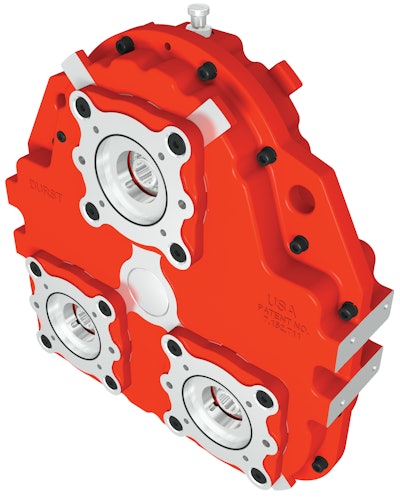
From wheat combines to off-shore oil drilling platforms, virtually all industrial equipment that incorporates heavy-duty hydraulic systems need customized pump drives. The vast quantity of specialized applications and various pump drive size requirements make any model standardization nearly impossible.
Previously, pump drives had to be purpose-built with hundreds of unique components to satisfy all the configurations required by OEMs. This painfully slow process resulted in high production costs, massive parts inventories and long lead times.
A team of engineers sought to find an alternative to constantly designing individual unique pump drives that in the end were incompatible with other applications. Starting from the beginning, the team opted for a complete redesign and focused on a revolutionary modular pump drive platform—a major leap forward in the way the pump drive market was approached.
To make customization the starting point of their pump drives rather than the last step, the team of pump drive engineers turned to a new paradigm in modular design: Design for Customization.
A new approach to modular design
Modular design is a well-established, even universal, industrial engineering principle. Modularity is very broadly defined. At its most basic, it is the use of independent, standardized or interchangeable units to serve a variety of functions. How engineers choose to address those multiple functions, user requirements and production specifications is what defines the established paradigms for modular design.
- Basic function modular design: A single-function unit is designed to do one job to extend a system’s existing functionality, with no further customization: it’s an add-on, and one size fits all.
- Auxiliary modular design: This approach means creating multiple basic function modules, each with one specific job; the modules can be assembled in different ways to create a variety of different products.
- Adaptive modular design: An adaptive module approach takes parts of an existing system or product and adapts and incorporates them into a new system or product.
- Non-modular modular design: A non-modular module may sound like an oxymoron, but it is a fact of life in modular design. A non-modular module is any basic, auxiliary or adaptive module that has to be redesigned and rebuilt individually for specific tasks to meet a customer’s needs — a technically challenging and expensive task. This was the approach used with non-modular pump drives: organically creating individual solutions to individual customer needs. Each created a new SKU, only usable by a small fraction of the customer base and required a massive inventory of spare parts. The basic modules were not all that dissimilar, but they could not cover the entire range of market requirements with at least some degree of individual customization to each. [1]
The new paradigm: customize first, manufacture second
The challenge the engineers faced in their redesign of the pump drive was that customization was the rule rather than the exception. Virtually every pump drive had different requirements, whether in size, componentry or capacity. Mass production of a single universal module would be impossible. The permutations and combinations were almost infinite; a modular design would still essentially require building a unique pump drive for every customer. But, the new Design for Customization approach to modular design addressed this challenge.
Design for Customization is a simple yet novel approach to modular design that evolved in the software and computer industries, where continual customization to ever-changing products was the norm. The approach is used when it is impossible to foresee all the contexts, conditions and customization needs customers may require. It is the process of designing for complete unknowns.
In practice, each individual customer designs the module by describing an application and its requirements. Yet, that module is not a one-of-a-kind. With a customization design approach, one modular design can meet the requirements of multiple customers. It simply means designing backward.[2]
Minimizing components to maximize customization
Using the Design for Customization approach, the team of pump drive engineers parsed through multiple existing customer specifications across industries and hydraulic applications to determine how much pump drive functionality could be contained in the smallest housing possible. Then they determined the minimum number of components that would have to be manufactured to customize a pump drive to meet any requirement; when finished, they had reduced the number of individual components from 317 to 96. They also turned certain customization options into standard features, designing and patenting a wet spline connection to address the most common form of failure: fretting corrosion.
The next step was to design individual components for simpler, universal assembly and service procedures. For example, previous gear designs required a complicated assembly procedure, pressing shafts into bearings and gears through a pump housing, then painstakingly adjusting and shimming taper roller bearings. The new design, which incorporates solid-shaft gears and ball bearings, eliminated the complicated assembly procedure. The shafts, bearings and gears drop straight into the pump drive housing without further adjustments. The gears themselves were designed to be interchangeable across any pump drive configuration, and adapter groups were reduced to a single set of input adapters and output pads for any iteration. These changes, along with part count and design simplifications, allowed for a 4-hour reduction in assembly time for a complete pump drive.
Customized componentry — including driveline adapters, output and input disconnects, and other customer-configurable equipment — turn the core drive into specialty pump drives for specialty applications. The modular core late-stage customization further extends the range of application suitability for the products.
The customer’s data is the design
Using a combination of core pump drive gearing available in a wide range of ratios and configurations, plus dozens of customer-specified engine adapters, drive plates, input shafts, clutches, clutch housings, clutch shafts, pump pads, spline adapters, input and output DLAs, the modular design is defined by the customer’s requirements and specifications. The customer completes an Application Data Sheet to specify the design of the pump drive. Then, through lean cellular manufacturing processes, the customized module is assembled from the specified components.
Because Design for Customization was employed on this platform, an application-specific pump drive variant can be produced in a fraction of the time that is required for a one-off design. With the Design for Customization method, manufacturing lead times have been reduced from 8-12 weeks to 2-4 weeks — dramatically improving availability while sharply reducing costs.