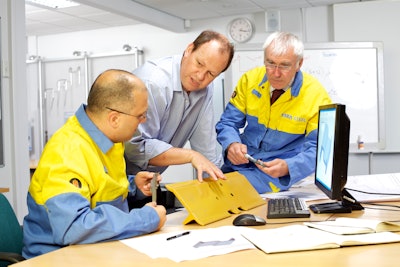
At bauma 2013, Tata Steel announced that it is extending its Early Vendor Involvement (EVI) program to German and European original equipment manufacturers (OEMs) in the lifting and excavating sector. With this unique scheme Tata Steel works with its customers' advanced engineering teams from the outset on design and development of new products and models. By tackling factors including strength-to-weight ratio, fatigue levels, processing costs and machine performance, the design, manufacturing and materials used can be optimized while reducing costs and weight.
Tata Steel recognizes that OEMs are constantly challenged to improve the performance and competitiveness of their machines, and is working hard to research and develop new products to support its customers in their work. By partnering with a company’s customer engineering team right at the start of the design process, its customers can benefit from Tata Steel’s technical and material expertise, and jointly fulfil both the market desire for enhanced performance and the customer’s own design challenges.
Terry Bennett, Marketing Manager, Lifting & Excavating says, “We have borrowed and tailored the EVI concept from our colleagues in the automotive division. The concept of lightweight has evolved in passenger vehicles, while the heavyweight world of off-highway engineering has historically been less concerned about weight reduction. But today the benefits are too big to ignore. It’s not just about the use of high strength steels; intelligent design is fast becoming a driving force in the evolution of the next generation of vehicle. And for lifting and excavating too, our EVI concept delivers a range of benefits.”
By simplifying certain design details, Tata Steel helped a global OEM at the forefront of equipment design, not only to reduce manufacturing costs for chassis production by €70,000 but more importantly, the joint design of the new generation of chassis are over 30% stiffer and more than 25% lighter compared to the previous generation.
Components including the cab and overhead protection should also be taken into account and high-strength steels can be vital for protecting occupants in the case of an accident. The use of ultra high-strength steels can play an important part in off-highway vehicle construction, drastically cutting the mass of these overhead structures whilst maintaining or even enhancing its structural integrity.
An overall reduction in the weight of a vehicle, particularly at the top, lowers its center of gravity and offers improved operating stability. In forklift applications it allows the better placement of counterweights. In all, it’s a trend towards using the mass of a vehicle more efficiently and effectively.
But the limitations of weld integrity can mean that lighter, higher-strength steels do not make a product any stronger. Tata Steel has also been developing new techniques to tackle this issue, including developing new manufacturing processes, like advanced pressing and forming techniques. Furthermore Tata Steel analysed how fatigue affects weld integrity allowing them to optimise design application in critical scenarios.
The EVI programme is one of the cornerstones of Tata Steel’s customer engineering offering, and has been successfully implemented in the automotive sector for over 15 years. It perfectly underlines the overall company approach of “Together we make the difference,” by forming close partnerships with its customers providing them with real benefits. As a result, Tata Steel has a track record in being able to offer lifting and excavating OEMs these benefits.