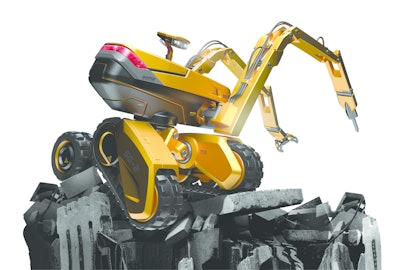
With two digging arms that fold down compactly, the remote controlled ARMB excavator solves many of the problems currently experienced on construction sites due to the limitations of the typical excavator.
Human error and negligence can be extremely costly, and result in lower construction quality, project delays, increased operating costs and higher risk of job site injury. Automated and robotic systems can provide a solution to these problems.
Another issue with current excavator designs comes from limitations of the machine’s movement in narrow construction sites where the arm cannot be fully unfolded and movement within the site is limited. The typical excavator also does not travel well on uneven ground. Also, if a part needs replacing on the digging arm, the whole machine needs to be temporarily put out of service.
ARMB has both a caterpillar track and wheels, which means it can move easily on many kinds of terrain – including steep slopes and stairs. Its functionality can be adjusted to suit the application.
The remote-controlled excavator also has two arms for efficient digging. They fold down flat to sit compactly at the sides of the machine when not in use.
Socket-type equipment can be replaced quickly and easily. This type of equipment does not need cables; connections are formed automatically when the parts are mounted.
ARMB is operated by remote control to reduce the risk of human injury. The control unit has a comfortable silicone casing. Its joystick commands six directions: anterior, posterior, left, right, right rotation, and left rotation. Fine movements can be easily directed. ARMB is further equipped with a camera and light. These pop up when needed from the roof of the excavator. The operator can view the footage on the remote control unit’s LCD screen.
Designer:
Wooseok Suh
[email protected]