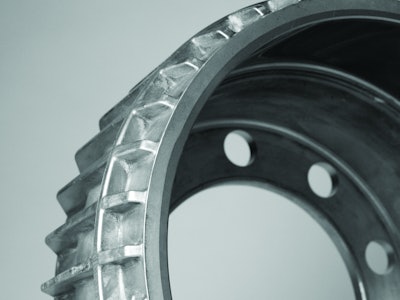
Composite materials and metal matrix composites (MMC) have been tackled numerous times in the pages of OEM Off-Highway magazine, especially as of late to help combat the extra weight carried by addition components in the engine and emissions systems. Light weighting also allows for a more fuel efficient vehicle; and oftentimes the composites can be made to be stronger and more durable than other materials, helping to keep the equipment running in the rugged conditions of the off-road industries.
But, while there are dozens of benefits to composites, there are shortcomings such as inconsistency in the blending process. While the same units of material input can go into each batch, the blend can be slightly different each time. Jim McManus—the new business development manager of Century Inc. 3+ LLC, a Traverse City, MI-based composite materials and extruder system manufacturer—claims that “over the last 40 to 50 years, the Achilles Heel of producing MMC components has been the ability to mix the ceramics consistently, as well as their cost. The key to making this work is to make the composite material consistently and affordably.”
The company used to be exclusively a manufacturer of extrusion machine parts for a number of years, explains McManus. When Century entered into the extrusion business as an OEM, it began making single- and twin-screw extruders. “We ran across a twelve ring extruder technology and bought it,” he says. “Our struggle was to find a commercial use for it. The technology is so highly efficient that at times it was ‘too good’,” he explains.
Century Inc. developed its 12-screw Ring Extruder compounding technology to allow for low-shear mixing and melting, as well as devolitization and reactive processing. The design is for a more elongational mixing style featuring twelve co-rotating, fully intermeshing, self-wiping screws that rotate around their own axes rather than around a single stationary core. The Ring Extruder brings automation to a previously batch process of manufacturing metal matrix composite components.
The smaller channels for throughput result in thinner material thickness and shorter diffusion paths for volatiles and reactants. The twelve screws allow for increased mixing without needing multiple kneading or high shear elements. The technology delivers evenly dispersed, mixed composites while minimizing the degradation of any sensitive resin components.
Feather-light strength
“The technology that we use selectively places the MMCs where it’s needed, and then the rest of the component is the light weight alloy,”—a technology commonly referred to as ‘selective reinforcement’ explains McManus. In the case of Century’s brake drum component, “at the end of the day, you get a brake drum that weights almost half, about 45% weight savings.”
The preform, when cast, is nearly 70% air and 30% silicon carbide ceramic, acting like a giant sponge when the molten aluminum is poured over and soaked into the preform. The component is then 70% aluminum and 30% silicon carbide ceramic.
A dark grey region (see image __) represents a ceramic preform of silicon carbide ceramic made with the Ring Extruder technology. The preform is placed only in the areas where the composite properties, in this case mainly wear resistance, are necessary. “On a brake drum, you really only need the matrix at the wear surface area,” says McManus.
If the whole brake drum were to be made of MMC, it would be more expensive to machine. By simply placing the composite material where it is needed, machining costs are reduced, lowering overall price.
Benefits outweigh their predecessors
The Ring Extruder technology is about enabling the movement of components that are normally cast in iron into other light weight alloys. “With MMCs you’re getting stiffness, light weighting, and wear resistance,” McManus says. “The connecting rod inside an engine may be a good use of MMCs, as it will allow you to use a lighter weight alloy for the connecting rod, and where it hooks on to the piston head you have a ceramic preform cast for wear resistance.” Clutch plates, rotors, piston rings, and cylinder liners are just a few of the many applications where MMCs could and are being used.
In trucking and haul truck applications, companies are always trying to find ways to lighten the vehicle weight to allow for a higher payload. Multi-axle vehicles holds multiple brake drums “and with savings around 50 lbs. per brake drum, you’re talking a lot of weight savings,” says McManus.
Logistically, the lighter weight of the components also allows shipping of approximately twice as many components per pallet, reducing shipping costs and overall fuel costs for delivery fleets. The commercial market is already investing in more costly light weight technologies, such as aluminum hubs and composite bumpers and panels. The mentality exists that light weighting, while usually more expensive, is worth the investment.
Century’s MMC brake drum technology has, thus far, outperformed its cast iron predecessor. The aluminum material is not only lighter than traditional cast iron, but also dissipates heat faster, solving a common problem of heat checks which tend to propagate in the cracks. The usual rigidity of cast iron is given more ductility to allow the part to flex, thanks to the aluminum; and calculations have shown the silicon carbide wear surface of the brake drums will allow them to last between 1.5 and 2 million miles, outlasting the life of the vehicle itself. This is particularly beneficial for military applications where lifecycle is a major concern for the safety and effectiveness of soldiers.
Militant ambition
Century Inc. is currently prototyping parts for specific military vehicle platforms. The company has prototyped parts for the FMTV, and TARDEC (Tank Automotive Research Development and Engineering Center) is currently evaluating Century’s aluminum MMC brake drum. By replacing the Stryker’s current heavy cast iron and steel brake drums with the lighter weight alternative, by some estimates, “We could save an immediate 1,000 lbs.* on the vehicle,” says Randal Gaereminck, associate director for engineering for TARDEC. “That gives a manager the option of adding more gear, technology, food or fuel—whichever is most beneficial to the mission.”
*The 1,000 lb. weight reduction estimate is due to the multiplying effect of un-sprung mass. Each pound of un-sprung weight saved in a component is equivalent to 3-5 times as much weight in sprung mass. For example, with a 45% weight reduction, the Stryker could take up to 250 lbs. of un-sprung mass from the wheel-ends, which is equivalent to nearly 1,000 lbs. of weight savings elsewhere in the vehicle.
Outside of its proven brake drum technology, Century has also manufactured MMC armor panels for a DARPA (Defense Advanced Research Projects Agency) Armor Challenge (see sidebar for more information).
Considering how heavy weaponry can be on military vehicles, light weighting technology allows for more vehicles to be equipped with weapon systems such as the CROWS (common remote-operated weapon system) unmanned system. CROWS is often mounted on Humvees (or HMMWV - high mobility multipurpose wheeled vehicle) and enables gunners to accurately engage targets viewed on a computer screen from the safety of the armored vehicle. “CROWS weighs approximately 300 lbs. If a military vehicle were to utilize our lighter weight brake drums on the vehicles, they’d save around 400 lbs. That allows them to equip the vehicle with CROWS and still save 100 lbs. of weight, while keeping the soldier safe from harm,” says McManus.
“Weight reduction really does add to survivability,” he continues. “It enhances payload performance and protection.” The benefits to weight reduction reach beyond the safety of soldiers, and into every day opportunities to increase fuel efficiency, reduce maintenance costs with longer component life, increase payloads, and reduced material and machining costs.