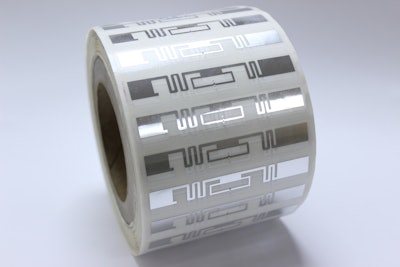
RFID tags can be read at multiple stages of an assembly process to guarantee manufacturing integrity and efficiency.
When people hear the term RFID (radio frequency identification) they typically think of credit cards used in the “tap to pay” option upon checkout. While this is indeed one of the uses of RFID technology, it is also found extensively in other applications in a variety of market segments. One of the most established market segments for the use of RFID is the apparel industry. The benefits and cost savings associated with RFID versus other identification methods such as barcodes and QR codes have long been proven. While the use of UHF (ultra-high frequency) RFID tags is prevalent in retail channels, there is growing penetration into other industries such as food, health care, agriculture and vehicle production.
Before delving into the possible use cases for RFID in vehicle manufacturing, it is important to understand RFID and its benefits.
RFID Defined
There are different types of RFID such as UHF, HF (high frequency), NFC (near field communication) and LF (low frequency). In this article, we will concentrate on passive UHF RFID, which typically operate in the frequency band of 865-928MHz. This is also called RAIN RFID, and is primarily used for inventory control and track and trace applications due to its ability to be read from greater distances.
RFID tags are constructed of a substrate, antenna and IC (integrated circuit) and typically have a self-adhesive backing and printable face stock if you are using them in label form. When you read or “wake up” an RFID tag, the reader/antenna energizes the tag using radio waves and the tag sends back information stored on the IC. The major benefits to RFID over barcodes and QR codes are as follows:
- Line-of-sight reading is not needed, so there is flexibility in placement of reading hardware as well as the tags themselves on your items.
- Multiple tags can be read at once, reducing time and labor thereby also saving on costs and increasing accuracy, as well as freeing labor to concentrate on other tasks.
- RFID tags have security features and varying degrees of memory size ensuring that a tag’s unique digital identity cannot be compromised or copied.
- RFID tags can come in label format so a barcode or QR code can be added along with any visual data needed for other stages in the manufacturing process.
While inventory control has been an exemplary use case for RFID implementation in the vehicle manufacturing industry, there are several other applications where RFID has clear benefits especially when it comes to vehicle manufacturing.
1. Asset Tracking
Manufacturing equipment, tools and other hard assets, such as returnable transport containers used in the manufacturing process, tend to be expensive and mobile. These assets can often end up intentionally or unintentionally misplaced, whether that is somewhere within a manufacturing space or moved outside. Not only are time and labor wasted in locating these assets, but if theft is involved, additional costs are incurred to replace them. Assets with RFID tags have their own unique digital identity. With the right RFID system in place, these assets can be located quickly and efficiently and/or prevented from being moved in the first place.
2. Manufacturing Efficiency & Error Proofing
One of the fastest growing applications of RFID in vehicle manufacturing is error proofing or manufacturing excellence. Take for instance the use of RFID tags in seating components. Not only are embedded RFID tags being used for inventory control, but they are also used to ensure the correct components are used in the intended assembly. When you consider the number of seating styles and trim levels, you can imagine the costs associated with reworks, recalls and work stoppages to fix incorrect components being used on a vehicle. RFID tags can be read at multiple stages of an assembly process to guarantee manufacturing integrity and efficiency.
3. Anti-Counterfeiting
Given today’s global supply chains, the threat of counterfeit components and the repercussion of their use is real and costly. While this might be more apparent in industries such as health care and cosmetics, the use of unapproved substitutes in vehicle production can lead to safety concerns, recalls, potential lawsuits and damage to brand reputation.
RFID deploys password protection, locking, encryption and blockchain security measures to help make the information as secure as possible compared to other technologies, such as barcodes and printed information, that can easily be copied, replicated and read by others.
Conclusion
RFID technology is ushering in a new era in vehicle manufacturing, emphasizing safety and efficiency. The trend of integrating RFID systems at every stage of production, from component sourcing to final assembly, is poised to reshape the industry's future. As manufacturers worldwide embrace RFID's potential, vehicle safety will undoubtedly reach new heights, setting the stage for a safer and more connected future on and off the road.
___________________________________________________
Gardner Bradlee is business development manager, automotive, at Avery Dennison Smartrac.