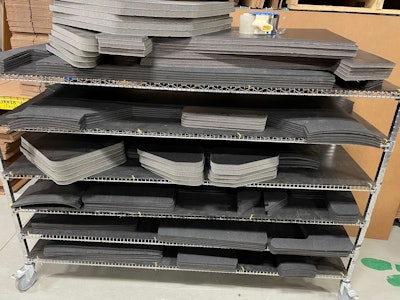
Construction equipment manufacturers that have too many stock-keeping units (SKUs) spend more time finding, sorting, handling, and organizing parts. This adds labor costs, requires more storage space, ties up cash in inventory, and increases tax liabilities. Parts kitting reduces the number of SKUs and improves operational efficiency during assembly and across the organization. The benefits range from streamlined purchasing and receiving to more efficient inventory management and accounting.
Today, companies that buy kitted parts can save time and money in five important ways: faster assembly, reduced overhead, volume discounts, reduced packaging waste, and fewer picking errors. Construction equipment manufacturers that combine parts kitting with assembly packaging can extend these benefits since all of the parts that are needed for a build are arranged in order of installation. The part that an installer needs first is on top, the part to install next is below it, and so on.
Not all kitted parts are candidates for packaging like this, however. For example, some of the molded parts for an excavator are used inside the cabin while others are used in the engine bay. Workers don’t install all of these parts at the same time, and the order of installation may not be as important as with the custom-cut acoustic insulation panels for the cabin. By partnering with the right supplier, manufacturers can realize the benefits of parts kitting while sourcing kits that support their specific assembly practices.
1. Faster Assembly
Kitted parts are faster to assemble because everything an installer needs arrives together and in the same box. In other words, installers don’t have to search for parts on shelves or wait for pickers to pull stock for them. With assembly packaging, installers won’t have to dump out a box of parts on a table, sort through similar-looking components, and figure out what to install first. That’s especially important for assembly operations with complex work instructions.Kitting groups related parts together to reduce the number of SKUs for greater efficiency.Elasto Proxy
2. Reduced Overhead
Parts kitting reduces the number of SKUs that manufacturers need to order, receive, store, and pay for. Buying all of the parts from a single supplier also supports vendor consolidation, which means fewer suppliers to manage and measure. If your company uses just-in-time (JIT) inventory, a box of kitted parts can move from your dock to the assembly line and bypass the warehouse, reducing your need for floor space and shelving. You’ll also free up cash since you won’t pay for parts until they arrive.
3. Volume Discounts
With construction equipment, the price of a part like a vibration mount may increase over time. In addition, it’s usually more expensive to buy one-off items instead of making regular purchases from a vendor you work with regularly. When you buy kitted items based on your production schedule, you may be able to get a volume discount since your supplier is regularly selling you more parts in fewer shipments. The right supplier may even be able to integrate your parts forecast into its ordering system.
4. Reduced Packaging Waste
Related parts that fit inside a standard cardboard box don’t require special packaging like the dunnage bags that secure truck parts during transport. Cardboard boxes can be recycled, of course, but kitting can also reduce the number of incoming boxes that you need to store and break down in the first place. In addition to reducing waste, it promotes operational efficiency since workers don’t have to make more trips to the dumpster. Reducing the number of incoming boxes also supports corporate sustainability initiatives. Kits can include taped parts that arrive ready to install.Elasto Proxy
5. Fewer Errors
Because kitting reduces SKUs, it reduces the risk of errors during purchasing, receiving, warehousing, picking, and payment. For example, when a buyer adds a line to a purchase order, that PO line can contain all the parts needed for a build. This reduces the risk that a buyer will forget a line item or add the wrong item to the PO. If you use assembly packaging, however, a kit will probably contain only what you install at the same time.
6. Parts Kitting Plus Assembly Packaging
Parts kitting for construction equipment provides business benefits, but kitting combined with assembly packaging can further promote production efficiency. Consider the example of a manufacturer that orders a kit with 25 similar-looking acoustic panels for an excavator cabin. An assembler that opens standard packaging must look for the panel to install first. Since it’s easy to confuse components, the wrong part gets picked. The assembler then dumps the box on the worktable, searches for each part as it’s needed, and walks back and forth to the line. This waste of motion is inefficient – and expensive.
Meanwhile, another worker opens assembly packaging that contains the same 25 kitted components. There’s no confusion about which acoustic panel to install first since it’s on top of the other parts. The assembler just follows the work instructions and removes each part from the box when it’s time to install it. There’s no searching for parts, no need to dump them on the table, and no walking back and forth from the table to the line because the wrong part was picked. Assembly is faster, and that saves the manufacturer time and money.
In this example, the headliner is on top and installed first. The acoustic insulation that’s installed along the sides of the cabin is installed last, so these parts are on the bottom of the cardboard box. The same kit could even contain floor mats if those parts are installed at the same time. If that sounds efficient to you, consider the combination of assembly packaging with just-in-time inventory. Kitted items travel in a single box right from the receiving area to the assembly line, bypassing the warehouse and all its associated costs.
For even greater efficiency, kitting and assembly packaging can be combined with parts taping. Unlike metal or plastic fasteners, adhesive tapes don’t require hand tools. Adhesive taping also has advantages over adhesive spraying, which requires time-consuming setup and cleanup while raising concerns about environmental health and safety. By partnering with the right supplier of kitted parts, construction equipment manufacturers can increase efficiency and use labor resources wisely at a time when workers are hard to find.
____________________
Roberto Naccarato is the sales and marketing manager for Elasto Proxy, a Canadian-based fabricator of industrial rubber products for the heavy equipment industry.