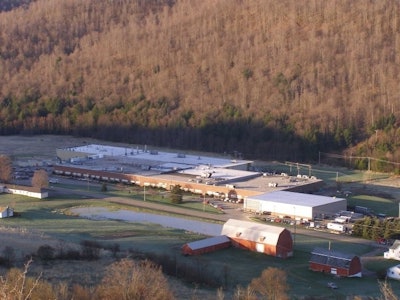
A recent research and development process resulted in the development of a large dense component that goes into equipment used in an extremely challenging corrosive precious metal mining process. The two-year development process required the development of a new powder and processing parameters, as well as investment in equipment that could machine larger shapes. The result has enabled Morgan to design and manufacture large cross sectional parts with uniform density and uniform grain size, making the material less susceptible to catastrophic failure in the field. The new material’s properties increase the part’s life such that it can be replaced during planned maintenance, rather than requiring an emergency shutdown. Precision pre- and post-firing machining produces tolerances and surface finishes that make the part easy to install in the field, further reducing mine operations costs.
Seeking materials for use in high pressure acid leaching autoclaves
Precious metal mines in the Southwest U.S., Southeast Asia, and Western Australia often use a high pressure acid leaching (HPAL) autoclave process to strip out minute amounts of precious metals from tons of raw ore and then reconstitute it to pure nickel, platinum and gold.
Large machines extract the precious metals using the HPAL process; the autoclave streams use valves to allow fluid to go from one autoclave to the next. The hot acid ore running through the process is extremely erosive and corrosive, and is running at very high pressure. Temperatures reach as high as 600 F/315 C, with pressures of 500 psi.
With a very low pH and the ability to cut through most materials, the hot acid causes a tremendous amount of wear and tear on plant and equipment. Equipment valves for HPAL must be made of extremely robust material to be able to withstand these conditions. Mine operators were finding that some materials, especially those made of conventional pressureless sintered silicon carbide (SiC), were not holding up, and they sought a more robust specialized carbide material.
Morgan Advanced Materials conducted a research and development project for an Australian precious metal mining operation at its Seals and Bearings facility in the United States. This Morgan facility develops highly engineered, very specialized materials needed for key aspects of rotating equipment used in challenging environments. Examples include advanced carbon graphite and SiC materials for friction and wear applications, including seals, bearings, vanes and rotors.
Challenges of making large ceramic components
The Australian mining project involved the development of a very large, shaped, structural wear valve. In addition to developing the material properties, the project included development of manufacturing and machining capabilities to provide finished components that would be ready for installation.
Manufacturing large SiC ceramic components involves the use of high temperature vacuum sintering to fire the material. It is extremely difficult to remove dense components with a large cross section from the furnace cycle in one piece – and without any cracks. The large valve component shapes required for this application are nearly fully dense, and have very large cross sections. Not only did the project require a large cross sectional part, manufactured as one high quality piece, it also required precision pre- and post-fire machining. The difficulty was far greater than, for example, developing rings with diameters of up to 10-20 in. (25-51 cm), because such rings have much smaller cross sections.
The HPAL equipment valve project had numerous challenges. First of all, the raw material particle size distribution had to be tailored to improve the thermal conductivity to allow sintering of very large cross sections. The grain size variation using standard material would have led to catastrophic failure—both thermally and mechanically due to internal stress.
Secondly, the spray-dried agglomerate size had to be adjusted to allow for pressing of large cross sections. Morgan invested in special machining equipment capable of holding large components, weighing up to 100 lbs. (45 kg).
The final material challenge was the development of a furnace profile capable of sintering very thick cross sections of material to uniform grain size and density. The R&D team achieved the desired material properties by careful manipulation of thermal profiles, atmosphere profiles, and packing methods within the furnace.
In addition to the material development work, Morgan invested in special diamond grinding equipment and tooling so machining could complete tolerances and surface finish requirements and ensure they would be ready for installation. The components were tested in the HPAL autoclave valves under full operating conditions and demonstrated their ability to withstand the environment and provide one year of working life or more. This performance consistency is a key feature for the mining operation, because it facilitates planned maintenance, rather than costly emergency shut downs resulting from unexpected component failure.
The part’s material properties include a density of 3.17 g/cc, versus conventional pressure-less sintered SiC at 3.13 g/cc.
With a hardness of 2800 kg/mm2, the material is one of the hardest substances known to man and has a compressive strength of up to ten times that of steel. It is unaffected by even highly corrosive fluids and has a temperature resistance of up to 3,000 F/1,649 C.
Since the original development process, similar products have been developed for precious metals mines in the Southwest United States, Southeast Asia, and Western Australia.