d'Ambrières, global marketing manager for batteries at Arkema, talked about how they’ve worked with customers for up to 25 years in some cases with Lithium-ion batteries and improving the technology inside the battery and developing solutions to help customers realize their potential.
James Labonte, vice president of North American sales for Turntide Technologies, talked about their axial flux motors and how they’re taking a wider view when it comes to development.
“We’ve spent a good portion of time and money to improve not just the internals, but the production line,” he said.
For Turntide, it’s as much about the long game as it is about their immediate customer needs as axial flux motors, which were once viewed as cost-prohibitive, are starting to gain traction. They’re working on scaling up production and bring costs down. Testing also plays a key role.
“We simulate everything,” he said. “We correlate the data to the model and go through many iterations and with the test data, we end up with a very robust and accurate model.”
Adapting and improving battery production through automation
Rockwell Automation, which is known for controllers and software, among other things, is embracing their new industry and bringing their experience to this new industry.
Annisha Vaughn, NA sales manager, EV and battery for Rockwell Automation, said her company is committed to developing batteries through machine building, stacking machines, software solutions and emulation.
“We’ve gained a lot of expertise and brought in many battery industry personnel to help provide insights,” she said. “We’re packaging that with our services and solutions.”
She added how they’re also trying to engage early with their partners and the importance of greenfield facilities and outlining the process before planning out their design.
Festo is another company making inroads into the battery industry. While not known for developing batteries or systems designed to make them, their prior experience has, like Rockwell, made the transition easier for them as they work to improve the production process for companies.
“Automation is what we do. We’re all about improving productivity,” said Jarod Garbe, industry segment manager – automotive at Festo. “We have a long history in automotive and we’re able to use what we know and adapt products as the market changes.”
They highlighted a high throughput dry-room electrode assembly of EV batteries as well as Festo AX, an artificial intelligence/machine learning (AI/ML) system to lower energy use and improve predictive maintenance.
“Our system watches and understands what’s normal and anomalous,” Garbe said about the AI/ML system. “It recognizes the patterns and process and improves uptime for the OEM.”
There are many challenges ahead for industries such as mining, agriculture and construction, which are the bedrock for the off-highway industry. Batteries help these vehicles run better and longer in more remote and dangerous locations. They’re only as good, though, as the work put in behind the scenes through research, testing and product development.
The Battery Show proved there are many out there putting in the time to improve automation and innovation so their machines can run faster and longer than ever.